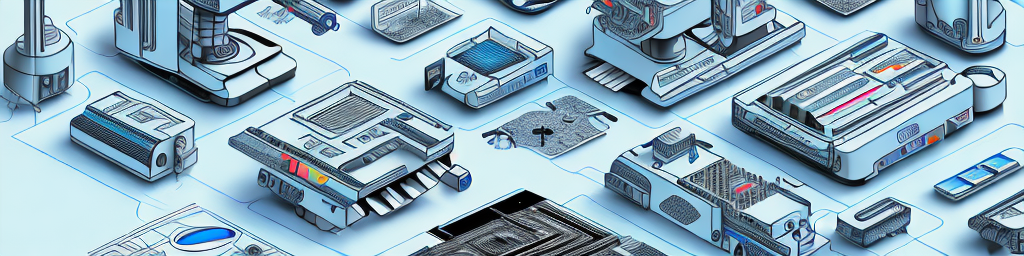
How to Automate the CFD Process
5 Ways Your CFD Process Can be Automated to Improve Efficiency
Computational Fluid Dynamics (CFD) is a powerful tool for simulating fluid dynamics in various industries. With the increasing complexity in product design and growing demand for faster production cycles, automation of the CFD process has become necessary to improve efficiency. In this article, we explore the benefits of automating your CFD workflow and present five ways to achieve this.
Before we dive into the ways to automate your CFD process, let's take a closer look at the benefits of automation. One of the main advantages of automating your CFD workflow is improved accuracy. When you rely on manual processes, there is always a chance of human error. However, by automating your CFD simulations, you can eliminate the possibility of human error and ensure that your results are accurate and reliable.
In addition to improved accuracy, automating your CFD process can also increase productivity. By reducing the time taken to run simulations, you can complete more simulations in less time, allowing you to test more design iterations and ultimately improve your product development process. This increased productivity can also help you stay ahead of your competition and bring your products to market faster.
Another benefit of automated CFD processes is that they are easy to reproduce. When you have a manual process, it can be difficult to reproduce the same results consistently. However, with an automated process, you can easily reproduce the same results every time, ensuring that your simulations are consistent and reliable.
Now that we've explored the benefits of automating your CFD workflow, let's take a look at five ways to get started. The first way to automate your CFD process is to use a software tool that offers automation capabilities. Many CFD software tools come with built-in automation features that can help you streamline your workflow and reduce the time taken to run simulations.
The second way to automate your CFD process is to use scripts. By writing scripts, you can automate repetitive tasks and reduce the likelihood of errors. Scripts can also help you automate the process of setting up simulations, which can be a time-consuming task.
The third way to automate your CFD process is to use cloud computing. By running your simulations on a cloud-based platform, you can reduce the time taken to run simulations and improve your overall productivity. Cloud computing also offers the benefit of scalability, allowing you to easily scale up or down depending on your needs.
The fourth way to automate your CFD process is to use machine learning. By using machine learning algorithms, you can automate the process of setting up simulations and improve the accuracy of your results. Machine learning can also help you identify trends and patterns in your data, allowing you to make more informed decisions.
The fifth and final way to automate your CFD process is to use a workflow management tool. Workflow management tools can help you automate your entire CFD process, from setting up simulations to analyzing results. These tools can also help you track your progress and identify areas for improvement.
In conclusion, automating your CFD process offers numerous benefits, including improved accuracy, increased productivity, and reduced product development costs. By using software tools, scripts, cloud computing, machine learning, and workflow management tools, you can automate your CFD process and take your product development to the next level.
Linking Geometry Parts to Downstream Objects and Actions
The first step in automating your CFD process is to create a link between geometry parts and downstream objects and actions. This link enables you to track and organize the changes made to the geometry and streamline the CFD process. The automated process ensures that downstream actions take place automatically when a specific geometry part changes, thus saving time and reducing the likelihood of errors.
When linking geometry parts to downstream objects and actions, it is important to consider the impact of any changes made to the geometry. For example, if a geometry part is modified, it may affect the downstream mesh, boundary conditions, and solver settings. By linking the geometry part to these downstream objects, any changes made to the geometry will automatically trigger updates to these downstream objects, ensuring that your CFD process remains accurate and efficient.
Additionally, linking geometry parts to downstream objects and actions can help you to better understand the impact of design changes on the overall CFD process. By tracking changes made to the geometry and the resulting updates to downstream objects, you can gain insight into how design changes affect the performance of your simulation. This information can be used to optimize your design and improve the accuracy of your CFD results.
Overall, linking geometry parts to downstream objects and actions is an essential step in automating your CFD process. By streamlining the process and reducing the likelihood of errors, you can save time and improve the accuracy of your simulations. So, take the time to set up these links and start reaping the benefits of an automated CFD process today!
Parameterization and Design Exploration
Parameterization is a key concept in computational fluid dynamics (CFD) that involves creating a set of independent variables that affect the output of a simulation. This approach enables engineers and designers to evaluate different design scenarios faster and more efficiently, as well as generate multiple geometries and run simulations automatically.
One of the benefits of parameterization is that it allows you to explore a wide range of design options without having to manually adjust each parameter or geometry. For example, you can easily change the size or shape of a component, adjust the flow rate, or modify the material properties of a fluid. By doing so, you can quickly evaluate the impact of these changes on the performance of your system.
Another advantage of parameterization is that it enables you to optimize your designs using advanced algorithms and optimization techniques. These algorithms can automatically adjust the values of your parameters to find the optimal solution based on a set of predefined objectives, such as minimizing pressure drop, maximizing heat transfer, or reducing turbulence. This approach can save you a significant amount of time and resources compared to manual optimization methods.
Design exploration is another important aspect of parameterization. This involves systematically exploring the design space to identify the best possible solutions based on a set of criteria. Design exploration can be performed using various techniques, such as sensitivity analysis, Monte Carlo simulations, and response surface modeling. These techniques can help you identify the most important parameters and their impact on the performance of your system.
In summary, parameterization and design exploration are essential tools for engineers and designers who want to optimize their designs and improve the performance of their systems. By using these techniques, you can save time and resources, explore a wide range of design options, and identify the best possible solutions based on a set of predefined objectives.
Templates and Scripts
Templates and scripts are powerful tools that can significantly speed up the computational fluid dynamics (CFD) process. In this section, we will explore how templates and scripts can be used to streamline the simulation setup and execution.
Templates
Templates are pre-defined simulation setups that can be easily modified and reused. They contain all the necessary information to define the simulation, including the boundary conditions, meshing parameters, and solver inputs. Templates can be created for various types of simulations, such as steady-state, transient, or multiphase simulations.
Using templates has several advantages. First, it saves time by eliminating the need to manually set up each simulation from scratch. Second, it ensures consistency across simulations, reducing the risk of errors and simplifying the validation process. Finally, it allows for easy modification of simulation parameters, such as changing the mesh size or the boundary conditions.
Scripts
Scripts are programs that automate the process of defining and executing simulations. They can be used to create and modify templates, execute simulations, and post-process results. Scripts can be written in various programming languages, such as Python, MATLAB, or FORTRAN.
Using scripts has several benefits. First, it eliminates the need for manual input of simulation parameters, reducing the risk of errors and saving time. Second, it allows for easy modification of simulation parameters, such as changing the mesh size or the solver settings. Third, it enables batch processing of simulations, which is useful for parameter studies or optimization tasks. Finally, it simplifies the post-processing of results, allowing for the creation of custom reports and visualizations.
Conclusion
Templates and scripts are essential tools for efficient and accurate CFD simulations. By using templates, you can easily create and modify simulation setups, ensuring consistency and saving time. By using scripts, you can automate the simulation process, reducing the risk of errors and enabling batch processing. Together, these tools can significantly speed up the CFD process, allowing for faster and more accurate simulations.
Next Level Post-Processing Automations
After running the simulations, post-processing is essential for analyzing and interpreting the results. Automating this process enables you to analyze the results faster and more efficiently. By script automation, you can perform tasks such as data collection, report generation, or visualizations that can take a lot of time if done manually.
One of the most significant benefits of automating post-processing is that it allows you to easily perform repetitive tasks. For example, if you need to generate a report for each simulation, you can create a script that automates this process. This script can collect the necessary data, generate the report, and even email it to the relevant stakeholders.
Another benefit of automating post-processing is that it can help you identify trends and patterns in your data. By automating the process of generating visualizations, you can quickly identify any anomalies or trends in your data. This can help you make more informed decisions and identify areas where further investigation is required.
Automating post-processing can also help you save time and reduce errors. By automating the process of collecting and analyzing data, you can reduce the risk of errors caused by manual data entry. Additionally, by automating the process, you can save time that would otherwise be spent on repetitive tasks, allowing you to focus on more important tasks.
Finally, automating post-processing can help you scale your analysis. As your simulations become more complex and generate more data, automating post-processing becomes increasingly important. By automating the process, you can quickly and easily analyze large amounts of data, allowing you to make more informed decisions and identify trends and patterns that would be difficult to identify manually.
Integrate with Third-Party Software
Integrating your CFD software with third-party software such as Excel or MATLAB can bring a whole new level of efficiency and productivity to your workflow. Not only does it automate the process of data transfer, analysis, and interpretation, but it also provides additional functionalities for evaluating, synthesizing, and visualizing the data.
For instance, Excel is a powerful tool for data manipulation and analysis. By integrating it with your CFD software, you can easily import simulation data into Excel and perform complex calculations, such as statistical analysis, regression analysis, and optimization. You can also create interactive charts and graphs to visualize the data and gain insights into the behavior of your fluid system.
On the other hand, MATLAB is a popular tool for numerical computation and data visualization. By integrating it with your CFD software, you can take advantage of its advanced algorithms and mathematical functions to perform complex simulations and data analysis. You can also create custom plots and animations to visualize the results and communicate your findings to others.
Moreover, integrating your CFD software with third-party software can help you to streamline your workflow and reduce the risk of errors. Instead of manually transferring data between different software programs, you can automate the process and ensure that the data is consistent and accurate across all platforms.
In summary, integrating your CFD software with third-party software can save you time, improve the accuracy of your results, and enhance your ability to communicate your findings to others. So why not give it a try and see how it can benefit your work?
Conclusion
In conclusion, automating your CFD process has numerous benefits that include increased efficiency, reduced costs, and improved accuracy. Implementing automation can be challenging, especially if you are new to the process, but the benefits are worth it. By implementing automation, you can focus more on the design aspects, reduce time spent on routine tasks, and make better decisions by evaluating more geometries and design iterations.