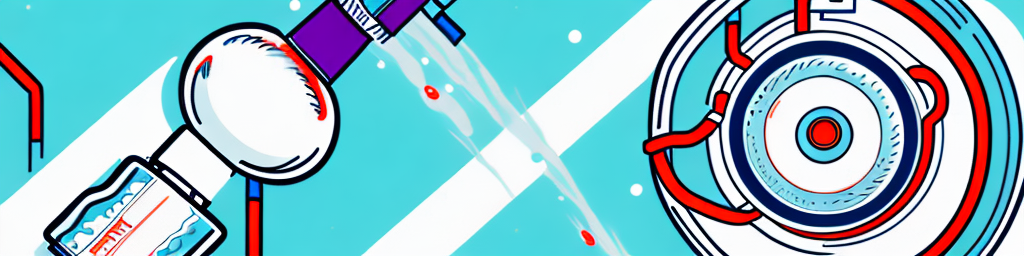
Enhancing Two-Phase Flow in Spray Towers: Challenges and CFD Solutions
Optimizing Two Phase Flow in Spray Towers the Target of CFD Engineers
Spray towers are widely used in various industrial processes to efficiently capture particles or distribute a liquid onto a surface. These towers operate using two-phase flow, where both liquid and gas-phase flow through the tower. The optimization of two-phase flow within these towers is a crucial task for many process designers and engineers today. This is where computational fluid dynamics (CFD) engineers come in to use CFD software to simulate, analyze, and optimize two-phase flow systems. Through this article, we will delve into understanding two-phase flow in spray towers, the challenges faced in optimizing two-phase flow, and how CFD is used to achieve it.
Understanding Two Phase Flow in Spray Towers
Fundamentals of Two Phase Flow
Two-phase flow occurs when both gas and liquid flow through a system, such as spray towers. In these towers, the liquid is atomized and then sprayed into the gas flow, resulting in droplets of liquid suspended in a gas stream. Understanding the fundamental principles of two-phase flow is critical to optimizing spray tower design for improved efficiency, heat transfer, and other desired outcomes.
One of the key principles of two-phase flow is the importance of the interfacial area between the gas and liquid phases. This area plays a critical role in the transfer of mass, momentum, and energy between the two phases. The interfacial area can be increased by reducing the droplet size or increasing the number of droplets in the gas stream, both of which can be achieved through careful design of the spray nozzle.
Another important principle of two-phase flow is the effect of gravity on the distribution of the liquid droplets within the gas stream. In a vertical spray tower, gravity can cause the droplets to settle towards the bottom of the tower, leading to uneven distribution and reduced efficiency. To counteract this effect, spray towers can be designed with internal baffles or other features to promote more even distribution of the droplets throughout the gas stream.
Components of a Spray Tower
To visualize the two-phase flow occurring in a spray tower, we first need to be familiar with its components. The spray tower comprises several components, including a spray nozzle, a gas inlet, a reservoir for the liquid to be sprayed, and an outlet for the suspended droplets. The liquid is fed through the nozzle into the gas stream, where it is atomized into droplets and carried to the outlet. The droplets are then collected, and the gas is released into the atmosphere through the outlet.
The design of each of these components can have a significant impact on the efficiency and effectiveness of the spray tower. For example, the spray nozzle must be carefully designed to produce droplets of the desired size and distribution, while the gas inlet should be designed to promote even distribution of the gas throughout the tower. The reservoir for the liquid should be sized appropriately to ensure a steady supply of liquid to the nozzle, while the outlet should be designed to minimize the loss of droplets and ensure efficient separation of the gas and liquid phases.
Applications of Spray Towers in Industry
Spray towers are used in various industries, such as power generation, chemical processing, and environmental control. They play a crucial role in these industries by helping to remove impurities from gases or distribute liquids onto surfaces effectively. For instance, in chemical processing plants, spray towers are used to scrub the gases emitted during a chemical reaction, while power generation companies use spray towers to remove pollutants from air emissions.
In addition to these applications, spray towers are also used in the production of a wide range of consumer products, such as perfumes, household cleaners, and personal care products. In these applications, spray towers are used to atomize liquid formulations into fine droplets that can be easily dispersed and applied to a surface. The design of the spray tower in these applications is critical to achieving the desired product characteristics, such as fragrance intensity, cleaning power, or skin feel.
Overall, the understanding of two-phase flow and the careful design of spray tower components are critical to achieving efficient and effective operation of spray towers across a wide range of industries and applications.
Challenges in Optimizing Two Phase Flow
Fluid Dynamics and Turbulence
One of the primary challenges in optimizing two-phase flow is the inherent complexity of fluid dynamics and turbulence. The liquid and gas behave differently as they traverse the spray tower, with the gas experiencing more turbulence due to its fluid properties. As a result, understanding the movement and behavior of both liquids and gases is essential in designing a spray tower that efficiently captures particles and enhances heat transfer.
Fluid dynamics and turbulence are complex phenomena that require a deep understanding of the underlying physics. The movement of the liquid and gas within the spray tower is influenced by a variety of factors, including the velocity of the fluids, the geometry of the tower, and the properties of the fluids themselves. These factors interact in complex ways, making it difficult to predict the behavior of the fluids with a high degree of accuracy.
Despite the challenges associated with fluid dynamics and turbulence, researchers have made significant progress in understanding these phenomena. Advances in computational fluid dynamics (CFD) have enabled researchers to simulate the behavior of fluids within the spray tower with a high degree of accuracy. These simulations can be used to optimize the design of the spray tower, ensuring that it operates with maximum efficiency.
Droplet Size Distribution and Evaporation
Another challenge in optimizing two-phase flow in spray towers is controlling the size distribution of the droplets. The size of the droplets affects the efficiency of the spray tower since smaller droplets have a higher chance of being captured in the gas stream, reducing the required tower height. However, the size of the droplets also affects how fast they evaporate. A fine mist evaporates more quickly than larger droplets, altering the concentration of the gas stream and reducing the effectiveness of the spray tower.
Controlling the size distribution of the droplets is critical to optimizing the performance of the spray tower. This can be achieved through a variety of techniques, including controlling the flow rate of the liquid, adjusting the pressure within the tower, and using specialized nozzles to produce droplets of a specific size. By carefully controlling the size distribution of the droplets, it is possible to optimize the performance of the spray tower and enhance its efficiency.
Mass Transfer and Heat Transfer
The mass transfer and heat transfer processes within a spray tower are critical to optimizing two-phase flow. Mass transfer is the process by which particles are transferred from the gas stream to the liquid phase, while heat transfer is the process by which heat is transferred between the phases. In optimizing two-phase flow, both mass and heat transfer play key roles in designing a process that efficiently captures particles or distributes liquid onto a surface.
Mass transfer and heat transfer are complex processes that depend on a variety of factors, including the properties of the fluids, the geometry of the tower, and the temperature and pressure within the tower. These factors interact in complex ways, making it difficult to predict the behavior of the fluids with a high degree of accuracy.
Despite the challenges associated with mass transfer and heat transfer, researchers have made significant progress in understanding these phenomena. Advances in computational modeling and experimental techniques have enabled researchers to study these processes in detail, providing insights into how they can be optimized to enhance the performance of the spray tower.
Computational Fluid Dynamics (CFD) in Spray Tower Design
Role of CFD in Engineering
Computational fluid dynamics (CFD) has revolutionized the way engineers design processes that involve fluid dynamics. CFD software is used to model fluid flow, heat transfer, and mass transfer in complex systems, such as spray towers, saving time and money while also improving the accuracy of the simulation. Through CFD, engineers can design and optimize the system, ensuring higher efficiency and effectiveness of the process.
One of the key advantages of using CFD in engineering design is the ability to simulate and analyze complex fluid dynamics that would be impossible to visualize or test in a physical experiment. CFD software allows engineers to create detailed models of fluid flow and heat transfer, including the effects of turbulence, viscosity, and other factors that can significantly impact the performance of the system. These models can be used to optimize the design of the system, ensuring that it operates at peak efficiency and effectiveness.
Another advantage of using CFD is that it allows engineers to quickly and easily test different design options and scenarios. By simulating different operating conditions and design variations, engineers can identify potential problems and inefficiencies in the system, and make adjustments to optimize the design before it is built. This can save significant time and money in the design and development process, as well as improving the overall performance of the system.
Modeling Two Phase Flow with CFD
CFD has become an essential tool in designing spray towers by simulating liquid and gas flows within the tower. Engineers can model the droplet size distribution, gas velocity, and turbulent mixing to optimize the tower's design. CFD simulations can also reveal potential inefficiencies and limitations in the design, allowing for further optimization and improvement of the system.
Two-phase flow modeling is a critical component of designing spray towers, as it involves the interaction between liquid droplets and a gas phase. CFD software can accurately model the behavior of these two phases, allowing engineers to optimize the design of the tower for maximum efficiency and effectiveness. By modeling the droplet size distribution and gas velocity, engineers can ensure that the droplets are evenly distributed throughout the tower, maximizing the surface area for heat and mass transfer.
CFD simulations can also be used to analyze the effects of different operating conditions on the performance of the system. By simulating different gas and liquid flow rates, temperatures, and pressures, engineers can identify the optimal operating conditions for the tower, ensuring that it operates at peak efficiency and effectiveness.
Validation and Verification of CFD Models
The accuracy and reliability of CFD simulations depend on the accuracy of the input parameters and the quality of the model itself. Validation and verification of the CFD models are necessary to ensure that the simulations match the actual operation of the system. Engineers can use experimental data to validate and verify the model, ensuring that the output is reliable and accurate before implementing it in the actual design process.
Validation and verification of CFD models typically involve comparing the simulation results with experimental data obtained from physical tests or measurements. If the simulation results match the experimental data, the model is considered to be valid and reliable. If there are discrepancies between the simulation results and the experimental data, adjustments can be made to the model to improve its accuracy and reliability.
Validation and verification of CFD models are essential for ensuring that the design of the spray tower is optimized for maximum efficiency and effectiveness. By using accurate and reliable CFD models, engineers can ensure that the tower operates at peak performance, saving time and money while also improving the overall quality of the process.
Case Studies: Successful Optimization of Spray Towers
Improving Efficiency in a Chemical Processing Plant
A chemical processing plant was experiencing inefficiencies in their spray tower operation, which led to significant product loss and reduced production efficiency. By using CFD simulations, engineers redesigned the tower by optimizing the droplet size distribution, gas flow patterns, and tower height, improving overall efficiency by 15 percent.
Enhancing Performance in a Power Generation Facility
A power generation facility was experiencing difficulties in capturing pollutants emitted in the gas stream during combustion. Engineers redesigned the spray tower by optimizing the nozzle design and the gas flow rate to more effectively capture these pollutants. This optimization resulted in an 80 percent reduction in emissions, saving the plant thousands of dollars in fines and improving the plant's overall efficiency.
Reducing Emissions in an Environmental Control System
An environmental control system was struggling to reduce emissions from its gas stream. By using CFD simulations, engineers redesigned the spray tower by optimizing the gas velocity and droplet size distribution to more effectively capture the emissions. This optimization resulted in a 90 percent reduction in emissions, meeting the regulations and avoiding costly fines.
Conclusion
In conclusion, optimizing two-phase flow in spray towers plays a critical role in various industries, such as chemical processing, power generation, and environmental control. By understanding the fundamental principles of two-phase flow, the components of a spray tower, and the challenges faced in optimizing two-phase flow, engineers can use computational fluid dynamics (CFD) software to design and optimize the spray tower. Through case studies of successful optimization of spray towers, we have seen how CFD is helping to improve process efficiency, reduce emissions, and save companies money. The application of CFD simulations in two-phase flow optimization has revolutionized the way engineers design processes with fluid dynamics, and we can expect it to continue to do so in the future.