F5 / FLUID-STRUCTURE INTERACTIONS
Recent trends in market requirements challenge our designs with respect to the durability and efficiency of fluid machinery. Frequent changes in operating conditions cause high demands on vibration behavior, operational stability and fatigue life.
Fluid Structure Interaction (FSI) is defined by the interaction of fluid dynamics and solid bodies. FSI is present in many applications, ranging from large-scale problems such as the dynamic instability of a fluttering aircraft wing to small-scale problems such as the flow of blood through an arterial valve.
With FSI simulations, engineers can visualize and optimize the behavior of complex products and predict performance and durability with confidence.
In FSI simulations, solid bodies can be rigid and act on the fluid unilaterally (one-way coupling) or can dynamically respond to an interacting fluid flow, either through responses in the rigid body’s motion or through the deformation of a non-rigid body.
FSI simulations are still quite costly so it is important to determine upfront whether one-way or two-way coupling is required to achieve the intended business objective or whether separate fluid and solid analyses will suffice. And if coupling is required, one must carefully assess the level of fidelity needed to address the quantities of interest and weight the computational costs accordingly. For example, non-linear material behavior will greatly increase the cost of simulations and may or may not be required.
These complexities underscore the importance of working with a qualified consulting engineer with many years of experience in FSI simulations.
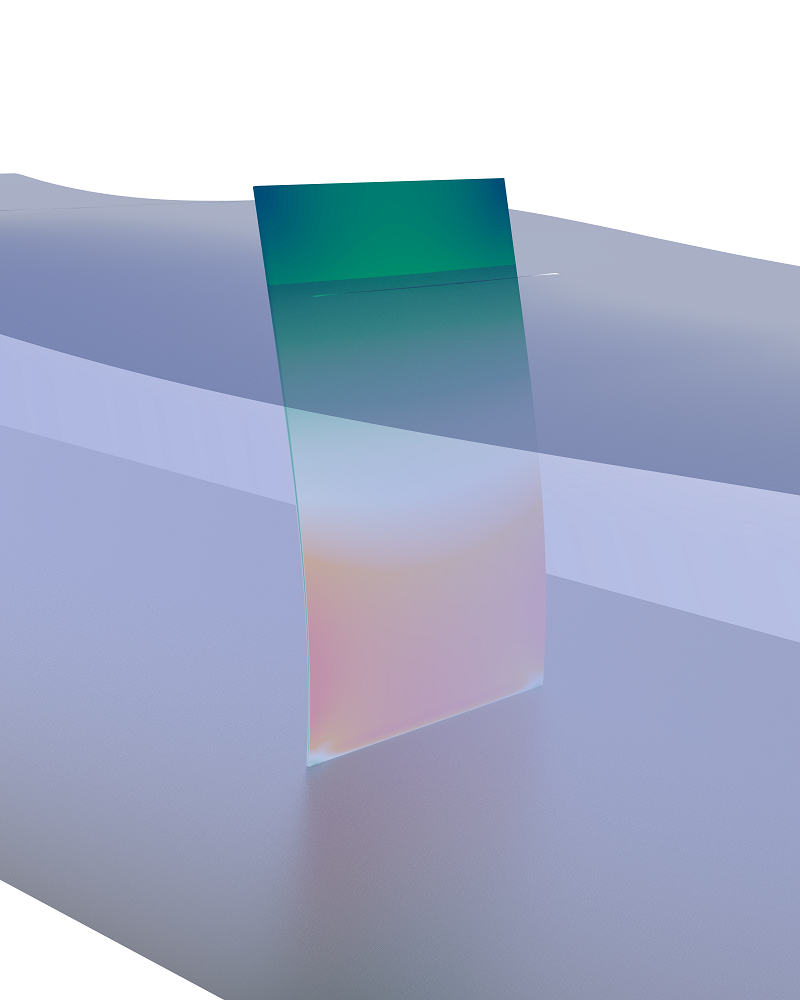
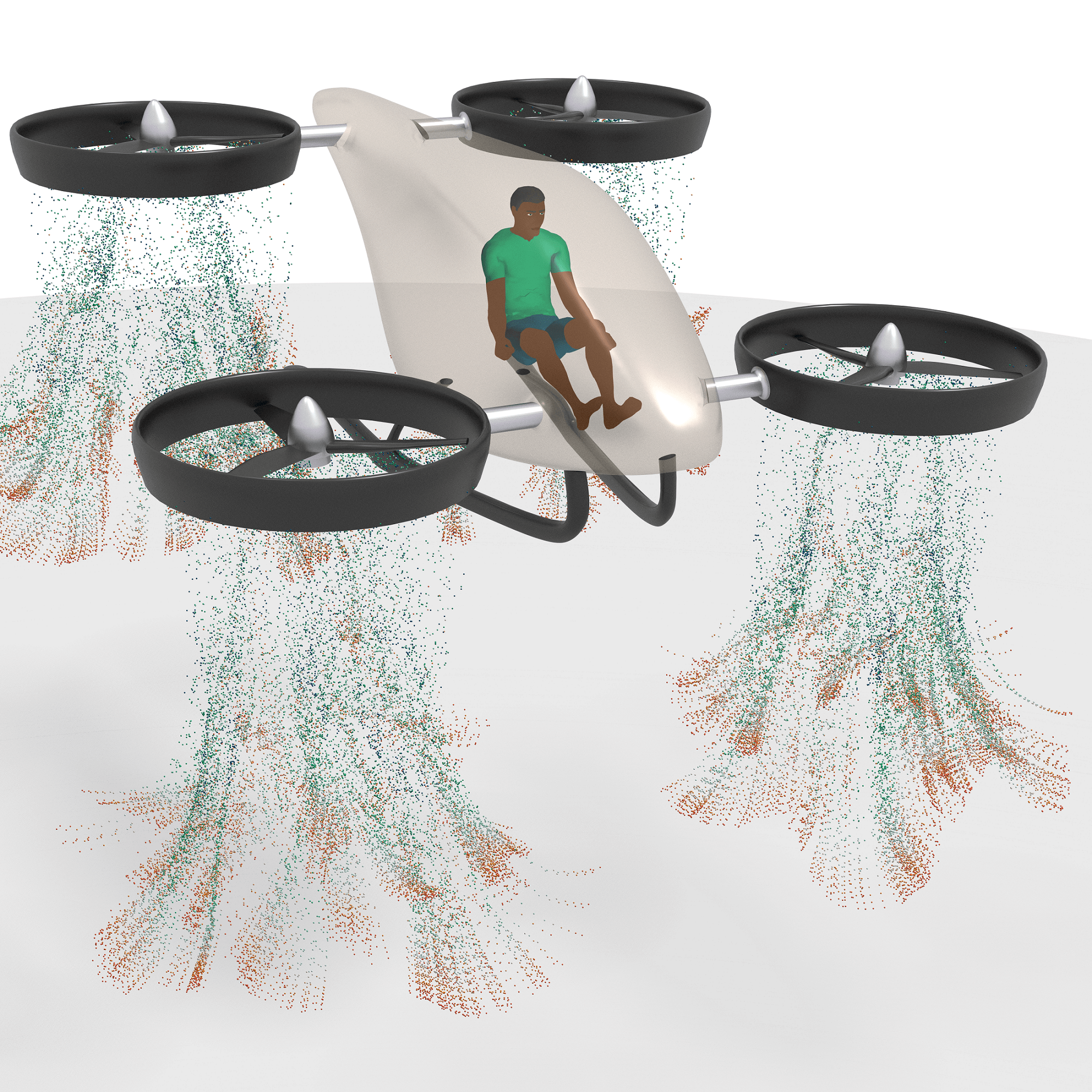
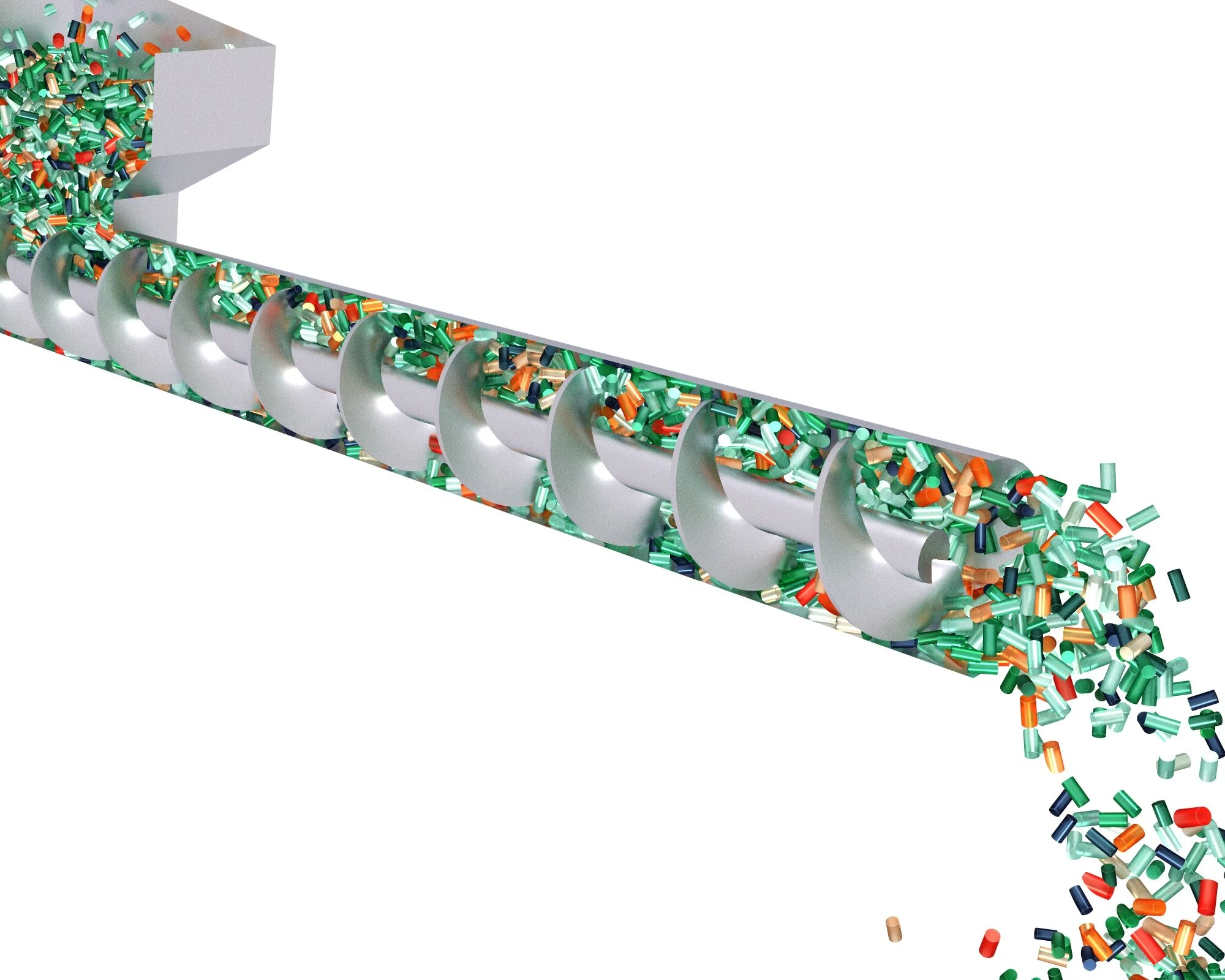
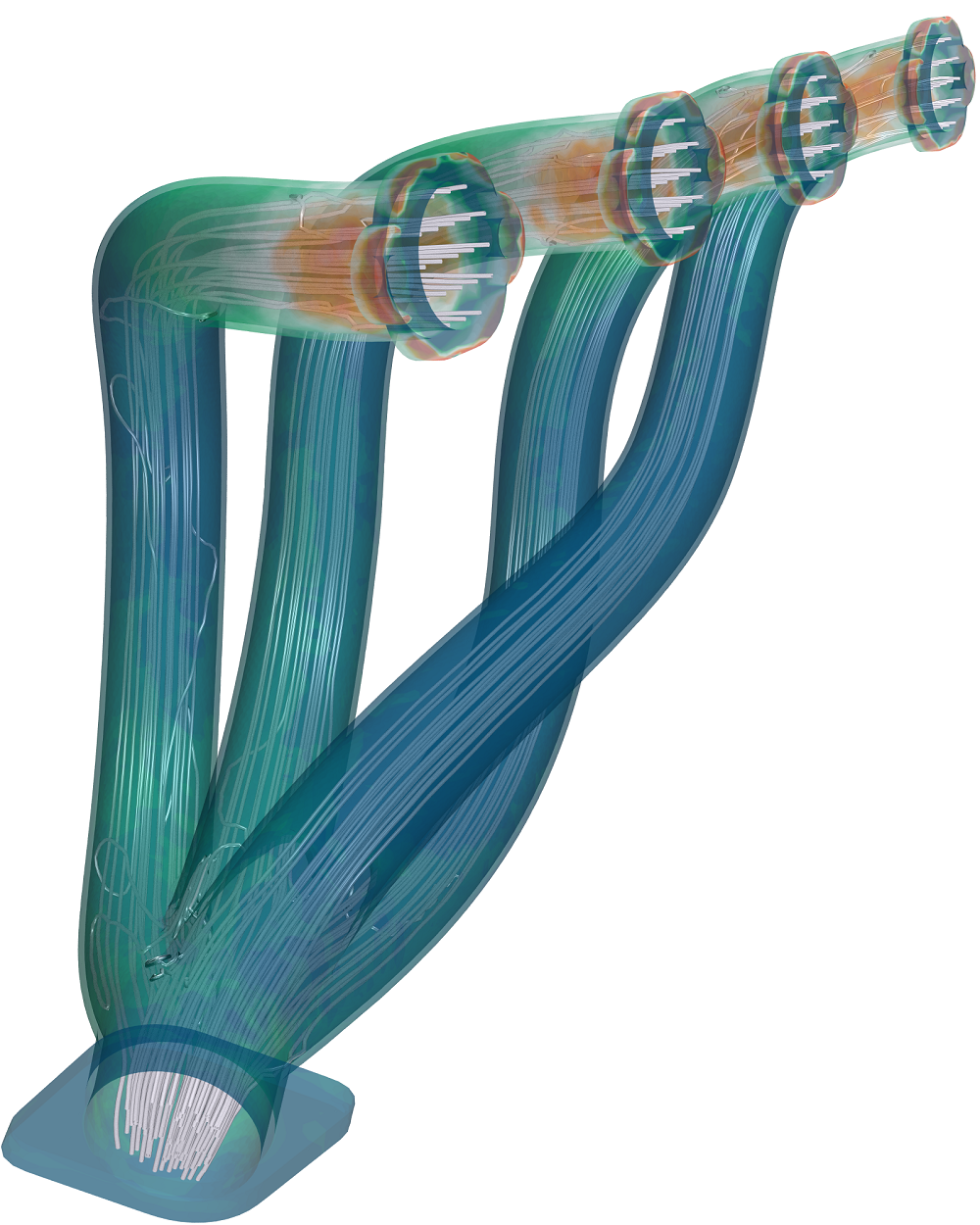
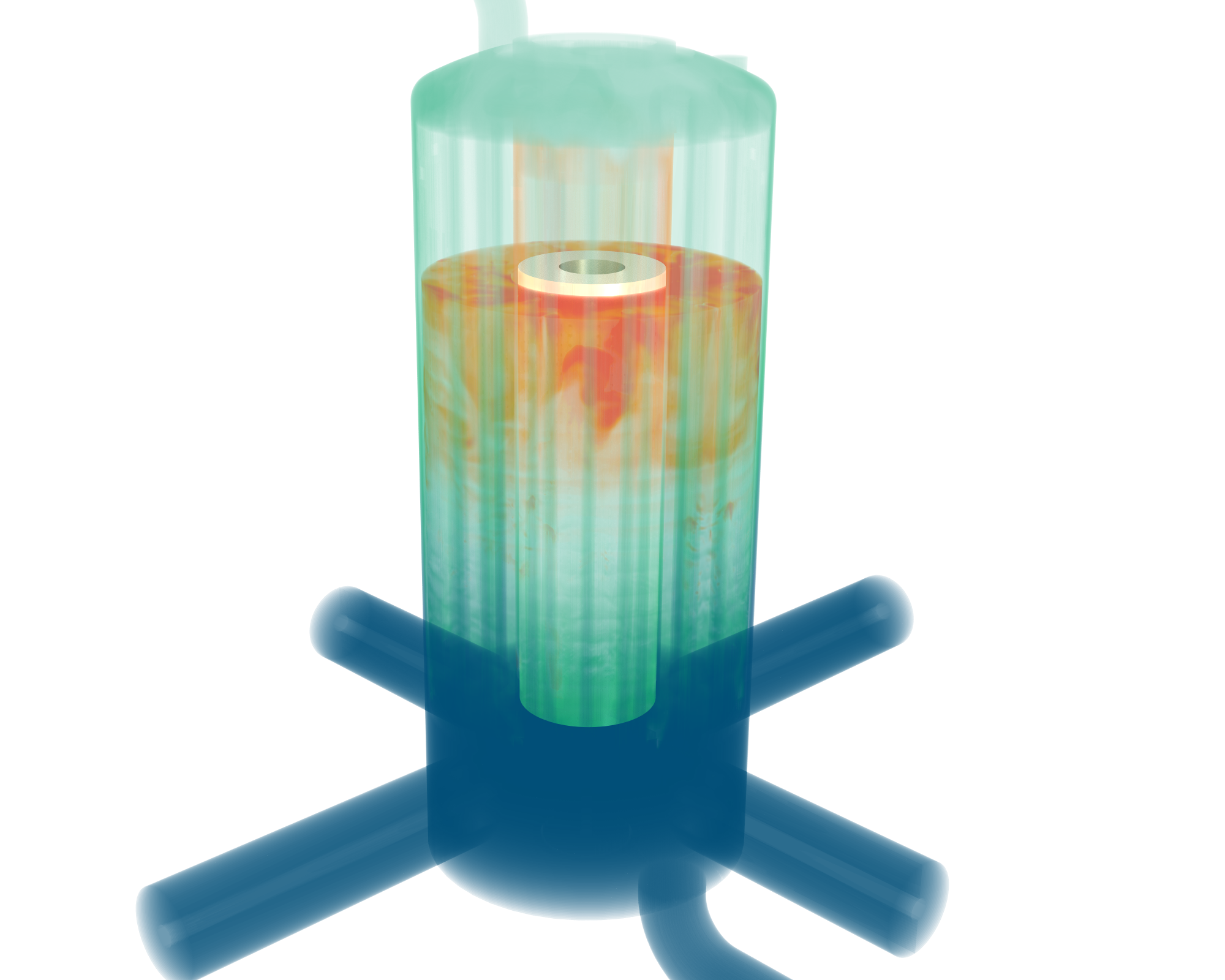
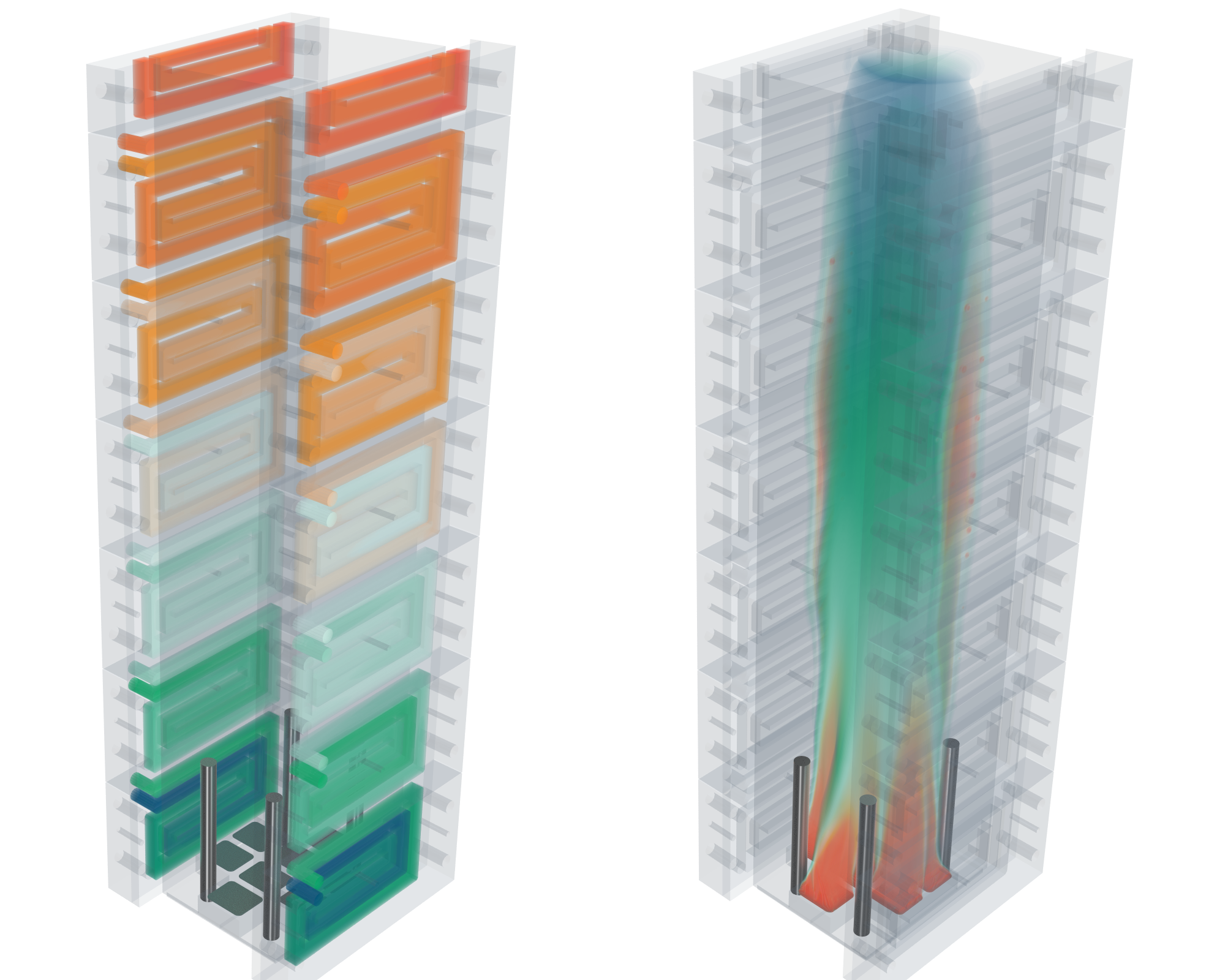
In one scenario, we use a DFBI (Dynamic Fluid Body Interaction) algorithm to simulate the motion of a rigid body in response to forces exerted by the fluid continuum, or to any additional forces that our customers help us define. Our simulations then calculate the resultant force and moment acting on the rigid body and solves the governing equations of motion to find the new position of the rigid body.
Many kinds of couplings can be defined that constrain the body’s motion relative to the environment or to other bodies, including spring-dampers, catenarys, contacts, and joints.
In a more challenging scenario, we use an integrated solid-stress solver to calculate the effect of the fluid forces on the structure displacements, but neglecting the effect of the structure displacements on the fluid flow. And finally in the most challenging scenario, we allow the structural displacements or rigid body motion to impact the fluid flow and all solvers are updated at each time step.
One of the most prevalent uses of FSI simulations is in marine transport. A marine vessel’s hull, its propulsion system and its rudder, all contribute to a hydrodynamic interaction with the environment. Reducing parasitic energy losses (hull drag and wave making drag) with these simulations by only a few percent can save thousands of gallons of fuel per year per vessel.
Establishing the dynamic position of the ship in relation to the sea surface (“sink and trim”) is critical to providing accurate resistance predictions under calm water design conditions. Therefore, at a minimum, simulations must incorporate both multiphase and DFBI methods.
Further, though, the majority of seakeeping analyses are also concerned with ship performance in uni-directional or long-crested waves. Our modeling capabilities extend across the entire range of known surface wave types including first- and fifth-order waves, cnoidal waves, and irregular waves and any superposition (combination) thereof.