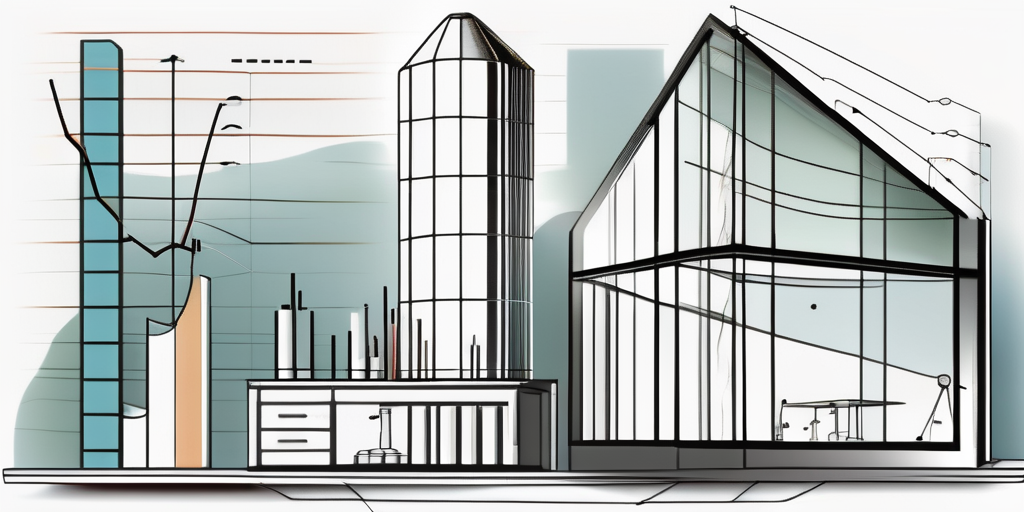
Exploring Options to Computational Fluid Dynamics (CFD)
What are the Alternatives to CFD Analysis?
Computational Fluid Dynamics (CFD) has become a powerful tool in engineering and scientific research for simulating fluid flow and heat transfer. However, there are situations where CFD analysis may not be the most suitable or feasible approach. In this article, we will explore some alternatives to CFD analysis that can be employed in such cases.
Classical Equations and Calculations
One of the oldest and most reliable methods for analyzing fluid flow is by using classical equations and calculations. These equations, such as the Navier-Stokes equations, provide a mathematical description of fluid flow based on fundamental physical principles. By solving these equations analytically or numerically, engineers can obtain valuable insights into fluid behavior without resorting to CFD analysis.
Classical equations and calculations have been extensively used in various fields of engineering, such as civil engineering for designing pipelines, hydraulic systems, and open channel flow, as well as in mechanical engineering for analyzing flow through pipes, ducts, and valves. Although these methods may not provide as detailed and realistic results as CFD analysis, they are often faster and more computationally efficient.
When it comes to analyzing fluid flow, classical equations and calculations offer a rich and diverse set of tools. For example, engineers can use the Bernoulli's equation to understand the relationship between fluid pressure, velocity, and elevation in a flowing system. This equation, derived from the conservation of energy principle, is particularly useful in analyzing flow through pipes and channels.
In addition to the Bernoulli's equation, engineers often rely on the continuity equation to study fluid flow. This equation, based on the principle of conservation of mass, allows engineers to determine how the flow rate changes along a pipe or channel. By solving the continuity equation, engineers can gain insights into the behavior of fluid flow, such as the formation of vortices or the occurrence of flow separation.
Another important tool in classical fluid flow analysis is the Reynolds number. This dimensionless quantity, named after Osborne Reynolds, provides a measure of the relative importance of inertial forces to viscous forces in a fluid flow. By calculating the Reynolds number, engineers can determine whether a flow is laminar or turbulent, which has significant implications for the design and performance of engineering systems.
Classical equations and calculations also play a crucial role in the design and analysis of hydraulic systems. Engineers use these methods to determine the pressure drop across pipes, the flow rate through valves, and the efficiency of pumps. By applying classical fluid flow principles, engineers can optimize the performance of hydraulic systems, ensuring efficient and reliable operation.
Furthermore, classical equations and calculations are not limited to steady-state flow conditions. Engineers have developed methods to analyze unsteady flows, such as water hammer in pipelines or the transient behavior of fluid flow in hydraulic systems. By incorporating time-dependent terms into the classical equations, engineers can predict and mitigate potential problems associated with unsteady flow conditions.
It is worth noting that while classical equations and calculations have been the backbone of fluid flow analysis for centuries, they are not without limitations. These methods often rely on simplifying assumptions, such as incompressible and Newtonian fluid behavior, which may not hold true in all engineering applications. Additionally, classical methods may struggle to accurately capture complex flow phenomena, such as turbulence or multiphase flow.
Despite these limitations, classical equations and calculations remain a valuable tool in the engineer's toolbox. They provide a solid foundation for understanding fluid flow behavior and can serve as a quick and reliable method for preliminary analysis. When combined with modern computational techniques, such as CFD analysis, classical methods can enhance the engineer's ability to design and optimize engineering systems for a wide range of applications.
Non-dimensional Analysis
Non-dimensional analysis, also known as similarity analysis, is a powerful technique that allows engineers to study the behavior of complex fluid flow systems without the need for detailed modeling or simulation. By identifying and manipulating dimensionless parameters, such as Reynolds number, Froude number, or Mach number, engineers can derive important relationships and scaling laws that govern fluid flow.
This approach is particularly useful in situations where the geometry and boundary conditions of the problem are well-defined and can be simplified. Non-dimensional analysis can provide valuable insights into the behavior of fluid flow, such as the onset of turbulence, flow separation, or the performance of various fluid devices like pumps, turbines, and heat exchangers.
Let's delve deeper into the concept of non-dimensional analysis and its applications. One of the key advantages of non-dimensional analysis is its ability to provide engineers with a universal framework for understanding fluid flow phenomena. By expressing physical quantities in terms of dimensionless numbers, engineers can compare and analyze different flow systems, regardless of their size or specific properties.
For example, the Reynolds number, which represents the ratio of inertial forces to viscous forces in a fluid flow, plays a crucial role in determining the flow regime. By examining the Reynolds number, engineers can predict whether a flow will be laminar or turbulent. This information is vital for designing efficient and reliable fluid systems, as turbulent flows often result in increased energy losses and decreased performance.
Another dimensionless parameter commonly used in non-dimensional analysis is the Froude number. It relates the inertial forces to gravitational forces and is particularly relevant in open channel flow and free surface flow problems. By analyzing the Froude number, engineers can determine the critical flow conditions, such as when a flow transitions from subcritical to supercritical, or when hydraulic jumps occur.
The Mach number, on the other hand, is a dimensionless parameter that characterizes the compressibility effects in fluid flow, especially in high-speed flows. It is widely used in aerospace engineering to study the behavior of supersonic or hypersonic flows. By examining the Mach number, engineers can assess the impact of compressibility on the flow properties, such as shock waves, expansion waves, and changes in density and temperature.
Non-dimensional analysis is not limited to these parameters alone. Engineers often employ a wide range of dimensionless numbers, depending on the specific problem at hand. Some other commonly used dimensionless parameters include the Cavitation number, Strouhal number, Weber number, and Peclet number, among many others.
Overall, non-dimensional analysis is a versatile tool that allows engineers to gain valuable insights into fluid flow behavior. It enables them to make informed decisions, optimize designs, and predict system performance without the need for extensive experimentation or complex simulations. By understanding the underlying principles of non-dimensional analysis, engineers can unlock the potential to solve a wide range of fluid flow problems and contribute to advancements in various industries.
Physical (Experimental) Scale Modeling
Physical scale modeling involves the construction of a physical model that represents the real-life system or flow situation. This model is then subjected to tests and experiments in a controlled environment, such as a laboratory or a testing facility. By carefully measuring and analyzing the behavior of the physical model, engineers can gain valuable insights into the fluid flow phenomena that occur in the actual system.
Wind Tunnel Testing Underway at NASA Langley and Ames Research Laboratories
This approach is particularly useful when dealing with complex flow phenomena, such as multiphase flow, flow around complex geometries, or flow in highly turbulent or unsteady conditions. The advantage of physical scale modeling is that it can capture complex flow phenomena that are difficult to simulate accurately using CFD. However, it is worth noting that physical scale modeling can be time-consuming, expensive, and may have limitations in terms of scale and accuracy.
In order to use a model to simulate the conditions of the prototype, the model must be geometrically, kinematically, and dynamically similar to the prototype system. To obtain full similarity between the two flow problems, all independent force ratios that can be written must be the same in both the model and the prototype. Thus, dynamic similarity is ensured by the five simultaneous equations below, where the subscripts p and m stand for prototype and model respectively. The Reynolds and Froude numbers defined previously are obvious. The latter two equations define the Cavitation number and Weber number.
Build and Test Prototyping
Build and test prototyping involves the construction of a physical prototype or model of the system or device under investigation. This prototype is then tested and evaluated in a real-world environment to assess its performance and behavior. By iterating the design and testing process, engineers can refine and optimize the prototype until it meets the required specifications.
Four-Rotor UAV Prototype Testing at NASA’s Ames Research Center.
This approach is particularly useful for evaluating the performance of fluid devices, such as pumps, compressors, or turbines, as well as for testing the effectiveness of flow control strategies or design modifications. Build and test prototyping offers a hands-on and practical approach to understanding fluid flow and can provide valuable insights that complement the results obtained from CFD analysis or other theoretical methods.
Conclusions
In conclusion, while CFD analysis is a powerful tool for simulating fluid flow and heat transfer, it is essential to consider alternative approaches when it may not be the most suitable option. Classical equations and calculations, non-dimensional analysis, physical scale modeling, and build and test prototyping are all viable alternatives that can provide valuable insights into fluid flow phenomena. By leveraging these alternatives, engineers can make informed decisions and optimize designs in a cost-effective and efficient manner.