HEAT EXCHANGER
Traditionally HE design has dependent on correlations and an iterative experimental approach aimed at meeting process flow condition targets. CFD simulations allow a more thorough design process and cost optimization.
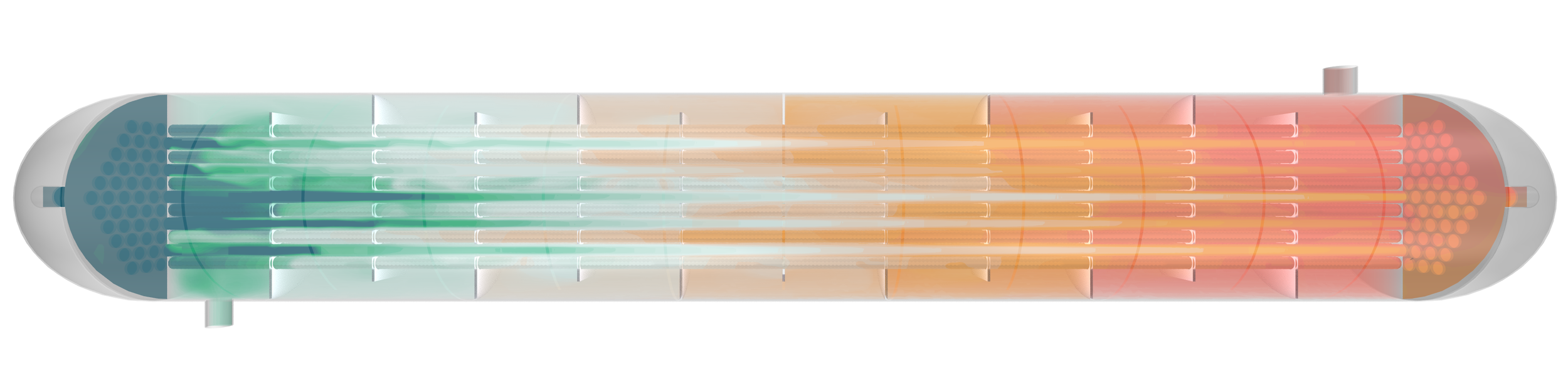
Heat exchangers are heat transfer devices used to transfer heat between hot and cold fluid and often intended to minimize primary energy consumption. Shell-and-tube heat exchangers (STHEs) in their various flavors are the most common type of heat exchanger across all process industries. STHEs are relatively easy to construct in a wide range of sizes and are mechanically rugged enough to withstand fabrication and installation stresses and normal operating conditions.
Heat transfer performance is driven by three factors; heat exchange surface area, the heat transfer coefficient and the logarithmic mean temperature difference between hot and cold fluids. Both surface area and the heat transfer coefficient are design driven and relating to fluid dynamic effects.
Many design parameters can be identified that impact heat exchanger cost and efficiency, including; the length and diameter of the shell, the number of baffles, the baffle geometry, the number of tubes, the spatial arrangement of tubes, the diameter of tubes, and material selections.
With recent advances in computing power, CFD simulations can now be utilized to cost-effectively evaluate heat exchanger designs with the aim to reduce construction or operating costs. Due to a number of advantages (e.g., low costs, easy design modifications in the investigated devices, fuller access to insights provided by results), this approach is becoming the preferred approach to heat exchanger design.
Multiphysics simulation results can include characterization of system pressure losses, heat exchange, and solid thermal stresses while cost evaluations are considered in parallel using Excel based cost models.
Optimize your heat exchanger designs in less time and at lower costs with Computational Fluid Dynamics.
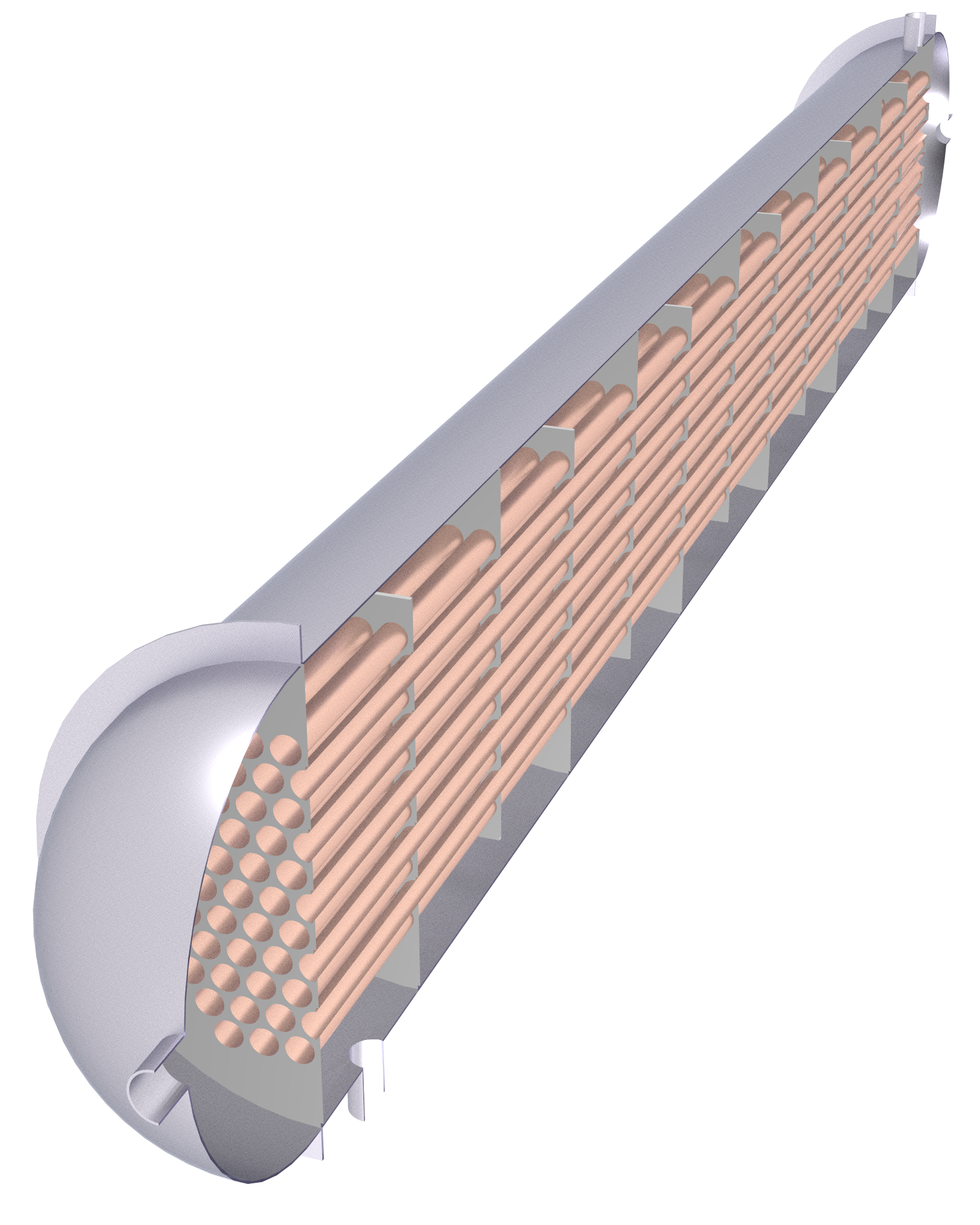
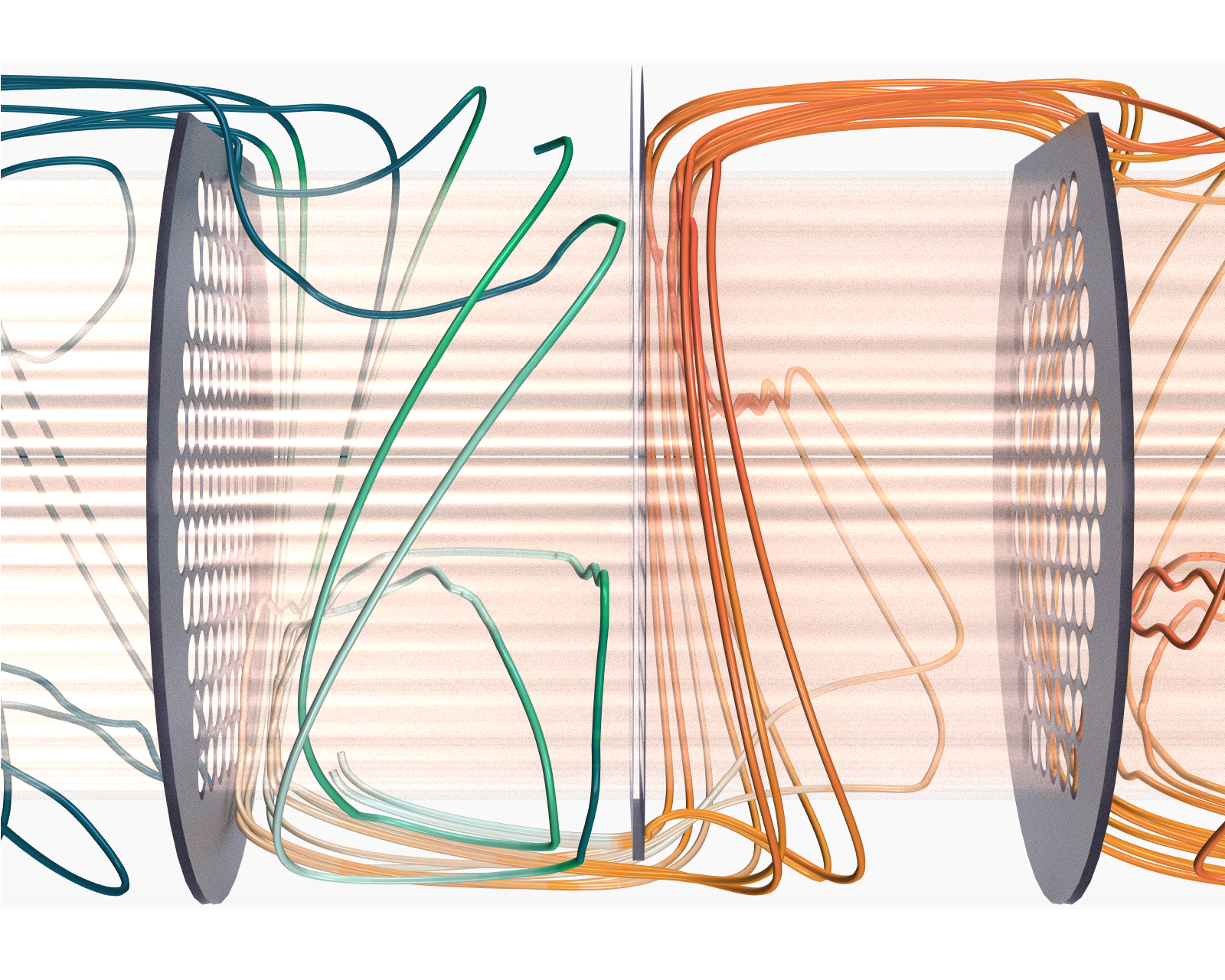
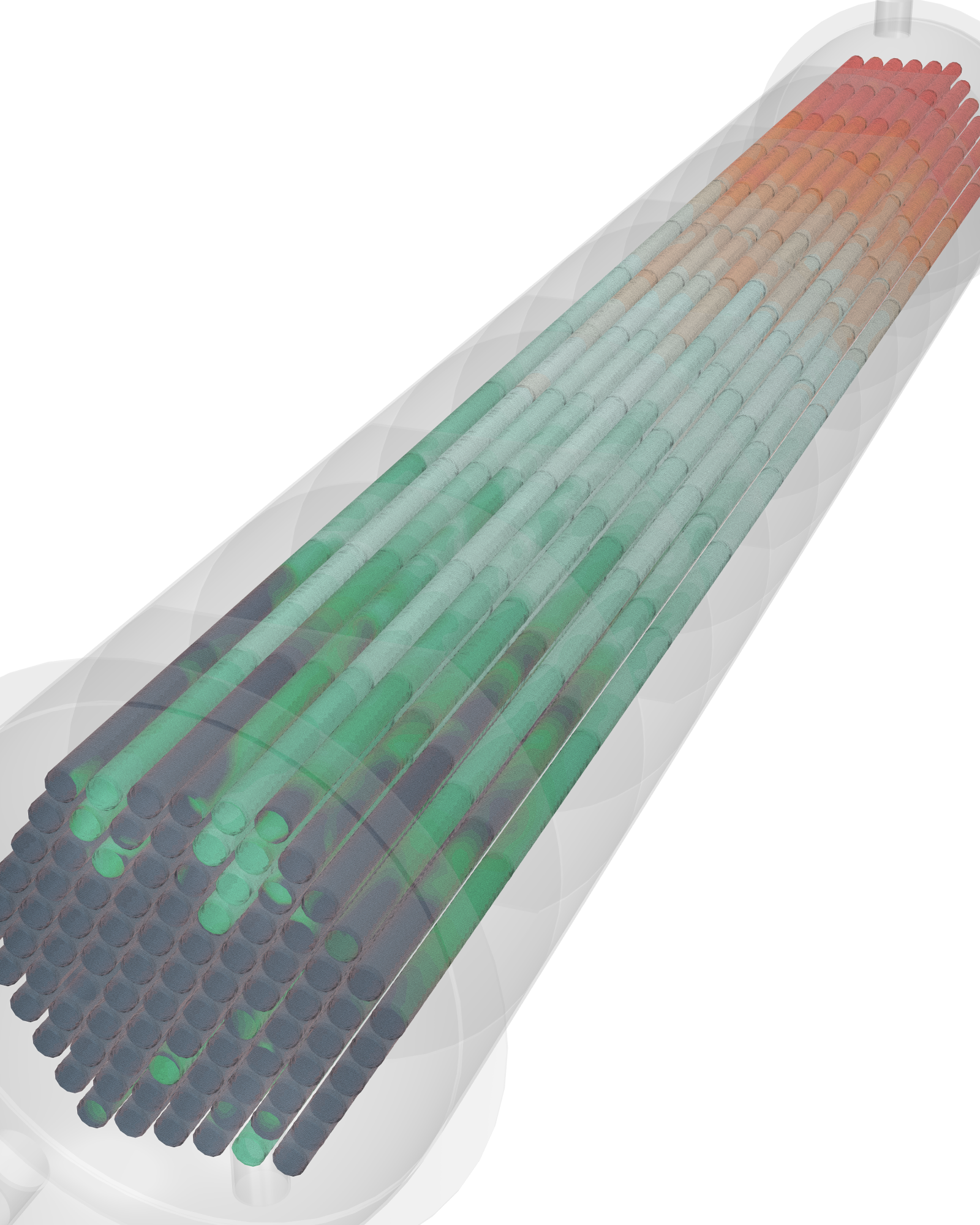
