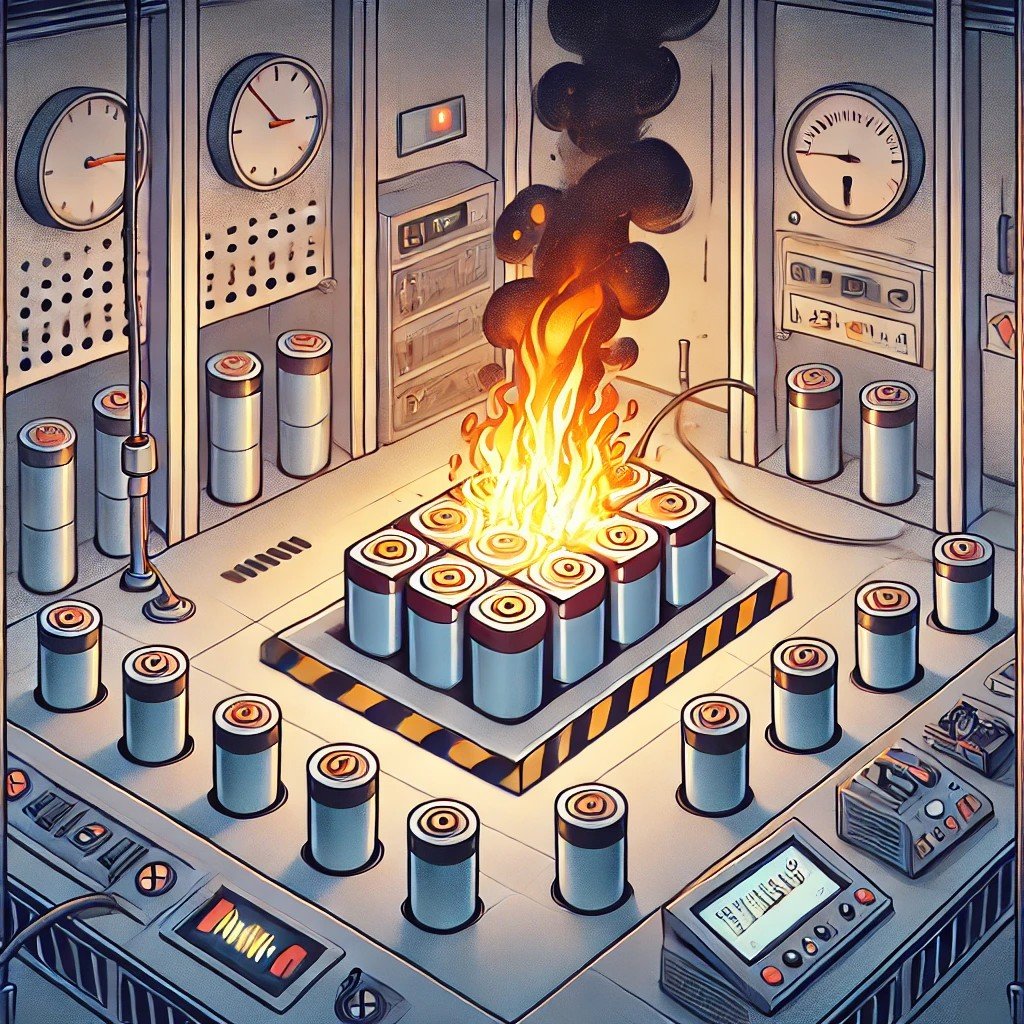
Thermal Runaway in Batteries: How CFD Helps Engineers Make Better Predictions
The Reality of Thermal Runaway in Lithium-Ion Batteries
If you work in battery engineering, you know that thermal runaway isn’t just a theoretical risk—it’s a real problem that keeps engineers up at night. Whether designing EV battery packs, aerospace power systems, or energy storage units, preventing uncontrolled heat propagation is critical.
But what actually happens inside the battery during thermal runaway? And more importantly, how can we predict and prevent it before it becomes a real-world disaster?
That’s where computational fluid dynamics (CFD) simulation comes in. With Simcenter STAR-CCM+, engineers can model battery chemistry, heat transfer, and gas generation—giving us a detailed look inside the runaway process without ever running a physical test.
Understanding Thermal Runaway: What Engineers Need to Know
How It Starts
Thermal runaway is a chain reaction triggered by excessive heat buildup inside a battery cell. It can be caused by:
Overcharging or deep discharging – Generates excess heat inside the electrolyte.
Mechanical damage – Cracks in the separator create internal short circuits.
Manufacturing defects – Tiny flaws can lead to localized overheating.
External heating – High ambient temperatures accelerate battery degradation.
How It Spreads
Once triggered, thermal energy spreads uncontrollably, leading to:
🔥 Electrolyte decomposition – Releases flammable gases.
🔥 Internal pressure buildup – Causes cell swelling and rupture.
🔥 Heat transfer to neighboring cells – Can trigger a domino effect in battery modules.
For EV manufacturers, aerospace engineers, and energy storage designers, these risks aren’t hypothetical—they’re critical safety concerns that must be modeled and mitigated.
Why CFD is the Key to Safer Battery Design
What We Can Simulate (That Physical Testing Can’t Easily Show)
Instead of relying solely on costly and time-consuming destructive testing, CFD simulations in Simcenter STAR-CCM+ allow engineers to:
Analyze heat generation and dissipation across cells, modules, and packs.
Predict gas buildup and pressure changes inside a failing battery.
Optimize cooling strategies to delay or prevent thermal propagation.
Compare different cell chemistries (LFP, NMC, etc.) for safer battery designs.
Why CFD is a Game-Changer for Thermal Runaway Analysis
✅ Captures the full physics of battery failure – Simulates electrochemistry, thermal behavior, and multiphase flow.
✅ Faster than physical testing – Identify risks before prototypes are built.
✅ More cost-effective – Reduces the need for destructive testing.
✅ Enables better designs – Helps optimize battery pack configurations for safer, more reliable products.
Industry-Specific Applications: Who Benefits from Thermal Runaway Simulations?
🚗 Electric Vehicles (EVs) & Hybrid Powertrains
Predict cell-to-cell thermal propagation to improve pack-level safety.
Ensure compliance with global safety standards (UNECE R100, UL 2580).
Evaluate fast-charging risks and develop thermal mitigation strategies.
✈ Aerospace & Aviation
Model battery performance at high altitudes (low pressure, extreme temperatures).
Improve safety in e-VTOL and drone power systems by preventing overheating.
⚡ Energy Storage Systems (ESS)
Simulate large-scale battery arrays for grid-level safety.
Optimize fire suppression systems to contain thermal events.
Final Thoughts: Better Battery Safety Starts with Better Simulation
Thermal runaway is one of the biggest safety challenges in battery engineering, and CFD simulation provides the insights needed to prevent catastrophic failures.
With Simcenter STAR-CCM+, engineers can:
✔ Analyze how heat spreads inside a battery pack.
✔ Test different cooling solutions virtually—without costly prototypes.
✔ Ensure compliance with global battery safety regulations.
If you’re designing EVs, aerospace power systems, or energy storage solutions, simulation-driven design isn’t optional—it’s essential.