F3 / REACTING FLOW
Methods for accurately simulating chemically reacting flows are now available. These modern engineering tools are being called upon to design ground-breaking new technologies that are changing the way we live.
Chemically reacting flows combine aspects of physical chemistry and fluid dynamics and are often encountered in industry as well as everyday life. A physical prototyping, trial-and-error based approach to designing reacting flow systems is considered impractical due to long lead times and high costs. Digital models are now being used to research new chemically reacting processes and to test different concepts across a range of design conditions.
While combustion is the most widely simulated reacting flow phenomenon, applications in chemical synthesis, redox reactions, precipitation, and catalysis are also common.
Industrial use cases include fluidized bed reactors, gas turbine combustors, methane reformation, glass furnaces, solid fuel furnaces, biofuel production, fermentation and building fires. The continuous improvement of existing products and the introduction of new and innovative products, enabled through digital simulation, are determining the future winners and losers in these industries.
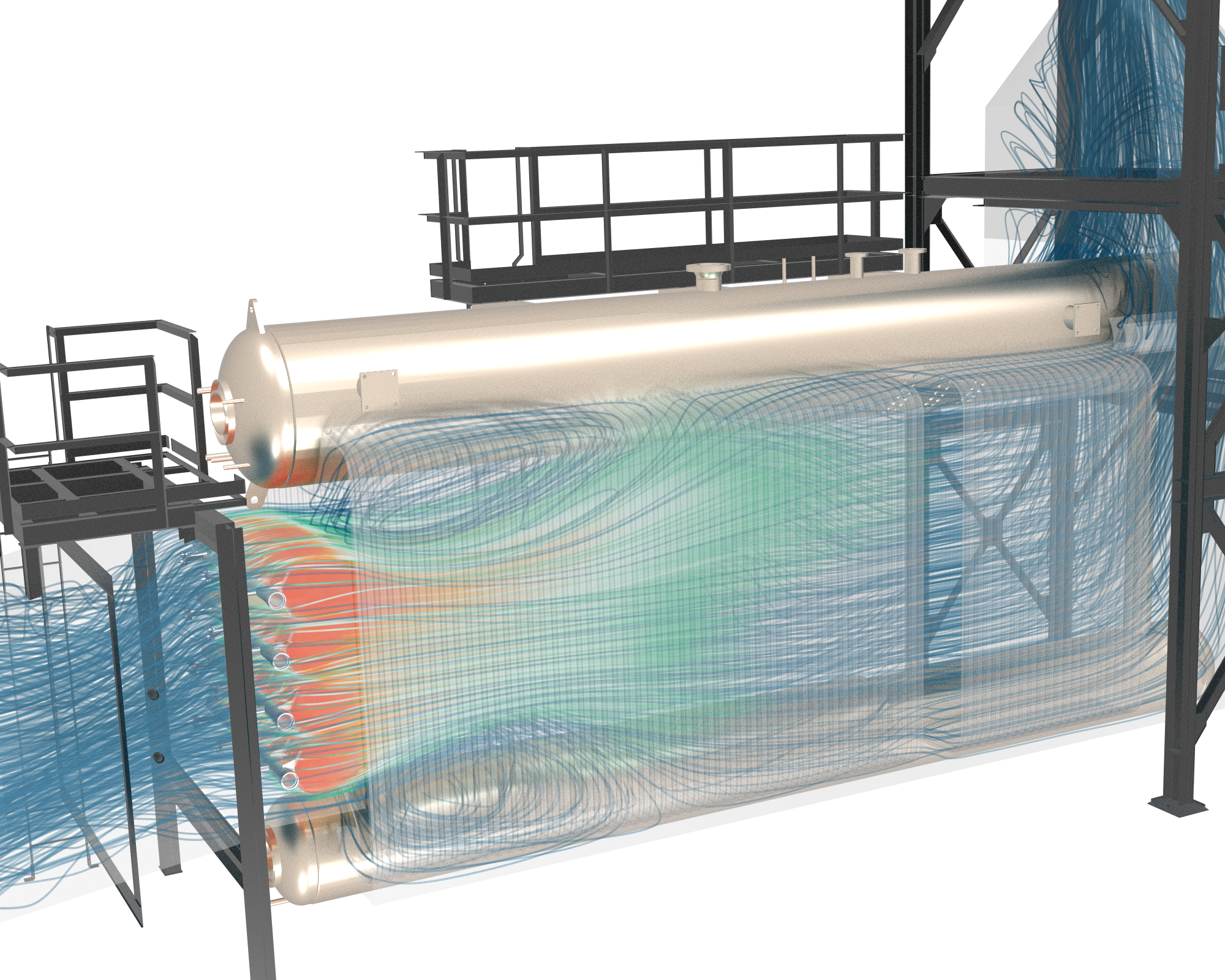
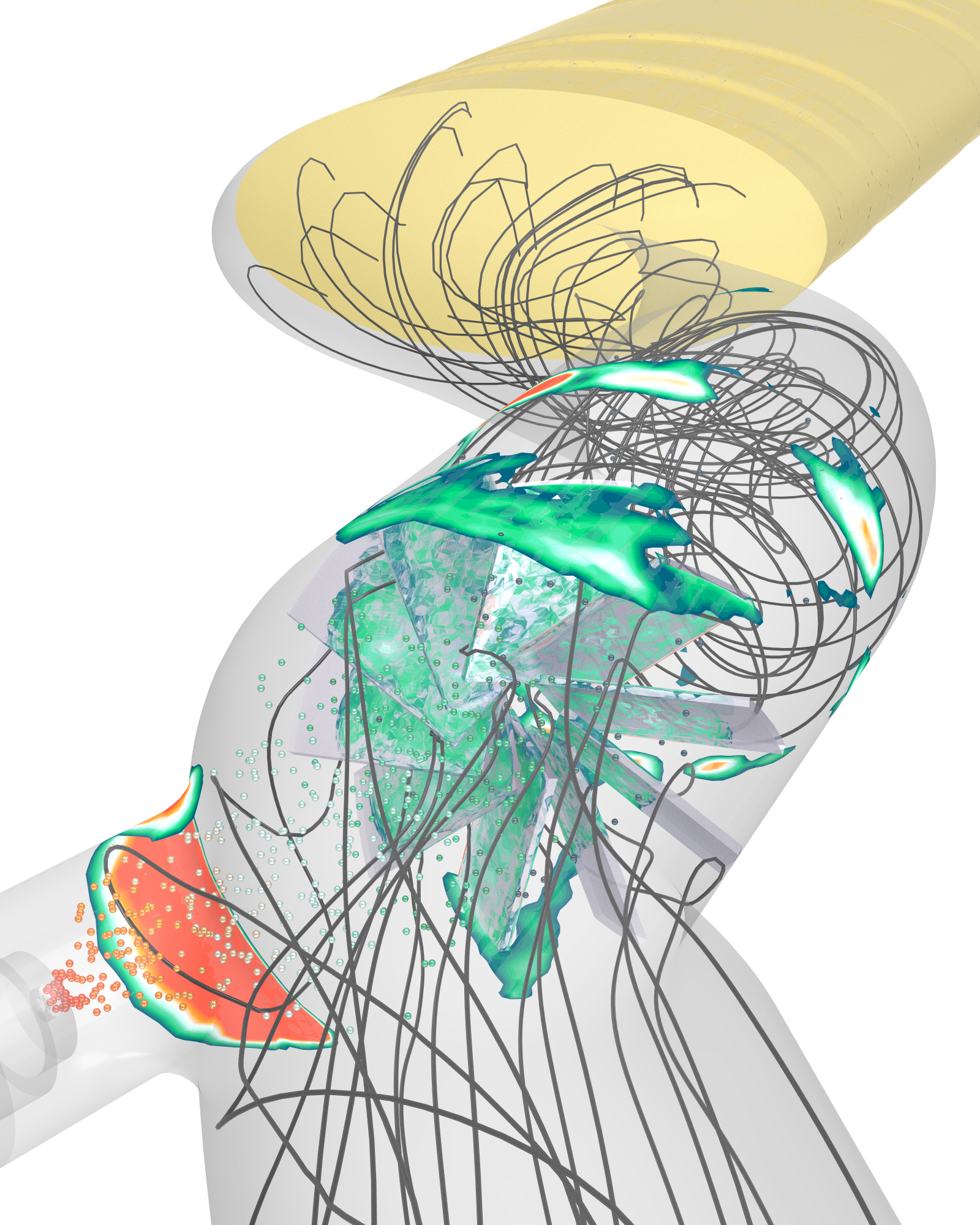
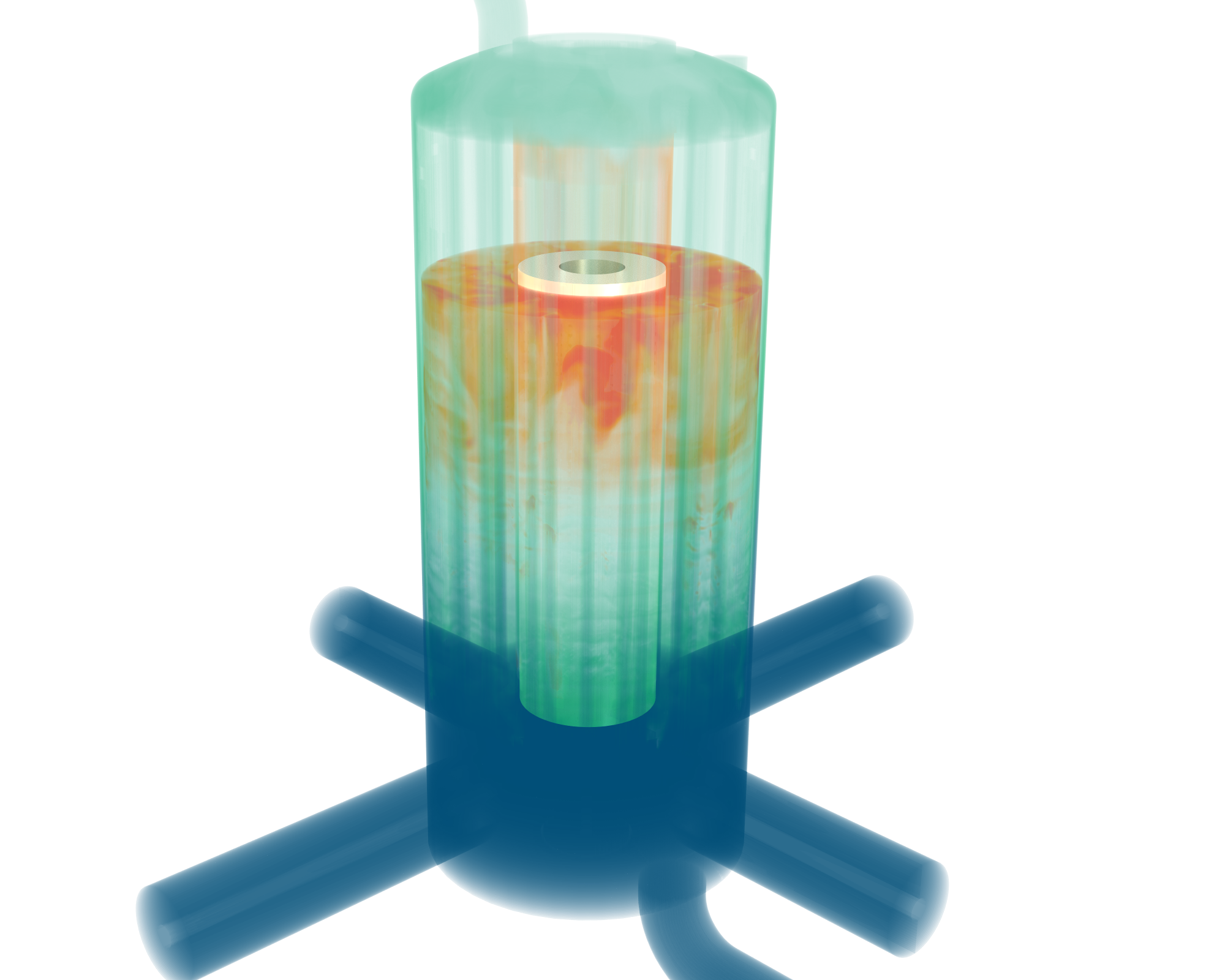
Chemically reacting systems often include complex geometries and physics, including multiple phases, conjugate heat transfer, radiation, and turbulence.
Because of this complexity a focus on speed without sacrificing fidelity is needed. Our software of choice, STAR-CCM+, excels in this respect through a comprehensive suite of reacting flow models and numerical methods, advanced meshing algorithms and automated workflows.
Specific methods that we’ve often used include complex chemistry models for accurate species predictions, flamelet models for fast and accurate flame-front predictions and chemical equilibrium models for the fastest predictions possible. Specialized models with which we have experience include those used for predicting emissions such as CO, NOx and soot and adaptive meshing for enhanced accuracy.
Our simulations are routinely fully coupled with conjugate heat transfer through surrounding solids, including the effects of radiation and external conditions.