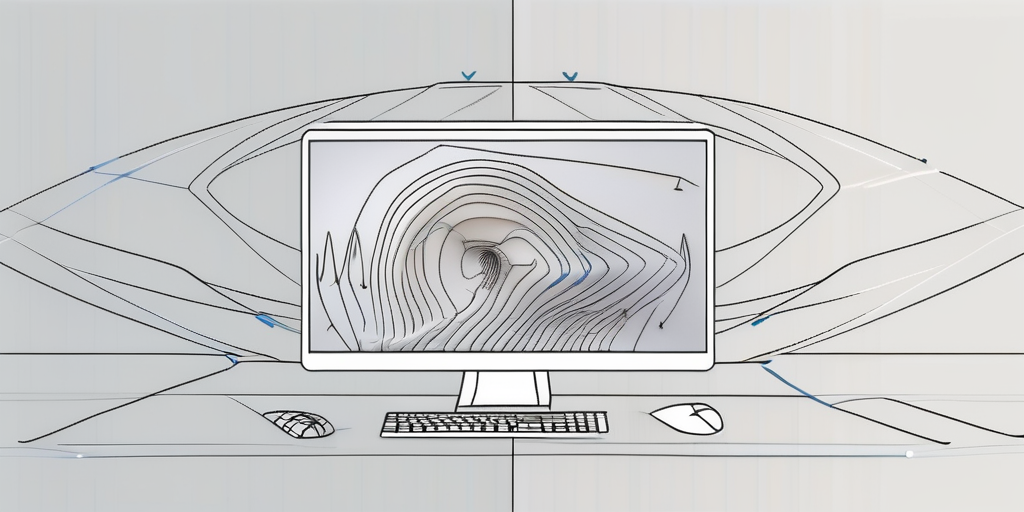
An Introduction to Setting Up a CFD Simulation in Commercial Software
How to Setup a CFD Simulation
Computational Fluid Dynamics (CFD) is a powerful tool used by engineers and scientists to analyze and simulate fluid flow behavior. Setting up a CFD simulation can be a complex process that requires careful planning and execution. In this article, we will discuss the step-by-step process of setting up a CFD simulation, covering important considerations and best practices to ensure accurate and reliable results.## Plan Your Model
Before diving into the simulation setup, it's crucial to have a clear understanding of your primary objectives and the system you want to simulate. This includes defining the boundaries of your model, selecting the appropriate physics, and determining the desired level of accuracy. By establishing these goals early on, you can efficiently allocate your resources and avoid unnecessary complexities later in the process.
When planning your model, consider the geometry you will be working with. If you are working with a complex three-dimensional shape, it may be beneficial to simplify it through approximation or decomposition into smaller parts. Remember that overly complex geometries can significantly increase computational costs and simulation time.
Furthermore, it is important to consider the material properties of the objects in your model. Different materials exhibit different behaviors under various conditions, and accurately representing these properties is crucial for obtaining meaningful simulation results. Take into account factors such as elasticity, thermal conductivity, and viscosity, depending on the nature of your simulation.
In addition to geometry and material properties, you should also consider the boundary conditions of your model. These conditions define how the system interacts with its surroundings and can have a significant impact on the simulation results. Examples of boundary conditions include fixed constraints, applied forces, and prescribed displacements. Carefully defining these conditions will ensure that your simulation accurately represents the real-world scenario you are trying to model.
Another aspect to consider when planning your model is the time frame of your simulation. Are you interested in studying the system's behavior over a short period or a long period? This will determine the time step size and the total simulation time. It's important to strike a balance between accuracy and computational efficiency, as smaller time steps and longer simulation times can increase the computational cost.
Lastly, don't forget to consider the computational resources available to you. Simulating complex models with high levels of accuracy can require significant computational power and memory. Make sure you have access to the necessary hardware or cloud computing resources to handle the computational demands of your simulation.
Import Geometry
The next step in setting up a Computational Fluid Dynamics (CFD) simulation is importing the geometry into your chosen CFD software. This crucial step allows you to define the physical boundaries and shapes of the objects that will be analyzed in the simulation.
There are two main methods for importing geometry into CFD software. The first method involves directly importing a Computer-Aided Design (CAD) file. This file contains detailed information about the geometry, such as the shape, size, and position of the objects. By importing a CAD file, you can save time and effort by utilizing the pre-existing geometry.
The second method involves creating the geometry within the CFD software itself. This can be done using various modeling tools provided by the software. While this method requires more time and effort, it allows for greater control and customization of the geometry.
Regardless of the method chosen, it is essential to ensure that the imported geometry is clean, free of inconsistencies, and properly connected. Inconsistencies in the geometry can lead to inaccurate simulation results and may cause the simulation to fail. Therefore, it is crucial to carefully inspect the imported geometry and make any necessary adjustments.
Once the geometry is imported, it is important to double-check for any open surfaces or gaps that might cause issues during the simulation setup. Open surfaces or gaps can lead to the leakage of fluid or incorrect flow behavior, compromising the accuracy of the simulation results. Identifying and repairing these issues early on can save you valuable time and effort later in the simulation process.
In conclusion, importing geometry into your CFD software is a critical step in setting up a simulation. Whether you choose to import a CAD file or create the geometry within the software, ensuring the cleanliness and connectivity of the geometry is essential for accurate and reliable simulation results.
Select Physics and Meshing
Now that you have a clean geometry, it's time to select the physics and meshing techniques that will best represent your system. This involves choosing the appropriate turbulence model, heat transfer model, and any other relevant physical phenomena that you want to include in your simulation.
When it comes to selecting the turbulence model, you have several options to consider. If your flow is laminar, you can use a simple model like the laminar flow model, which assumes a smooth and orderly flow. However, if your flow is turbulent, you might need to use more advanced turbulence models, such as the Reynolds-averaged Navier-Stokes (RANS) models or the large eddy simulation (LES) models. These models take into account the turbulent fluctuations and provide a more accurate representation of the flow behavior.
Heat transfer models are crucial for accurately capturing the thermal behavior of your system. Depending on the nature of your problem, you can choose between conduction, convection, and radiation heat transfer models. Conduction models are suitable for problems where heat transfer occurs primarily through solid materials, while convection models are used when heat is transferred through a fluid medium. Radiation models, on the other hand, are necessary when heat transfer occurs through electromagnetic waves.
Aside from turbulence and heat transfer models, there might be other physical phenomena that you want to include in your simulation. For example, if your system involves multiphase flows, you can select models that account for the interactions between different phases, such as the volume of fluid (VOF) or the Eulerian-Eulerian models. If your system involves combustion, you can choose combustion models that simulate the chemical reactions and heat release.
Meshing plays a crucial role in accurately representing the geometry and physics of the system. It involves discretizing the geometry into a grid of small cells that capture the local flow properties. A high-quality mesh is essential for obtaining reliable and accurate results.
When it comes to meshing techniques, there are several options available. Structured meshes consist of regularly shaped elements, such as quadrilateral or hexahedral cells, and are suitable for simple geometries. Unstructured meshes, on the other hand, consist of irregularly shaped elements, such as triangles or tetrahedra, and are more flexible for complex geometries. Using a combination of structured and unstructured mesh elements can help optimize the computational efficiency while maintaining accuracy.
During the meshing process, pay attention to the boundary layer resolution near the walls and regions of interest. These areas often require a finer mesh to capture the flow behavior accurately. By refining the mesh in these regions, you can ensure that the velocity and temperature gradients are properly resolved.
Additionally, it is important to verify that there are no highly distorted or tangled elements in the mesh. These elements can negatively impact the solution convergence and lead to inaccurate results. Mesh quality metrics, such as aspect ratio and skewness, can be used to assess the quality of the mesh and identify any problematic elements that need to be addressed.
In conclusion, selecting the appropriate physics and meshing techniques is crucial for accurately simulating your system. By carefully choosing the turbulence and heat transfer models, as well as considering other relevant physical phenomena, you can ensure that your simulation captures the real-world behavior. Additionally, paying attention to the mesh quality and resolving the boundary layers and regions of interest properly will help you obtain reliable and accurate results.
Define Boundary and Initial Conditions
With the mesh and physics selected, it's time to define the boundary and initial conditions for your simulation. This involves specifying the flow properties, such as velocity, pressure, and temperature, at the inlet and outlet boundaries. Additionally, you need to define the walls or other solid surfaces and assign appropriate boundary conditions.
Understanding the expected behavior of the system is crucial for defining proper initial conditions. These conditions represent the state of the system at the beginning of the simulation and can significantly affect the convergence speed and accuracy. Be sure to carefully consider factors such as the initial velocity profile, temperature distribution, and any other relevant parameters that may impact the solution.
Setup Plots and Data Analyses
Setting up proper plots and data analyses is essential for evaluating and interpreting the results of your CFD simulation. Most CFD software packages allow you to define specific quantities of interest, such as pressure distribution, velocity profiles, or temperature gradients, and conveniently visualize them throughout the simulation.
Consider creating plots and data analyses that effectively present the information you need to validate your simulation against experimental data or theoretical predictions. These visualizations can help you identify trends, anomalies, or areas where the simulation may be deviating from expectations.
In addition to visual analysis, it is advisable to extract and store numerical data for further post-processing or comparisons. This can include data such as maximum velocity, heat transfer coefficients, or any other relevant parameters specific to your simulation goals.
Conclusion
Setting up a CFD simulation requires careful planning, attention to detail, and a good understanding of the physics and system behavior. By following the step-by-step process outlined in this article, you can effectively set up a CFD simulation and obtain reliable and accurate results. Remember to continuously validate your simulation against experimental data or theoretical predictions to ensure its credibility. With practice and experience, you will become proficient in setting up CFD simulations and gain valuable insights into the behavior of fluid flows.