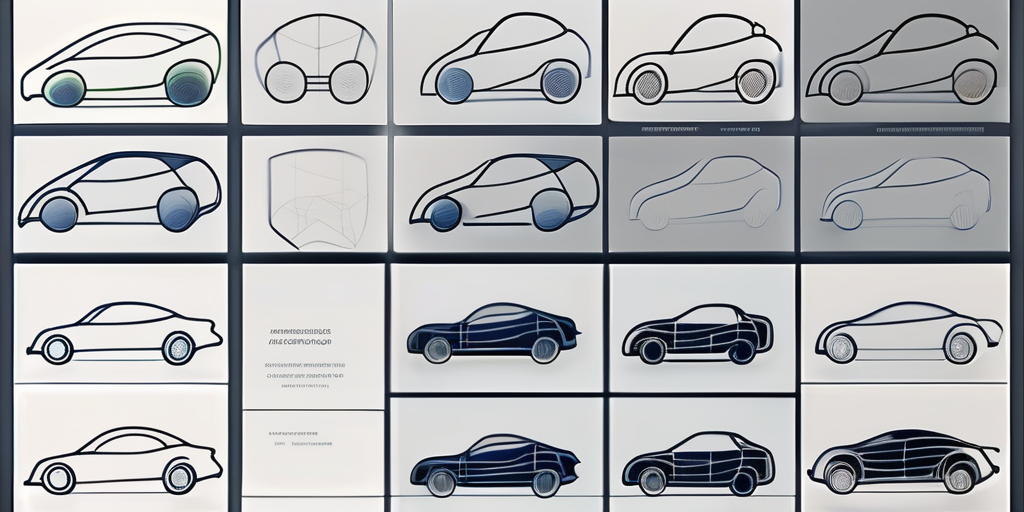
Faster, Cheaper, Better - The Pros of Leveraging Computational Fluid Dynamics
What are the Benefits of CFD Analysis
Computational Fluid Dynamics (CFD) Analysis is a powerful tool that allows engineers to simulate and analyze fluid flow and heat transfer in a virtual environment. This technology has revolutionized the way products are designed and optimized. In this article, we will explore the numerous benefits of CFD analysis and how it can significantly impact the engineering industry.
Shorter Design Cycle Timelines
One of the major advantages of CFD analysis is its ability to significantly reduce design cycle timelines. Traditionally, the design process involves building physical prototypes and conducting numerous experiments to gather crucial data. This iterative process can often take weeks or even months to complete.
However, with the advent of computational fluid dynamics (CFD) analysis, engineers now have a powerful tool at their disposal that can revolutionize the design process. CFD analysis allows engineers to simulate the behavior of fluids and gases in virtual environments, providing valuable insights into the performance of their designs.
By leveraging CFD analysis, engineers can iterate and optimize their designs much faster. They no longer have to rely solely on physical prototypes and time-consuming experiments. Instead, they can simulate different design configurations and test their performance virtually.
Imagine a scenario where a team of engineers is tasked with designing a new aircraft wing. Traditionally, they would have to build multiple physical prototypes, each with slight variations, and conduct extensive wind tunnel tests to evaluate their performance. This process alone could take several months.
However, with CFD analysis, the engineers can create a virtual model of the wing and simulate its behavior under various operating conditions. They can study the impact of design changes, such as altering the wing's shape or modifying the airfoil profile, and evaluate performance metrics such as lift, drag, and stability.
What's more, the results of the CFD analysis are available in a matter of hours or days, compared to the weeks or months required for physical testing. This allows engineers to make informed design decisions early in the development process, leading to efficient designs and shorter time to market.
Furthermore, CFD analysis enables engineers to explore a wider range of design possibilities. They can quickly evaluate the performance of different design configurations, allowing for more innovative and optimized solutions. This flexibility in design exploration can lead to breakthroughs and advancements that would have been difficult to achieve using traditional design methods.
In addition to reducing design cycle timelines, CFD analysis also offers cost savings. By minimizing the need for physical prototypes and experiments, engineers can save on materials, manufacturing, and testing expenses. This not only benefits the company's bottom line but also allows for more resources to be allocated towards further research and development.
In conclusion, CFD analysis has revolutionized the design process by significantly reducing cycle timelines. Engineers can now iterate and optimize their designs much faster, thanks to the ability to simulate different design configurations and test their performance virtually. This not only leads to efficient designs but also shorter time to market. With the cost savings and increased design exploration opportunities, CFD analysis has become an invaluable tool in the field of engineering.
Less Expensive Development
Another significant benefit of CFD analysis is cost savings in the development process. Traditional experimentation requires building physical prototypes, conducting tests, and often procuring specialized equipment. These activities can be resource-intensive and expensive.
By utilizing CFD analysis, engineers can reduce the need for physical prototypes and minimize the associated costs. Virtual simulations provide a cost-effective means to study different design iterations and evaluate their performance. Additionally, CFD analysis allows for the optimization of existing designs without the need for physical modifications, further reducing development costs.
Let's delve deeper into the cost savings achieved through CFD analysis. When engineers rely solely on physical prototypes, they must invest significant time and money in constructing these models. This process involves sourcing materials, assembling components, and ensuring that the prototype accurately represents the intended design. Moreover, conducting tests on physical prototypes often requires specialized equipment and facilities, which can be costly to acquire and maintain.
However, with CFD analysis, engineers can bypass these expenses. By creating virtual simulations, they can explore various design iterations without the need for physical prototypes. This not only saves time but also reduces the financial burden associated with building and testing multiple physical models. Engineers can quickly iterate through different designs, making adjustments and improvements virtually, before committing to physical production.
Furthermore, CFD analysis enables engineers to optimize existing designs without making any physical modifications. Through virtual simulations, they can identify areas of improvement and make adjustments to enhance performance. This eliminates the need for costly redesigns and physical alterations, resulting in substantial cost savings.
It's worth noting that the cost savings achieved through CFD analysis extend beyond the development phase. Once a design is finalized, engineers can use the virtual simulations to evaluate its performance under different operating conditions. This allows them to identify potential issues or areas for improvement before the product is manufactured and deployed. By catching and addressing these issues early on, companies can avoid costly recalls or product failures, saving both money and reputation.
In summary, CFD analysis offers significant cost savings in the development process. By reducing the reliance on physical prototypes and enabling virtual simulations, engineers can save time, money, and resources. The ability to optimize existing designs without physical modifications further enhances these cost savings. Additionally, CFD analysis helps identify potential issues early on, preventing costly recalls or product failures. Overall, incorporating CFD analysis into the development process is a wise investment that can lead to substantial financial benefits.
Ability to Adapt to Fast Changing Customer Requirements
The engineering industry operates in a dynamic environment where customer requirements and preferences can change rapidly. It is crucial for engineers to adapt and respond to these changes swiftly to stay competitive. CFD analysis provides the agility required to address fast-changing customer requirements.
CFD analysis, which stands for Computational Fluid Dynamics, is a powerful tool used by engineers to simulate and analyze fluid flow and heat transfer. It has revolutionized the way engineers design and optimize various systems, from aircraft and automobiles to buildings and industrial processes.
With CFD analysis, engineers can evaluate design variations and assess their impact on performance quickly. This enables them to identify the optimal design configurations that align with evolving customer needs. By leveraging the flexibility of virtual simulations, engineers can rapidly iterate and refine their designs to meet changing market demands, giving them a competitive edge.
One of the key advantages of CFD analysis is its ability to provide detailed insights into the behavior of fluid flow and heat transfer. Engineers can visualize and analyze complex flow patterns, turbulence, and temperature distributions within a system. This allows them to identify potential bottlenecks, areas of high stress, or regions with inadequate cooling, enabling them to make informed design decisions.
Furthermore, CFD analysis can also help engineers optimize the performance of existing systems. By simulating different operating conditions and design modifications, engineers can identify opportunities for improvement and fine-tune their designs accordingly. This not only enhances the overall performance of the system but also helps in reducing energy consumption, minimizing environmental impact, and increasing operational efficiency.
In addition to its technical benefits, CFD analysis also offers cost and time savings. Traditionally, physical prototypes and testing were required to evaluate design variations and performance. This process was not only time-consuming but also expensive. With CFD analysis, engineers can conduct virtual experiments, eliminating the need for costly prototypes and reducing the time required for testing. This accelerates the design iteration process and allows engineers to respond quickly to changing customer requirements.
In conclusion, CFD analysis provides engineers with the ability to adapt to fast-changing customer requirements in the dynamic engineering industry. By leveraging virtual simulations, engineers can evaluate design variations, optimize performance, and make informed design decisions. This not only gives them a competitive edge but also enables them to meet evolving customer needs effectively.
In Conclusion
CFD analysis offers significant benefits to the engineering industry. Its ability to shorten design cycle timelines, reduce development costs, and adapt to fast-changing customer requirements makes it an invaluable tool for engineers. By harnessing the power of CFD analysis, engineers can drive innovation, optimize designs, and bring products to market faster. As technology continues to advance, the role of CFD analysis will only become more crucial in shaping the future of engineering.