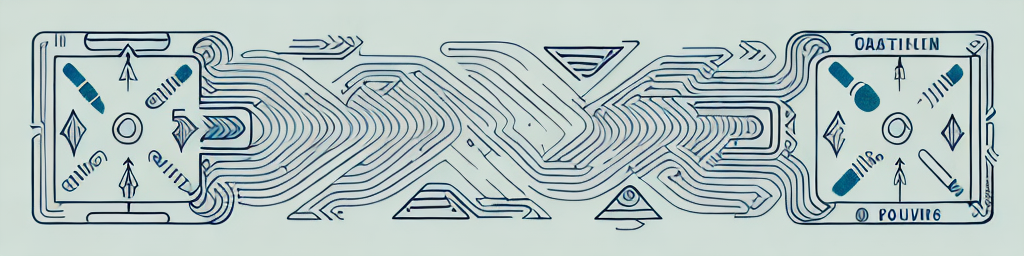
Leveraging CFD to Improve Static Mixer Efficiency
CFD Use to Optimally Balance Pressure Loss and Mixing Uniformity Across Static Mixers
Static mixers have been used for decades to efficiently mix fluids of varying viscosities and flow rates. However, achieving optimal mixing performance and pressure loss remains a challenging task for engineers. Fortunately, advances in computational fluid dynamics (CFD) have simplified this process by providing an accurate and efficient means of analyzing the performance of static mixers. In this article, we will explore the importance of pressure loss and mixing uniformity in static mixers, the fundamentals of CFD analysis, and how CFD can be used to optimize the design of static mixers.
Understanding the Importance of Pressure Loss and Mixing Uniformity in Static Mixers
Static mixers are widely used in various industries to mix and blend fluids. These mixers are designed to provide efficient and effective mixing of fluids with minimal energy consumption. However, the performance of static mixers can be affected by pressure loss and mixing uniformity.
Pressure loss occurs when a fluid traverses a static mixer, and this can lead to decreased mixing performance, reduced transport efficiency, and increased energy consumption. The pressure loss across a static mixer depends on many factors, including the mixer geometry, fluid properties, and flow rate. Engineers must take these factors into account when designing a mixer to ensure that the pressure loss remains within acceptable limits while achieving optimal mixing performance.
Mixing uniformity, on the other hand, determines how well the fluid is mixed within the mixer. Poor mixing uniformity can lead to incomplete reactions or incomplete mixing. Effective mixing performance relies on achieving mixing uniformity across the entire mixer. Uniform mixing means that every fluid particle comes into contact with every other particle within the mixer, ensuring that no regions of unmixed fluid exist. This requires an understanding of the flow characteristics of the fluids and the proper selection of mixing elements within the mixer.
The Role of Pressure Loss in Static Mixers
The pressure loss in a static mixer is an important factor that affects its performance. Pressure loss can occur due to various reasons, such as frictional losses, turbulence, and eddies. These losses can cause a decrease in the fluid velocity, which in turn affects the mixing performance of the mixer. Therefore, it is crucial to design the mixer in such a way that the pressure loss is minimized while achieving optimal mixing performance.
One way to minimize pressure loss is to reduce the mixer's length while maintaining the required mixing performance. This can be achieved by selecting the appropriate mixing elements and optimizing their arrangement within the mixer. Another way to reduce pressure loss is to increase the diameter of the mixer, which reduces the fluid velocity and the associated frictional losses. However, increasing the mixer's diameter can also increase its cost and size, which may not be desirable in some applications.
Achieving Mixing Uniformity for Optimal Performance
Mixing uniformity is an essential factor that determines the quality of the final product. A well-mixed product ensures that all the components are evenly distributed, and there are no regions of unmixed fluid. Achieving mixing uniformity requires an understanding of the fluid flow characteristics and the selection of appropriate mixing elements.
The selection of mixing elements depends on the fluid properties, flow rate, and the desired mixing performance. Mixing elements can be classified into two categories: passive and active. Passive mixing elements rely on the fluid's natural flow to achieve mixing, while active mixing elements use external energy sources, such as motors or pumps, to enhance mixing performance.
Passive mixing elements include helical elements, baffles, and static mixers. These elements rely on the fluid's natural flow to create turbulence, which enhances mixing performance. Active mixing elements include impellers, turbines, and propellers. These elements use external energy sources to create high shear forces, which enhance mixing performance.
In conclusion, pressure loss and mixing uniformity are critical factors that affect the performance of static mixers. Engineers must take these factors into account when designing a mixer to ensure optimal mixing performance while minimizing energy consumption and cost. Achieving mixing uniformity requires an understanding of the fluid flow characteristics and the proper selection of mixing elements within the mixer.
Fundamentals of Computational Fluid Dynamics (CFD) in Mixer Design
CFD is a powerful tool that enables engineers to design and optimize static mixers. The use of CFD analysis in mixer design provides several advantages, including reducing the need for costly and time-consuming physical experimentation, providing greater accuracy, and enabling engineers to optimize mixer design and performance, leading to energy savings and more efficient product mixing.
Static mixers are widely used in various industries, including chemical, pharmaceutical, and food processing, to mix fluids and improve product quality. However, designing an efficient static mixer can be challenging, as it requires a thorough understanding of fluid dynamics and mixing principles.
The Basics of CFD Analysis
CFD analysis involves breaking down complex fluid flow problems into smaller, more manageable pieces. A computer program then solves these smaller pieces, producing a visual representation of the fluid flow within the static mixer. Engineers can then use this visual representation to optimize the mixer's design and improve its performance.
CFD analysis can simulate various fluid flow conditions, including laminar, turbulent, and transitional flow regimes. It can also simulate the effects of different mixer geometries, such as the number of mixing elements, their shape, and their orientation.
CFD analysis can also provide insights into the pressure loss characteristics of the mixer, which is an important consideration in many applications. Pressure loss can affect the efficiency of the mixer and the energy required to operate it.
Advantages of Using CFD in Static Mixer Design
The use of CFD analysis in mixer design provides several advantages. Firstly, it reduces the need for costly and time-consuming physical experimentation, as CFD analysis is faster and less expensive to conduct. Secondly, it provides greater accuracy, since CFD analysis allows for more detailed visualization of fluid flow within the mixer. Finally, it enables engineers to optimize mixer design and performance, leading to energy savings and more efficient product mixing.
CFD analysis can also help engineers to identify potential problems with the mixer design before it is built and installed. This can save time and money by avoiding costly design changes and modifications.
In conclusion, CFD analysis is a valuable tool for engineers designing static mixers. It provides a detailed understanding of fluid flow within the mixer, enabling engineers to optimize the mixer's design and performance, leading to energy savings and more efficient product mixing.
CFD Simulation Process for Static Mixers
The CFD simulation process for static mixers involves defining the simulation parameters, carrying out the analysis, and interpreting the results to optimize the mixer design.
Defining the Simulation Parameters
The first step in CFD analysis is to define the simulation parameters. This involves defining the flow rate, fluid properties, and mixer geometry. Engineers must also specify the type of fluid flow, such as laminar or turbulent, which will affect the mixing performance and pressure loss characteristics of the mixer.
Analyzing the CFD Results
Once the simulation has been run, engineers must analyze the CFD results. This involves examining the visual representation of the fluid flow within the mixer and identifying areas of high pressure loss or poor mixing uniformity. Based on their findings, they can then optimize the mixer design to achieve improved performance.
Case Study: Optimizing Static Mixer Design with CFD
The benefits of using CFD analysis to optimize static mixer design can be seen in real-world applications. In this case study, we examine how CFD analysis was used to optimize the design of a static mixer.
Identifying the Problem: Pressure Loss and Mixing Uniformity
The engineers at the company had identified pressure loss and poor mixing uniformity within their static mixer. These issues had led to decreased mixing performance and increased energy consumption.
Implementing CFD Analysis to Improve Mixer Performance
The company used CFD analysis to optimize the mixer design. The engineers ran simulations, adjusting the mixer geometry and flow rate to achieve optimal mixing performance. The simulations also allowed them to reduce pressure loss across the mixer.
Evaluating the Optimized Design
Once the optimized design was implemented, the company saw significant improvements in mixer performance, with increased mixing uniformity and reduced pressure loss. This led to energy savings and improved product quality, making the optimized design a worthwhile investment.
Practical Applications of CFD-Optimized Static Mixers
The use of CFD-optimized static mixers has practical applications in a wide range of industries.
Industries Benefiting from Improved Static Mixer Performance
The improved performance of static mixers can benefit industries such as chemical processing, pharmaceuticals, food and beverage, and wastewater treatment. In chemical processing, for example, static mixers can be used to mix chemicals with different viscosities, while in food and beverage processing, they can be used to mix ingredients uniformly to create high-quality products.
Environmental and Cost Savings from Optimized Designs
CFD-optimized static mixers also offer significant environmental and cost-saving benefits. By reducing pressure loss and improving mixing performance, they can save energy and reduce the need for additional processing steps or rework. This, in turn, leads to reduced production costs and a smaller environmental footprint.
Conclusion
CFD analysis provides an accurate and efficient means of analyzing and optimizing the performance of static mixers. By understanding the importance of pressure loss and mixing uniformity in static mixers, and utilizing CFD simulation and analysis, engineers can design and optimize static mixers to achieve higher performance, decreased pressure loss and improved uniformity, benefitting a wide range of industries while reducing environmental impact and costs.