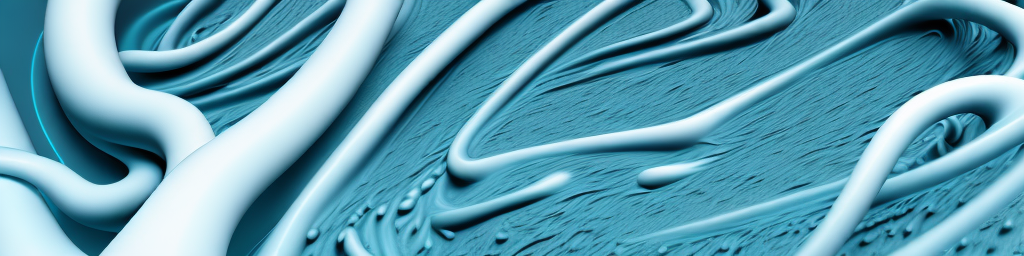
Intro to Chemically Reacting Flow Models
Chemically Reacting Flow Models in CFD
Chemical reactions are an essential part of many industrial processes, and their accurate prediction is crucial for optimizing these processes. Computational fluid dynamics (CFD) has emerged as a powerful tool for simulating chemical reactions in complex flows, providing a way to predict and optimize process outcomes. In this article, we will explore the use of chemically reacting flow models in CFD, the types of reactions that can be modeled, different modeling approaches, as well as challenges and applications in industry.
Chemical reactions are fascinating phenomena that occur all around us, from the rusting of iron to the combustion of gasoline in an engine. However, what many people don't realize is that these reactions are always happening within a fluid environment. Whether it's the air we breathe or the water we drink, fluids play a crucial role in the behavior of chemical reactions.
One of the most critical factors in the reaction rate and product formation is the flow of the fluid. For example, if a gas is flowing rapidly through a pipe, the chemical reaction occurring within that pipe will be affected by the speed and direction of the gas flow. Similarly, if a liquid is flowing over a surface, the chemical reaction occurring on that surface will be influenced by the speed and turbulence of the liquid flow.To accurately model these chemical reactions, it is essential to understand the underlying fluid dynamics. This involves studying the movement and behavior of fluids, including how they flow, mix, and interact with their surroundings. By incorporating fluid dynamics into our models of chemical reactions, we can gain a deeper understanding of how these reactions occur and how we can optimize them for various applications.For example, in the field of combustion, understanding the fluid dynamics of the gases flowing through an engine can help us design more efficient and environmentally friendly engines.
Similarly, in the field of chemical engineering, understanding the fluid dynamics of liquids flowing through pipes and reactors can help us optimize chemical production processes and reduce waste.In conclusion, while chemical reactions may seem like purely chemical phenomena, they are, in fact, intimately tied to the behavior of fluids. By incorporating fluid dynamics into our models of chemical reactions, we can gain a deeper understanding of these fascinating phenomena and use that knowledge to improve our world.
What Types of Chemical Reactions can be Modeled in CFD?
Computational Fluid Dynamics (CFD) is a powerful tool that can be used to simulate and study a wide range of chemical reactions. CFD is a branch of fluid mechanics that uses numerical methods and algorithms to solve and analyze problems that involve fluid flows. It has been widely used in many fields, including aerospace, automotive, and chemical engineering.
One of the most important applications of CFD is in the modeling of chemical reactions. CFD can model a wide range of chemical reactions, including combustion, pyrolysis, gasification, and more. The key requirement is that the reaction takes place in a fluid environment. This means that CFD can be used to study reactions that occur in gases, liquids, and even in some cases, solids.
The complexity of the reaction that can be modeled using CFD can vary greatly. It can range from simple single-step reactions to complex multi-step reactions involving dozens of species and intermediate products. For example, CFD can be used to model the combustion of a single fuel molecule, such as methane, which involves a single-step reaction. On the other hand, CFD can also be used to model the combustion of a complex fuel mixture, such as gasoline, which involves a complex multi-step reaction.
CFD can also be used to study the effects of various factors on chemical reactions. For example, CFD can be used to study the effect of temperature, pressure, and flow rate on a chemical reaction. This information can be used to optimize the design of reactors and other chemical processes.
In addition to the modeling of chemical reactions, CFD can also be used to study other aspects of chemical processes. For example, CFD can be used to study the mixing of fluids, the transport of heat and mass, and the formation of pollutants. This makes CFD a very versatile tool that can be used to study many different aspects of chemical processes.
In conclusion, CFD is a powerful tool that can be used to model a wide range of chemical reactions. It can be used to study simple single-step reactions or complex multi-step reactions involving dozens of species and intermediate products. CFD can also be used to study the effects of various factors on chemical reactions and other aspects of chemical processes. Its versatility makes it a valuable tool for chemical engineers and researchers.
Comparing Different Chemically Reacting Flow Models
Several modeling approaches are available to simulate chemically reacting flows in CFD. Two of the most widely used models are the laminar flamelet and the eddy dissipation concept (EDC). The laminar flamelet model explicitly solves for the flame structure, and its robustness has made it popular in practical applications. On the other hand, the EDC model uses a statistical turbulence closure to model the effects of turbulence on reaction rates. Comparing these models' strengths and weaknesses is essential to determine which one is best suited for a particular application.
The laminar flamelet model is based on the assumption that the flame structure can be represented by a set of steady-state solutions. This model is well-suited for low-turbulence, laminar flames, where the flame structure is well-defined. However, it may not be accurate for high-turbulence, non-laminar flames, where the flame structure is more complex and variable. In these cases, the EDC model may be more appropriate.
The EDC model uses a statistical approach to model the effects of turbulence on reaction rates. This model assumes that the turbulence scales are much smaller than the flame thickness, allowing the turbulence to be modeled separately from the flame structure. The EDC model has been shown to be effective in simulating high-turbulence, non-laminar flames, where the flame structure is more complex and variable. However, it may not be as accurate for low-turbulence, laminar flames, where the flame structure is well-defined.
Another model that is commonly used for simulating chemically reacting flows is the flamelet generated manifolds (FGM) model. This model combines the strengths of the laminar flamelet and EDC models by using a set of steady-state solutions to represent the flame structure and a statistical approach to model the effects of turbulence on reaction rates. The FGM model has been shown to be effective in simulating both low-turbulence, laminar flames and high-turbulence, non-laminar flames.
In conclusion, the choice of which model to use for simulating chemically reacting flows depends on the specific application and the characteristics of the flame being modeled. The laminar flamelet model is well-suited for low-turbulence, laminar flames, while the EDC model is better suited for high-turbulence, non-laminar flames. The FGM model combines the strengths of both models and can be used for both types of flames.
Investigating the Role of Turbulence in Chemically Reacting Flow Models
The effect of turbulence on reaction rates is a crucial factor in chemically reacting flows, and accurately modeling this interaction is vital for a wide range of applications. Turbulent transport of chemical species can cause local fluctuations in the reactant concentrations, leading to a non-uniform reaction rate across the flame front. This non-uniformity can have a significant impact on the efficiency and stability of combustion systems, as well as the formation of pollutants.
One approach to improving the accuracy of chemically reacting flow models is to incorporate advanced turbulence models that can capture the complex interactions between turbulence and chemistry. These models use a variety of techniques, such as large eddy simulation and Reynolds-averaged Navier-Stokes equations, to simulate the behavior of turbulent flows.
Another important factor to consider is the effect of turbulence on the transport of heat and mass within the reacting flow. Turbulent mixing can enhance the transport of heat and mass, leading to a more efficient combustion process. However, it can also lead to the formation of hotspots and cool spots, which can have a significant impact on the reaction rate.
Recent studies have also investigated the role of turbulence in the formation of pollutants, such as nitrogen oxides (NOx) and soot. Turbulent mixing can lead to the formation of these pollutants, which can have a significant impact on air quality and human health. Understanding the mechanisms behind their formation is crucial for developing effective strategies to reduce their emissions.
In conclusion, the role of turbulence in chemically reacting flow models is a complex and challenging area of research. However, by incorporating advanced turbulence models and considering the impact of turbulence on heat and mass transport, as well as pollutant formation, researchers are making significant progress towards improving the accuracy and efficiency of combustion systems.
Investigating the Effect of Computing Power on Chemically Reacting Flow Models
The accurate simulation of chemically reacting flows is crucial for a wide range of applications, including combustion engines, chemical processing, and environmental studies. These simulations require significant computational resources due to the complex nature of the chemical reactions involved.
One of the most significant factors affecting the accuracy and efficiency of chemically reacting flow models is the available computing power. With the rapid advancement of technology, computing power has increased significantly over the past few decades. This increase in computing power has allowed for more complex and detailed simulations, leading to more accurate predictions of chemical reactions' behavior.
One approach to modeling chemically reacting flows is the use of computational fluid dynamics (CFD) simulations. CFD simulations use numerical methods to solve the governing equations of fluid flow, heat transfer, and chemical reactions. These simulations require a significant amount of computing power to accurately model the complex interactions between the fluid flow and chemical reactions.
As computing power continues to increase, CFD simulations can be run at higher resolutions and with more detailed models, leading to more accurate predictions of chemical reactions' behavior. Additionally, the increased computing power allows for the optimization of the modeling approach, enabling researchers to identify the most efficient and accurate method for simulating specific chemical reactions.
However, the increase in computing power also presents new challenges. As simulations become more complex and detailed, the amount of data generated increases significantly, requiring more storage and processing power. Additionally, the cost of computing resources can be a limiting factor, particularly for smaller research groups or organizations with limited budgets.
Despite these challenges, the continued increase in computing power has allowed for significant advancements in the modeling and simulation of chemically reacting flows. These advancements have led to a better understanding of the behavior of chemical reactions and have enabled researchers to develop more efficient and sustainable chemical processes.
Exploring the Benefits of Using Chemically Reacting Flow Models
The use of chemically reacting flow models in computational fluid dynamics (CFD) has revolutionized the way we design and optimize industrial processes. These models simulate the complex interactions between chemical reactions, fluid flow, and heat transfer, providing insights into the behavior of products and processes that were previously impossible to obtain.
One of the key benefits of using chemically reacting flow models is the ability to predict the optimal operating conditions for a given process. By simulating different scenarios, researchers and engineers can identify the most efficient and cost-effective conditions for their process. This not only improves productivity but also reduces energy consumption and waste production.
Another advantage of using these models is the ability to understand the behavior of products. By simulating the chemical reactions and fluid flow within a process, researchers can predict the composition, properties, and quality of the final product. This information is crucial for ensuring that the product meets the desired specifications and is safe for consumers.
Furthermore, chemically reacting flow models can help identify potential improvements in the design of process equipment. By simulating different designs and configurations, researchers can optimize the geometry, size, and materials used in the equipment. This can lead to significant improvements in efficiency, safety, and cost-effectiveness.
Chemically reacting flow models enable engineers to optimize designs without the need for expensive and time-consuming experiments. By simulating the process, engineers can quickly identify potential areas for improvement and make adjustments to the design accordingly. This not only saves time and money but also reduces the environmental impact of the process by minimizing the need for physical experimentation.
Another benefit of using these models is that they enable engineers to explore a wider range of design options. By simulating the process, engineers can quickly test different design options and identify the optimal solution. This is particularly useful in industries where the process conditions are complex and difficult to replicate in a physical experiment.
Overall, the use of chemically reacting flow models in CFD has transformed the way we approach industrial processes. By providing detailed insights into the behavior of products and processes, these models enable researchers and engineers to optimize their designs, increase efficiency, and reduce environmental impact. As such, they are an essential tool for anyone involved in the design and optimization of industrial processes.
Examining the Challenges of Modeling Chemical Reactions in CFD
Computational fluid dynamics (CFD) has revolutionized the way we understand fluid mechanics and thermodynamics. However, accurately modeling chemical reactions in CFD is not without its challenges.
One of the biggest challenges in modeling chemical reactions in CFD is accurately modeling the turbulence-chemistry interaction. Turbulence plays a crucial role in chemical reactions, as it enhances mixing and increases the reaction rates. However, turbulence also leads to fluctuations in temperature, pressure, and species concentrations, which can impact the reaction kinetics. Therefore, accurately modeling the turbulence-chemistry interaction is essential for predicting the behavior of chemical reactions in CFD simulations.
Another challenge in modeling chemical reactions in CFD is properly accounting for the transport of different species. Chemical reactions involve the transport of multiple species, each with its own unique properties. These species can have different diffusion coefficients, thermal conductivities, and specific heats, which can impact the reaction kinetics. Therefore, it is important to accurately model the transport of each species in the CFD simulation.
Furthermore, accounting for the radiation effects on the flame front is another challenge in modeling chemical reactions in CFD. Radiation can impact the temperature field and alter the reaction rates, leading to inaccurate predictions. Therefore, accurate modeling of radiation is essential for predicting the behavior of chemical reactions in CFD simulations.
Despite these challenges, improvements in computing power and numerical algorithms continue to make these models more accurate and practical. With the advent of high-performance computing, it is now possible to perform simulations with higher grid resolutions and longer simulation times, allowing for more accurate predictions. Additionally, the development of advanced numerical algorithms, such as adaptive mesh refinement and implicit time integration, has enabled more accurate and efficient simulations of chemical reactions in CFD.
In conclusion, modeling chemical reactions in CFD is a complex and challenging task. Accurately modeling the turbulence-chemistry interaction, properly accounting for the transport of different species, and accounting for the radiation effects on the flame front are only a few of the challenges. However, with advancements in computing power and numerical algorithms, these challenges can be overcome, leading to more accurate and practical models of chemical reactions in CFD.
Investigating the Applications of Chemically Reacting Flow Models in Industry
Chemically reacting flow models in CFD have revolutionized the way we approach industrial processes, enabling us to optimize designs and improve efficiency. These models have a wide range of applications in various industries, including:
Combustion systems:
These models are extensively used in combustion systems to optimize fuel injection and combustion airflows while minimizing pollutant emissions. By simulating the combustion process, engineers can identify potential areas for improvement and make adjustments to the system to achieve optimal performance.
Chemical processing:
Chemical processing engineers can use these models to optimize reactor designs and identify potential process improvements. By simulating the chemical reactions taking place in the reactor, engineers can identify the optimal conditions for the process to take place and make adjustments to the design accordingly.
Materials synthesis:
These models have also been used in the design of materials synthesis processes, such as catalytic converters for automobiles and other industrial applications. By simulating the chemical reactions taking place during the synthesis process, engineers can identify the optimal conditions for the process to take place and make adjustments to the design accordingly.
Conclusion
Overall, chemically reacting flow models have revolutionized the way we approach industrial processes, enabling us to optimize designs and improve efficiency. As technology continues to advance, we can expect to see even more applications for these models in the future.
The use of chemically reacting flow models in CFD has proven to be a powerful tool for simulating and predicting the behavior of chemical reactions in a variety of industrial processes. Understanding the different modeling approaches, challenges, and applications of these models can provide researchers and engineers with the insight needed to optimize processes, improve efficiencies, and minimize environmental impact.