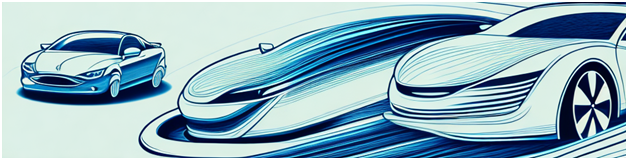
CFD for Automotive Aerodynamics
When we think of the sleek curves and impressive speeds of modern sports cars, we might assume that they are solely the product of cutting-edge engineering techniques and advanced materials. However, the truth is that the science of automotive aerodynamics has been evolving for well over a century. Today, one of the most important contributors to this field is computational fluid dynamics (CFD), which has helped designers and engineers to create vehicles that are faster, more efficient, and better able to meet the needs of their drivers and passengers.
The Evolution of Automotive Aerodynamics
Early Concepts and Designs
The history of automotive aerodynamics dates back to the earliest days of the automobile. As designers began to experiment with different shapes and sizes of vehicles, they quickly realized that certain factors - such as wind resistance and fuel efficiency - were intimately related to issues of airflow and drag. Early car models reflected a range of simple, often boxy designs that gave little thought to aerodynamics. However, with the introduction of more powerful engines and increased competition between manufacturers, automakers began to see the value in developing more efficient, streamlined designs.
One of the earliest pioneers in automotive aerodynamics was Paul Jaray, a Hungarian aeronautical engineer who worked for the German aircraft manufacturer, Luftschiffbau Zeppelin of Hindenburg disaster infamy. Many years before that incident though, Jaray led the wind tunnel testing fluid dynamics team responsible for the aerodynamic design of the company’s airships.
(Paul Jaray with 1/10 Scale model of a Zeppelin Airship in a Wind Tunnel)
But Jaray was fascinated with the idea of creating a car that would be more aerodynamic than any other vehicle on the market. Around 1922 he and a colleague, Wolfgang Klemperer, began designing an ultra-aerodynamic car based on the shape of the Zeppelin. They experimented with a range of different shapes and designs, eventually settling on a teardrop-shaped body that would minimize wind resistance and maximize fuel efficiency.
This design was licensed by The Tatra Company and produced as the model T77, and later the T77A.
Adolf Hitler loved Tatra cars and enjoyed driving them during his political trips around Czechoslovakia. Their innovativeness greatly influenced the designer, Ferdinand Porsche. The handbuilt T77A was beautiful, quiet and quite fast for its time, hitting a top speed of 150 km/h on only 75 horsepower. It is reasonable to wonder how the T77A could reach such speeds with so little power, especially considering the bulk of the vehicle and the density of the materials used during that time. The only way it could is by being revolutionary it its ability to limit the drag on the vehicle.
What is drag?
Drag is a force that acts in the opposite direction to the motion of an object moving through a fluid. It is caused by the friction between the fluid and the object and is proportional to the square of the speed of the object.
(T77 - Courtesy wheelsage.org)
What is a coefficient of drag?
The Coefficient of Drag (C.D.) is a dimensionless number that is used to quantify the relative resistance of an object to the flow of the fluid.
How do you calculate coefficient of drag?
The coefficient of drag is typically calculated using the following formula:
C_d = 2F_d/ (ρv^2A)
Where `F_d` is the drag force, `ρ` is the fluid density, `v` is the speed of the object, and `A` is the cross-sectional frontal area of the object.
The T77A model is widely regarded as one of the most aerodynamic cars of its time. With a reported coefficient of drag of 0.212, the T77A would rival the most aerodynamically streamlined cars of our day as well, such as the Tesla Model S and Lucid Air.
(courtesy Richard Owen – Supercars.net)
The Rise of Computational Fluid Dynamics (CFD)
In the latter part of the 20th century, the automotive industry began to turn to CFD to help solve the complex issues involved in creating better-performing and more attractive vehicles. CFD is a type of computer simulation that models the way that air flows around objects, allowing designers and engineers to test and refine their ideas before ever building a physical prototype to test in a wind tunnel or on the track. This technology revolutionized the way that new vehicle models were created, as it allowed designers to experiment with a range of factors from different angles and perspectives.
In the early 1980s, the use of CFD was limited to helping to define the basic shape of the car body, but largely in a supporting role of wind tunnel testing. With increased computing power, improved CFD algorithms, and enhanced turbulence models, CFD grew in use in the 1990 and early 21st century to include simulation and design of more complex fluid-structure interactions such as mirrors, ground effects, under-hood engine compartment, wheels and so on. It is increasingly replacing the wind tunnel and some cars have been 100% designed using on computer simulations. Today’s cutting edge includes aeroacoustics simulations to minimize on-road noise.
(CFD Generated Image Showing Predicted Flow Patterns Around a Tractor Trailer)
One of the key advantages of CFD is that it allows designers to create virtual wind tunnels, which can be used to test the aerodynamic properties of a vehicle in a controlled environment. This means that designers can experiment with a range of different shapes and designs, and quickly identify which ones are most effective at reducing drag and improving fuel efficiency. CFD has become an essential tool for automotive designers, and is used by every major car manufacturer in the world today.
Modern Aerodynamic Innovations
Today’s automobiles are the result of decades of aerodynamic refinement, which have resulted in an elaborate set of design considerations, including curves and slopes that help to minimize air resistance, and intricate vents and ducts that channel air in specific ways to maximize efficiency. Vehicles that are designed with these advanced aerodynamic features are consistently some of the most popular and effective on the market, prized for their speed, handling, and fuel economy.
One of the most significant recent innovations in automotive aerodynamics has been the development of active aerodynamic systems. These systems use a range of sensors and actuators to dynamically adjust the shape and configuration of a vehicle's body, in response to changing driving conditions. For example, some vehicles are equipped with active spoilers that can be raised or lowered depending on the speed of the vehicle, while others have active grille shutters that can open or close to regulate airflow and improve fuel efficiency. These systems have become increasingly common in high-end sports cars and luxury vehicles, and are expected to become more widespread in the coming years.
Overall, the evolution of automotive aerodynamics has been a fascinating journey, marked by innovation, experimentation, and a relentless pursuit of efficiency and performance. As technology continues to advance, we can expect to see even more exciting developments in this field, as designers and engineers continue to push the boundaries of what is possible.
The Science Behind Automotive Aerodynamics
Understanding Fluid Dynamics
At the heart of automotive aerodynamics is the science of fluid dynamics, which is concerned with the way that matter flows and interacts with other materials in the natural world. In an automotive context, this science deals specifically with the way that air flows around the exterior of a vehicle, generating drag and other forces that can affect performance. By studying these complex dynamics using advanced computational tools and engineering skills, designers are able to build vehicles that are both faster and more fuel-efficient.
The Importance of Airflow Management
One of the key elements of automotive aerodynamics is the management of airflow around a vehicle. This involves the strategic positioning of vents, grilles, hood scoops, and other features to direct air in the most efficient way possible. By channeling air to specific areas of the body, designers can make use of airflow not only to reduce drag but also to increase engine cooling, enhance handling, and reduce noise levels. Effective airflow management can also impact the way that a car looks - with sleek, angular designs that capture the eye and convey speed and power.
Perhaps the most commonly seen and noticed airflow management devices on the road today are the skirts along the sides of the underbody of tractor trailers, as seen for example in the image below.
(Wind Tunnel Testing of Navistar's "Catalist" Concept Truck, Including Skirts, at NASA’s Ames Research Center – Photo Courtesy of Navistar)
Reducing Drag and Increasing Efficiency
Of particular interest to automotive engineers is the issue of drag, which is caused by the resistance generated by the movement of air over the surface of a vehicle. To reduce drag and increase efficiency, designers may create shapes that are low and flat or incorporate features like underbody panels or air deflectors. Advanced materials like carbon fiber can also help to reduce a vehicle's overall weight, which can further decrease drag and increase fuel efficiency.
Another way to reduce drag is by using active aerodynamics, which involves adjusting various parts of the vehicle in real-time to optimize airflow.
For example, the Porsche 911 GT3 RS features an adjustable rear wing that can be set to different angles depending on the driving conditions. This allows for optimal airflow management, reducing drag and increasing downforce when needed for high-speed driving. The design of the GT3 RS adjustable rear wing was initiated with CFD and fine tuned in wind tunnel testing shown below.
(Porsche 911 GT3 RS Adjustable Rear Wing in Wind Tunnel Testing - courtesy Porsche)
Another example, the Lamborghini Huracan Performante, features active aerodynamics that adjust the front and rear spoilers to improve downforce and reduce drag, allowing for faster lap times on the track.
In conclusion, automotive aerodynamics is a complex field that involves a deep understanding of fluid dynamics and the strategic management of airflow around a vehicle. By incorporating advanced materials and technologies, designers are able to create vehicles that are both faster and more fuel-efficient, while also looking sleek and stylish on the road.
CFD in the Automotive Industry
The Role of CFD in Vehicle Design
Today, CFD is an essential part of the design process for most modern automobiles. By using advanced software and modeling techniques, designers and engineers can experiment with different ideas and concepts, quickly testing out new designs to determine which ones will be most effective. This allows companies to get new car models to market more quickly and at a reduced cost. CFD has even been used to create high-performance race cars, enabling teams to build vehicles that can outstrip the competition in terms of speed and handling.
One of the key advantages of using CFD in vehicle design is that it allows engineers to simulate the behavior of fluids and gasses around a car, without the need for expensive and time-consuming physical tests. This means that designers can quickly and easily test out different ideas, making tweaks and adjustments as needed to optimize the performance of the vehicle.
CFD Software and Tools
The software used in CFD is complex and constantly evolving, relying on a range of algorithms and computational models to simulate the behavior of fluids and gasses around a vehicle. Some programs may use finite element analysis (FEA) or other modeling techniques to generate accurate simulations, while others may rely on more simplified models based on fluid dynamics equations. In either case, the software is an essential tool for designers and engineers looking to create more efficient and effective automobiles.
One of the most popular CFD software packages used in the automotive industry is Siemens STAR-CCM+. This software is known for its accuracy and versatility, and is used by many leading car manufacturers to optimize the design of their vehicles. Other popular CFD tools include OpenFOAM and ANSYS Fluent.
Case Studies of Successful CFD Implementation
There are numerous examples of successful CFD implementation throughout the automotive industry. One notable case is the McLaren P1, a high-performance supercar that was designed using CFD to optimize its aerodynamic properties. The car features a range of advanced design elements, including active air ducts and innovative materials like titanium and carbon fiber. The result is a car that can reach speeds of up to 217 mph while still providing exceptional handling and fuel efficiency.
Another example of successful CFD implementation can be found in the design of the Tesla Model S. This electric car was designed using CFD to optimize its aerodynamics, resulting in a vehicle that has a drag coefficient of just 0.24. This makes it one of the most aerodynamic cars on the market, and contributes to its impressive range of up to 402 miles on a single charge. The Tesla Model S design team made heavy use of STAR-CCM+ CFD simulation software.
Overall, CFD has revolutionized the way that cars are designed and built, enabling engineers to create more efficient, effective, and high-performance vehicles than ever before. As software and modeling techniques continue to evolve, we can expect to see even more impressive advancements in the field of automotive design in the years to come.
Competitive Advantages of Adopting CFD
Computational Fluid Dynamics (CFD) is a powerful tool that can revolutionize the way automotive engineers design and develop vehicles. It is a simulation technique that allows engineers to visualize and analyze the behavior of fluids and gases in a virtual environment. By incorporating CFD into the design process, engineers can make more informed decisions and create better-performing vehicles. Let's take a closer look at some of the competitive advantages of adopting CFD.
Improved Fuel Efficiency
Perhaps the most significant advantage of incorporating CFD into the design process for automotive engineers is the ability to improve fuel efficiency. By reducing drag and streamlining airflow, vehicles designed with CFD can significantly reduce fuel consumption, saving drivers money and reducing environmental impact. With rising fuel prices and growing concerns about climate change, improving fuel efficiency has become a top priority for the automotive industry. CFD can help automakers achieve this goal by optimizing the design of a vehicle's exterior, including its shape, size, and aerodynamics.
CFD simulations can also help engineers identify areas of a vehicle that are creating unnecessary drag, such as the underbody, wheel wells, and side mirrors. By making small changes to these areas, engineers can reduce drag and improve fuel efficiency without sacrificing performance or safety.
Enhanced Vehicle Performance
CFD also offers a range of opportunities for enhancing overall vehicle performance. By testing out new design concepts and materials using advanced simulations, engineers can create cars that are faster, more responsive, and more stable on the road. This can be particularly useful for high-performance vehicles like racing cars, where even small improvements can mean the difference between victory and defeat.
CFD simulations can help engineers optimize a vehicle's suspension, brakes, and steering, allowing for better handling and control. They can also help engineers identify areas of a vehicle that are prone to overheating, such as the engine and brakes, and make changes to improve cooling and performance.
Reduced Environmental Impact
Finally, by using CFD in the development of new car models, the automotive industry can continue to advance sustainability and environmental responsibility. By creating more efficient cars with reduced emissions, automakers can help to reduce the carbon footprint of the transportation industry and combat climate change.
CFD simulations can help engineers optimize a vehicle's engine and exhaust system, reducing emissions and improving fuel efficiency. Below is an image from a type of CFD model common to the automobile industry – that of the selective catalytic reduction system on a diesel engine.
(CFD Simulation Showing Urea Injected into the SCR system of a automotive diesel exhaust)
CFD simulations can also help engineers identify areas of a vehicle that are creating excess noise pollution, such as the exhaust system or air intakes, and make changes to reduce noise levels.
Overall, the adoption of CFD in the automotive industry has the potential to revolutionize the way vehicles are designed and developed. By improving fuel efficiency, enhancing performance, and reducing environmental impact, CFD can help automakers create cars that are better for drivers, better for the environment, and better for the future.
Conclusion
The history of automotive aerodynamics is a long and fascinating one, chronicling the major milestones and innovations that have brought us to where we are today. With the help of CFD, designers and engineers are able to build cars that are faster, leaner, and better adapted to the demands of the modern world, offering a range of competitive advantages to automotive manufacturers and drivers alike.