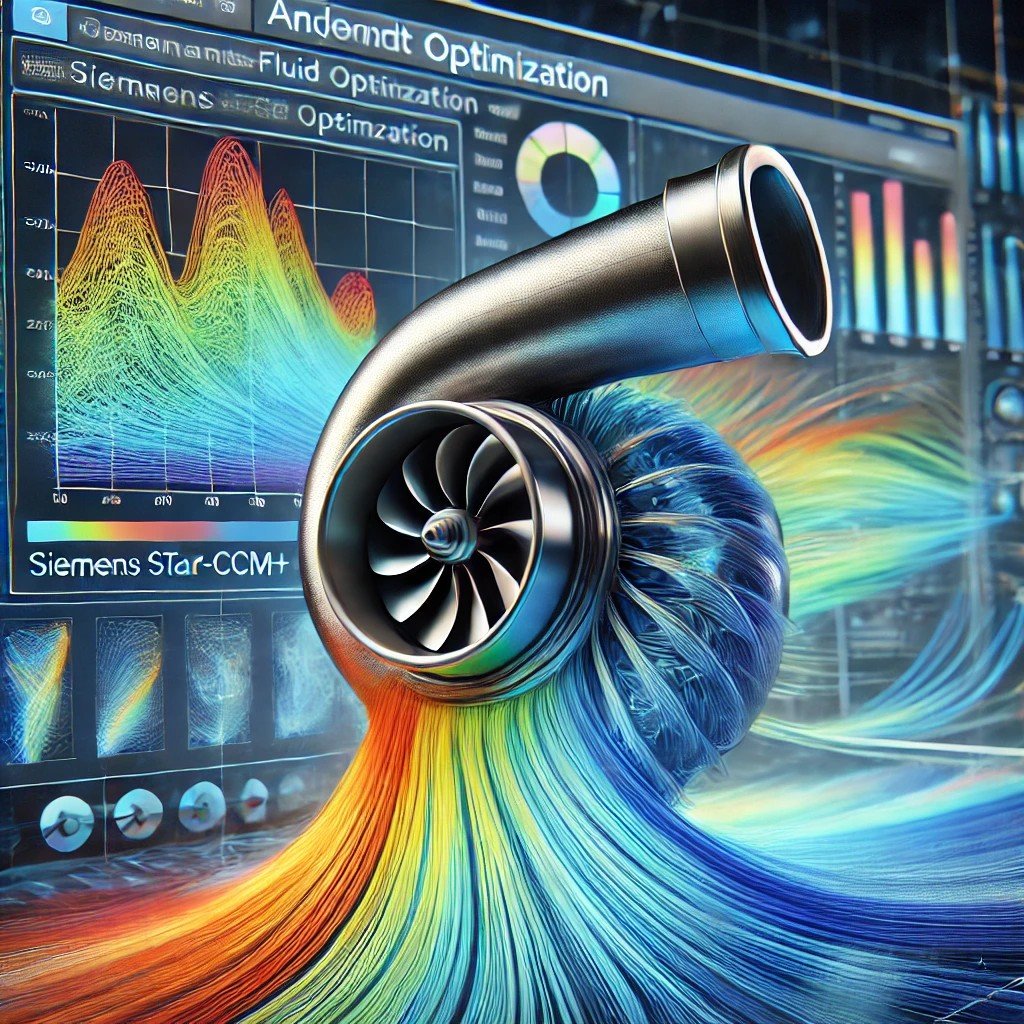
Adjoint Optimization at Full Speed: Engineering Design without the Guesswork
In high-performance engineering, speed and precision define success. Every iteration in a design cycle is a tradeoff between computational expense and finding the optimal solution. Computational Fluid Dynamics (CFD) has revolutionized design, but traditional optimization methods often require running thousands of simulations—an approach that's both time-intensive and computationally expensive.
Enter adjoint optimization, a technique that flips the script by providing gradient-based insights for rapid design refinement. With Siemens Simcenter STAR-CCM+, engineers can optimize complex geometries in real-time, reducing design cycle times while improving performance.
Why Adjoint Optimization?
Instead of blindly iterating through designs, adjoint-based optimization provides precise direction for shape modifications based on performance objectives such as drag reduction, pressure drop minimization, or heat transfer enhancement. Here’s how it changes the game:
Computational Efficiency – Adjoint methods compute sensitivities for all design parameters in a single simulation, drastically reducing computational costs compared to brute-force parametric sweeps.
Granular Insight – Engineers gain a pixel-by-pixel map of how geometry changes impact performance.
Automated Shape Optimization – Directly modifies designs without manual intervention, accelerating development timelines.
A Real-World Example: Turbocharger Optimization
Turbocharger aerodynamics demand peak efficiency under stringent space constraints. Traditional optimization might require running thousands of simulations, each with slight modifications to blade profiles and volutes.
With STAR-CCM+ Adjoint Solver, engineers can:
Identify high-sensitivity areas in a single adjoint run.
Directly morph blade geometries to minimize losses.
Reduce design iterations by up to 80%, cutting development time from months to weeks.
The new solver in version 2502 drastically improves adjoint residual convergence over version 2410, achieving smooth, efficient second-order convergence, reducing residuals by 10 orders of magnitude in just 80 iterations, and eliminating infinite loops.
Key Benefits of Adjoint Optimization in STAR-CCM+
1. Speeding Up the Design Process
Traditional CFD optimization: Requires thousands of simulations.
Adjoint-based optimization: Achieves the same goal in a single run.
2. Improved Design Exploration
Finds the most impactful shape modifications automatically.
Reduces reliance on trial-and-error, freeing up engineers for higher-value tasks.
3. Seamless Integration with Existing Workflows
Works within the STAR-CCM+ ecosystem, enabling engineers to integrate adjoint solutions with existing parameterized models and automated design loops.
Engineering the Future with Intelligent CFD
Adjoint optimization isn't just an incremental improvement—it’s a paradigm shift. By reducing simulation overhead and guiding shape refinement with precision, STAR-CCM+ empowers engineers to achieve optimal performance faster than ever.
For teams looking to drive innovation in automotive aerodynamics, turbomachinery, or industrial design, adjoint optimization delivers unmatched efficiency, reducing development cycles without compromising on accuracy.
Ready to Take Your Designs to the Next Level?
Harness the power of adjoint optimization in Simcenter STAR-CCM+ and leave traditional trial-and-error behind. Contact us today to learn how CFD-driven optimization can redefine your engineering workflow.