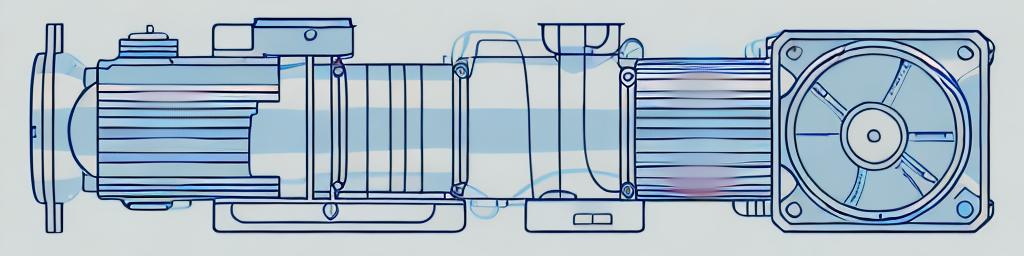
Revolutionizing Pump Design with CFD
Unlocking the Benefits of CFD in Pump Design
As the demand for more efficient, durable and reliable pumps increases, the use of Computational Fluid Dynamics (CFD) in pump design has become increasingly popular. CFD allows for a better understanding of fluid dynamics and the optimization of pump design.
Understanding the Basics of CFD in Pump Design
Computational Fluid Dynamics (CFD) is a simulation technology that uses numerical methods and algorithms to solve and analyze problems related to fluid flow and heat transfer. In pump design, CFD is used to simulate and analyze fluid flow inside a pump.
CFD works by breaking a fluid flow domain into small, discrete parts called cells or elements. These cells are then solved using numerical methods to calculate pressure, velocity, and other fluid properties. The results provide detailed insights into fluid flow and heat transfer behavior, which can be used to optimize pump performance and design.
Understanding the basics of CFD is essential for engineers involved in pump design. It enables them to create more efficient and reliable pumps that meet the specific needs of their applications.
What is Computational Fluid Dynamics (CFD)?
CFD is a technology used to simulate and analyze problems related to fluid flow and heat transfer. It uses numerical methods and algorithms to solve complex equations that govern fluid behavior, providing detailed information about fluid dynamics.
CFD has become an essential tool in pump design, enabling engineers to create pumps that are optimized for specific applications. It has revolutionized the field of fluid dynamics, allowing engineers to simulate and analyze complex fluid behavior that was previously impossible to model.
The Role of CFD in Pump Design
The design of efficient and reliable pumps is a complex process that requires a deep understanding of fluid dynamics. CFD allows for the simulation and analysis of fluid flow inside a pump, providing engineers with greater insight into the performance of pumps.
By using CFD simulations, engineers can optimize pump design to improve efficiency, reduce development time and costs, and enhance reliability and durability. CFD technology has revolutionized the way pumps are designed and manufactured, enabling engineers to create better pumps for specific applications.
CFD simulations can also be used to analyze the effects of different operating conditions on pump performance. This allows engineers to design pumps that are optimized for a range of operating conditions, improving their versatility and usefulness.
Key Terminology and Concepts in CFD
There are several key concepts and terminology related to CFD that are important to understand in pump design. These include Reynolds number, turbulence modeling, boundary conditions, and mesh generation. By mastering these concepts, engineers can optimize pump design through analysis in CFD simulations.
The Reynolds number is a dimensionless quantity that is used to predict the onset of turbulence in fluid flow. Turbulence modeling is the process of simulating turbulent flow in CFD simulations. Boundary conditions define the behavior of fluid at the boundaries of the simulation domain. Mesh generation is the process of creating a discrete representation of the fluid flow domain in CFD simulations.
By understanding these key concepts and terminology, engineers can create more accurate and reliable CFD simulations, leading to better pump design and performance.
Advantages of Using CFD in Pump Design
When it comes to designing pumps, engineers have a lot to consider. They need to ensure that the pump is efficient, reliable, and durable, while also meeting the specific needs of the industry or application it will be used in. Fortunately, the use of computational fluid dynamics (CFD) has revolutionized pump design, providing engineers with a powerful tool for optimizing pump performance and reducing development time and costs.
Improved Efficiency and Performance
One of the primary advantages of using CFD in pump design is the ability to analyze and optimize pump performance for maximum efficiency. By creating a digital model of the pump and simulating fluid flow through it, engineers can identify areas of turbulence and pressure drop that may be impacting performance. With this information, they can refine the geometry of the pump to improve flow efficiency, resulting in a more effective and efficient pump.
For example, CFD simulations can help engineers identify areas of recirculation within the pump that are reducing flow efficiency. By adjusting the geometry of the pump to minimize these areas, engineers can improve flow efficiency and increase the overall performance of the pump.
Reduced Development Time and Costs
Another major advantage of using CFD in pump design is the ability to reduce the time and cost needed to develop and test prototypes. Traditional pump design methods often require the creation of physical prototypes for testing, which can be time-consuming and expensive. With CFD simulations, however, engineers can create and test multiple design options digitally, allowing them to optimize pump design and reduce the number of physical prototypes needed.
Furthermore, CFD simulations can be run quickly and efficiently, allowing engineers to test a wide range of design options in a short amount of time. This can significantly reduce the overall development time and costs associated with pump design.
Enhanced Reliability and Durability
CFD simulations can also provide engineers with valuable information on how different design options perform under a range of conditions. This can help to identify potential issues with pump reliability and durability and improve design accordingly, resulting in more reliable and durable pumps.
For example, CFD simulations can help engineers identify areas of high stress within the pump that may be causing premature wear or failure. By adjusting the design of the pump to reduce stress concentrations, engineers can improve the reliability and durability of the pump.
Optimized Design for Specific Applications
Finally, CFD simulations can be tailored to specific applications, allowing engineers to optimize pump design for maximum effectiveness in particular environments or operating conditions. This leads to pumps that are better suited to the specific needs of a wide range of industries, including oil and gas, mining, and water treatment.
For example, CFD simulations can help engineers optimize pump design for use in corrosive environments by identifying materials and coatings that will provide the necessary protection against corrosion. Similarly, CFD simulations can help engineers optimize pump design for use in high-temperature environments by identifying materials and cooling methods that will prevent overheating and damage to the pump.
Overall, the use of CFD in pump design provides engineers with a powerful tool for optimizing pump performance, reducing development time and costs, improving reliability and durability, and tailoring design to specific applications. As such, it has become an essential part of modern pump design and is likely to continue to play a significant role in the industry for years to come.
CFD Simulation Process in Pump Design
Pre-processing: Geometry and Mesh Generation
The first step in the CFD simulation process is pre-processing, where the geometry of the pump is created and meshed. The geometry is created using computer-aided design (CAD) software, which allows engineers to accurately model the pump's geometry in a virtual environment. The mesh is then generated by dividing the geometry into a series of smaller, discrete elements, allowing for a more accurate analysis of fluid flow.
Solving: Fluid Flow and Heat Transfer Analysis
The next step in the CFD simulation process is solving, where the fluid flow and heat transfer equations are solved using numerical algorithms. The CFD software simulates fluid flow inside the pump, allowing engineers to analyze how different design options impact pump performance.
Post-processing: Visualization and Interpretation of Results
In the final step of the CFD simulation process, the results are visualized and interpreted. CFD software generates detailed graphical representations of fluid flow and heat transfer behavior, allowing engineers to interpret and understand the results of their analysis. These insights can then be used to optimize pump design for improved performance and efficiency.
Real-World Examples of CFD in Pump Design
Case Study 1: Improving Centrifugal Pump Efficiency
An engineering firm used CFD simulations to analyze and improve the design of a centrifugal pump used in a chemical processing plant. The simulations allowed the engineers to optimize the pump's geometry, resulting in a 10% increase in pump efficiency and a significant decrease in maintenance costs.
Case Study 2: Reducing Cavitation in Positive Displacement Pumps
A company involved in the production of sugar found that their positive displacement pumps were experiencing cavitation, which was causing significant maintenance issues. CFD simulations allowed engineers to optimize the pump design, resulting in a 15% increase in flow rate and a decrease in maintenance costs.
Case Study 3: Designing Custom Pumps for Unique Applications
CFD simulations allowed engineers to design custom pumps for unique applications, such as a pump used to transfer heat from a nuclear reactor to a cooling tower. The simulations allowed engineers to build an accurate virtual model of the pump and test its performance under extreme conditions, resulting in a pump design that met the specific needs of the application.
Conclusion
The use of CFD in pump design has revolutionized the way pumps are designed and manufactured. CFD simulations allow for detailed analysis of fluid flow inside a pump, resulting in optimized pump designs that are more efficient, reliable, and cost-effective. From reducing development time and costs to designing custom pumps for unique applications, CFD has unlocked significant benefits in pump design.