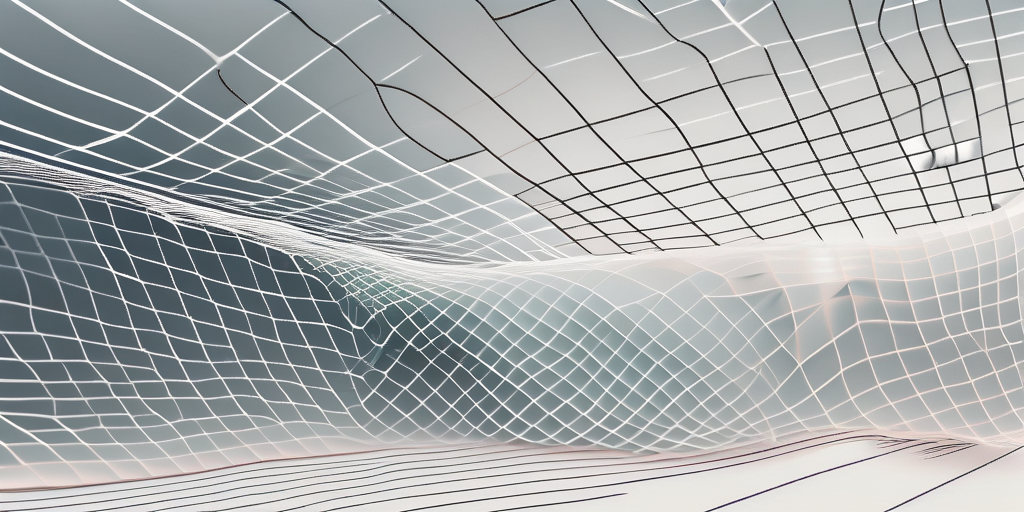
How to Create a CFD Mesh Using Commercial Software
How to Create a CFD Mesh
Creating a Computational Fluid Dynamics (CFD) mesh is an essential step in conducting fluid flow simulations. A well-designed mesh can greatly affect the accuracy and efficiency of the simulation results. In this article, we will explore the process of creating a CFD mesh, including importing geometry, selecting meshing models and parameters, and inspecting and revising the mesh.## Import Geometry
Before starting the meshing process, you need to import the geometry of the object or system you want to simulate. This geometry can be created using Computer-Aided Design (CAD) software or obtained from other sources. In most CFD software, you can import geometry files in popular formats such as STEP, IGES, or STL.
Importing the geometry is a crucial step in the simulation process as it provides the foundation for accurate and reliable results. The geometry represents the physical shape and dimensions of the object or system under investigation. It defines the boundaries and surfaces that will interact with the fluid flow or heat transfer.
When importing the geometry, it is essential to ensure that the file format is compatible with the CFD software being used. Different software packages may have specific requirements or limitations regarding the supported file formats. Therefore, it is advisable to check the software documentation or consult the software provider for guidance.
Once the geometry is successfully imported, you may need to make some adjustments or repairs to ensure that it is suitable for meshing. This step is necessary because the imported geometry may contain unnecessary features, complex geometry that could hinder the meshing process, or gaps and holes that need to be closed.
Removing unnecessary features involves identifying and eliminating any geometric details that are not relevant to the simulation. These features could include small fillets, chamfers, or intricate surface details that do not significantly impact the fluid flow or heat transfer behavior. By simplifying the geometry, you can reduce the computational effort required for meshing and subsequent simulations.
In some cases, the imported geometry may have complex shapes or intricate details that can cause difficulties during the meshing process. Simplifying the geometry can involve techniques such as smoothing or reducing the number of surface patches. By simplifying the geometry, you can create a more manageable mesh that accurately captures the essential features of the object or system being simulated.
In addition to simplification, it is crucial to ensure that the imported geometry is watertight. Gaps or holes in the geometry can lead to issues during meshing, such as the creation of invalid elements or leakage of fluid through unintended paths. Closing these gaps or holes involves carefully inspecting the geometry and using appropriate tools to fill or patch any openings.
Overall, the process of importing geometry for CFD simulations involves not only transferring the physical shape and dimensions but also preparing the geometry for meshing. This preparation step ensures that the subsequent meshing and simulation processes can be carried out smoothly and accurately, leading to reliable results and insights into the fluid flow or heat transfer phenomena of interest.
Select Meshing Models and Parameters
After importing the geometry, the next step is to select the meshing models and parameters. Meshing models determine the type and structure of the mesh, while parameters define the resolution and refinement level of the mesh elements.
There are various meshing models available, such as structured, unstructured, hybrid, or adaptive. Each model has its advantages and is suitable for specific types of simulations. The choice of meshing model depends on factors like geometry complexity and the desired accuracy of the simulation.
Structured meshing models are characterized by a regular arrangement of mesh elements, with each element having a consistent shape and size. This type of meshing is suitable for simple geometries with regular shapes, as it provides good control over element quality and computational efficiency. However, structured meshes may not be able to capture complex geometries accurately, as they lack flexibility in adapting to irregular shapes.
On the other hand, unstructured meshing models offer greater flexibility in capturing complex geometries. In this approach, the mesh elements can have different shapes and sizes, allowing for better resolution in areas of interest. Unstructured meshes are commonly used in simulations involving highly irregular geometries or intricate flow patterns. However, the irregular arrangement of mesh elements can lead to lower computational efficiency and challenges in maintaining element quality.
Hybrid meshing models combine the advantages of both structured and unstructured meshes. They use a combination of structured and unstructured elements to achieve a balance between accuracy and computational efficiency. Hybrid meshes are often employed in simulations where certain parts of the geometry require structured meshing for better control, while other areas benefit from the flexibility of unstructured meshing.
Adaptive meshing models take mesh refinement to the next level by dynamically adjusting the mesh resolution based on the solution's requirements. These models use error indicators to identify regions that require higher resolution and refine the mesh accordingly. Adaptive meshes are particularly useful in simulations with complex and evolving flow phenomena, as they allow for efficient use of computational resources while maintaining accuracy.
Additionally, you need to specify parameters such as element size, growth rate, and boundary layer thickness. The element size determines the size of the mesh elements, with smaller elements providing higher resolution but requiring more computational resources. The growth rate controls the transition between different element sizes, ensuring smooth transitions in areas of varying geometric complexity. The boundary layer thickness is essential for capturing boundary layer phenomena near solid walls.
Choosing the appropriate element size depends on the specific requirements of the simulation. Smaller element sizes are typically used in areas with high gradients or regions of interest, where capturing fine details is crucial. However, using excessively small elements throughout the entire mesh can lead to an excessive number of elements and increased computational cost. It is important to strike a balance between resolution and computational efficiency.
The growth rate parameter determines how the element size changes as the mesh moves from one region to another. A higher growth rate results in a more rapid transition, while a lower growth rate ensures a smoother transition. The choice of growth rate depends on the desired level of detail and the geometric complexity of the model. In areas with sharp changes in geometry, a lower growth rate may be necessary to accurately capture the flow behavior.
The boundary layer thickness parameter is crucial for simulations involving fluid flow near solid walls. The boundary layer is a thin layer of fluid adjacent to the wall, where the velocity profile changes from zero at the wall to the bulk flow velocity. Capturing the boundary layer accurately is essential for predicting flow separation, drag, and heat transfer. The boundary layer thickness parameter determines the number of mesh layers within the boundary layer, with a higher value providing better resolution.
Inspect and Revise
Once you have generated the initial mesh, it is crucial to inspect and revise it to ensure its quality. Mesh quality plays a significant role in the accuracy and stability of the simulation.
Inspecting the mesh involves checking for issues such as element skewness, aspect ratio, element size variation, and boundary conformity. Skewed elements, where the angles of the edges significantly deviate from perpendicular or parallel orientations, can lead to inaccurate results. Similarly, elements with extreme aspect ratios can adversely affect the simulation accuracy.
In addition to geometric considerations, it is essential to check the mesh for proper boundary conformity. The mesh should align with the boundaries of the object or system being simulated. Any gaps or overlaps between the mesh and the boundaries should be identified and addressed.
If any issues are identified during the inspection, revisions may be required. This could involve refining the mesh in specific regions, adjusting mesh parameters, or improving the geometry representation. Iterations of inspection and revision may be necessary to achieve a satisfactory mesh quality.
In conclusion, creating a CFD mesh involves importing geometry, selecting meshing models and parameters, and inspecting and revising the mesh. Successful mesh generation requires careful consideration of various factors, including geometry complexity, desired resolution, and mesh quality. With a well-designed mesh, you can obtain accurate and reliable results in your CFD simulations.