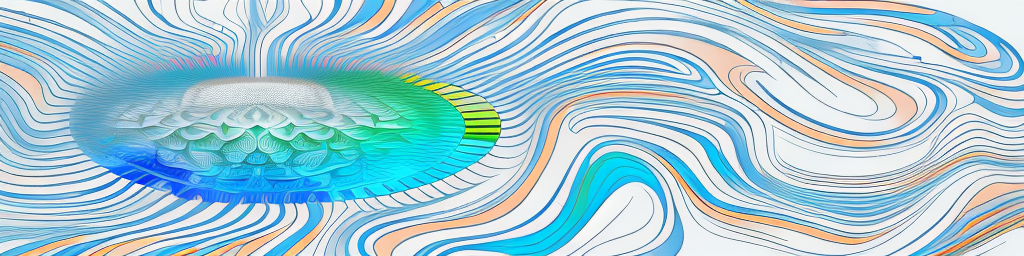
CFD-Enhanced Mixing Tanks: Revolutionizing Fluid Dynamics in Modern Industries
Mixing Tanks - An Age Old Technology Gets a Boost with Modern Computational Fluid Dynamics
Mixing tanks have been an essential component of many industries for centuries. These vessels have been used to mix a variety of substances, including chemicals, pharmaceuticals, and food. Despite their long history, however, mixing tanks have undergone a remarkable transformation in recent years with the integration of modern computational fluid dynamics (CFD) technology. In this article, we'll explore the evolution of mixing tank technology, the basics of CFD, and the benefits of modern mixing tanks with CFD. We'll also examine some real-world applications of CFD-enhanced mixing tanks and discuss the future of mixing tanks and CFD technology.
The History of Mixing Tanks
The use of mixing tanks dates back to ancient times when early civilizations mixed liquids and powders in simple vessels made from various materials, including pottery, stone, and metal. Over time, the design and construction of mixing tanks evolved, with new materials, shapes, and configurations.
As civilizations advanced, so did their need for more efficient and effective mixing tanks. The ancient Greeks, for example, were known to use mixing vessels made of clay and bronze to create perfumes, medicines, and other mixtures. These vessels were often decorated with intricate designs and symbols, showcasing the artistry and creativity of the time.
Early Mixing Tank Designs
Early mixing tanks consisted of simple vessels with nozzles for adding materials and stirring blades for mixing. These tanks were often made of wood or metal and required manual stirring, which was typically done with a hand-powered paddle or crank. The mixing process was highly labor-intensive and often resulted in inconsistent mixing quality.
One notable early mixing tank design was the "mortar and pestle," which was used by ancient Egyptians to mix herbs and spices for medicinal purposes. This design consisted of a bowl-shaped vessel made of stone or pottery and a hand-held tool made of wood or stone for grinding and mixing the ingredients.
Evolution of Mixing Tank Technology
The industrial revolution ushered in a new era of mixing tank technology, with the introduction of steam-powered and mechanical agitators. These innovations made the mixing process much more efficient and consistent, and they paved the way for future advancements in mixing tank technology.
With the advent of electricity in the late 19th century, mixing tanks became even more advanced. Electric motors replaced steam engines and hand-cranked paddles, and new materials such as stainless steel and fiberglass were used to construct the tanks. These advancements allowed for greater precision and control in the mixing process, leading to higher quality products in industries such as pharmaceuticals, food and beverage, and chemical manufacturing.
Today, mixing tanks come in a wide range of sizes, shapes, and configurations, from small laboratory-scale vessels to large industrial tanks that can hold thousands of gallons. They are used in a variety of industries, including cosmetics, biotechnology, and mining, and continue to be an essential tool for creating high-quality mixtures and products.
Understanding Computational Fluid Dynamics (CFD)
Computational Fluid Dynamics (CFD) is a computerized simulation technology used to model fluid dynamics in real-world applications. It is a powerful tool that can accurately predict the behaviors of fluids and their interactions with solid objects. CFD has become an integral part of many industries, including aerospace, automotive, and bioengineering, to name a few.
CFD is a complex field that requires a deep understanding of fluid mechanics, numerical methods, and computer programming. It involves the use of sophisticated algorithms and mathematical models to simulate the behavior of fluids in complex systems.
Basics of CFD
The basic concept of CFD is to break down a fluid system into a grid of cells and simulate the behavior of the fluid in each cell. This allows engineers to study the behavior of fluids in complex systems and make predictions about how they will behave under different conditions.
CFD simulations can be used to study a wide range of fluid phenomena, including laminar and turbulent flows, heat transfer, and chemical reactions. These simulations can provide valuable insights into the behavior of fluids in real-world applications and help engineers design more efficient and effective systems.
Applications of CFD in Various Industries
The applications of CFD are vast and varied. In the aerospace industry, CFD is used to simulate the airflow around aircraft and spacecraft, enabling engineers to optimize the aerodynamics for better performance and fuel efficiency. CFD is also used in the design of wind turbines, where it is used to optimize the placement and shape of the blades to maximize energy production.
In the automotive industry, CFD is used to simulate the airflow around vehicles and their components, enabling engineers to optimize the aerodynamics for better performance and fuel efficiency. CFD is also used to simulate the combustion process in engines, which can help improve fuel efficiency and reduce emissions.
In the healthcare industry, CFD is used to model the blood flow in arteries and veins, providing valuable insights into the diagnosis and treatment of cardiovascular disease. CFD is also used to simulate the flow of air in the lungs, which can help diagnose and treat respiratory diseases.
Overall, CFD is a powerful tool that has revolutionized the way engineers and scientists study fluid dynamics. Its applications are vast and varied, and it has become an essential tool in many industries.
The Integration of CFD in Mixing Tank Design
CFD or Computational Fluid Dynamics is a powerful tool used to simulate and analyze the behavior of fluids in mixing tanks. It is an ideal tool for modeling the complex interactions between fluids and solid objects, making it an essential tool for engineers designing mixing tanks.
CFD simulations can accurately predict the flow patterns of fluids and identify potential mixing issues, allowing engineers to optimize the design of mixing tanks for maximum efficiency and performance.
Advancements in Mixing Tank Simulations
The integration of CFD in mixing tank design has led to significant advancements in mixing tank simulations. With the help of CFD, engineers can now simulate the behavior of fluids in mixing tanks with a high degree of accuracy.
CFD simulations can provide detailed insights into the fluid flow, mixing efficiency, and heat transfer in mixing tanks. This information can help engineers identify potential problems and optimize the design of mixing tanks for maximum performance.
Improved Efficiency and Performance
The use of CFD in mixing tank design has led to improved efficiency and performance in many industries. By optimizing the design and configuration of mixing tanks, engineers can reduce energy consumption, improve mixing quality, and enhance product consistency and quality.
For example, in the food and beverage industry, CFD simulations can help engineers design mixing tanks that ensure consistent product quality and reduce the risk of contamination. In the chemical industry, CFD simulations can help engineers optimize the design of mixing tanks to improve the efficiency of chemical reactions.
Overall, the integration of CFD in mixing tank design has revolutionized the way engineers approach the design and optimization of mixing tanks. With the help of CFD, engineers can now design mixing tanks that are more efficient, effective, and reliable than ever before.
Benefits of Modern Mixing Tanks with CFD
Modern mixing tanks with computational fluid dynamics (CFD) have revolutionized the process of mixing fluids. They offer a wide range of benefits that make them ideal for many industries. These benefits include:
Enhanced Mixing Quality
One of the key benefits of modern mixing tanks with CFD is enhanced mixing quality. CFD simulations can accurately predict the mixing of fluids, ensuring a consistent and uniform product. The simulations can also help engineers determine the optimal mixing speed and duration, resulting in a better quality product.
For industries such as pharmaceuticals and food production, where the quality and consistency of the product are critical, modern mixing tanks with CFD are a game-changer. With CFD, engineers can ensure that the product meets the required specifications, reducing the risk of product recalls and improving customer satisfaction.
Reduced Energy Consumption
Modern mixing tanks with CFD are also more energy-efficient. By optimizing the design and configuration of mixing tanks, engineers can reduce energy consumption and minimize waste. CFD simulations can help identify areas of the tank where energy is being wasted or where the flow is not optimal, allowing engineers to make design changes that improve energy efficiency.
Reducing energy consumption not only saves money on energy bills but also helps companies meet their sustainability goals. By using less energy, companies can reduce their carbon footprint and contribute to a cleaner, healthier environment.
Optimized Tank Design and Configuration
The use of CFD in mixing tank design has led to optimized tank design and configuration. Engineers can design tanks that maximize the mixing efficiency while minimizing the risk of product contamination or production downtime. CFD simulations can help identify potential problems with the tank design before it is built, saving time and money on costly repairs or redesigns.
By optimizing the tank design and configuration, companies can improve their production processes, increase productivity, and reduce costs. They can also ensure that their products meet the required quality standards, reducing the risk of product recalls and improving customer satisfaction.
In conclusion, modern mixing tanks with CFD offer numerous benefits that make them ideal for many industries. Enhanced mixing quality, reduced energy consumption, and optimized tank design and configuration are just a few of the advantages that companies can enjoy by using modern mixing tanks with CFD.
Real-World Applications of CFD-Enhanced Mixing Tanks
CFD-enhanced mixing tanks are now being used in a variety of industries, from chemical and pharmaceutical to food and beverage. The use of these tanks has revolutionized the way products are made and has led to increased efficiency and cost savings.
Chemical Industry
In the chemical industry, CFD-enhanced mixing tanks are used to mix chemicals and produce a wide range of products, including pharmaceuticals, cleaners, and fertilizers. These tanks are designed to optimize mixing efficiency and quality, which can lead to increased production and reduced costs. Engineers can use CFD simulations to analyze the flow patterns within the tanks and optimize the design for maximum efficiency.
One example of the use of CFD-enhanced mixing tanks in the chemical industry is the production of fertilizers. By using these tanks, engineers can optimize the mixing of the various chemicals used in fertilizer production, resulting in a more consistent product. This can lead to increased crop yields and reduced costs for farmers.
Pharmaceutical Industry
Pharmaceutical companies use CFD-enhanced mixing tanks to produce drugs and other medical products. With enhanced mixing quality and performance, these tanks can help improve the efficiency and consistency of drug production. The use of CFD simulations allows engineers to optimize the design of the tanks to ensure that the drugs are mixed thoroughly and consistently.
One example of the use of CFD-enhanced mixing tanks in the pharmaceutical industry is the production of vaccines. By using these tanks, engineers can optimize the mixing of the various components of the vaccine, ensuring that the final product is consistent and effective. This can help to improve public health and save lives.
Food and Beverage Industry
The food and beverage industry also benefits from CFD-enhanced mixing tanks, which are used to produce foods, beverages, and other consumer products. By optimizing the mixing efficiency and quality, these tanks can help improve product consistency and quality.
One example of the use of CFD-enhanced mixing tanks in the food industry is the production of sauces and dressings. By using these tanks, engineers can optimize the mixing of the various ingredients, resulting in a more consistent and flavorful product. This can lead to increased customer satisfaction and brand loyalty.
In conclusion, CFD-enhanced mixing tanks have a wide range of real-world applications and are revolutionizing the way products are made in various industries. By optimizing mixing efficiency and quality, these tanks can lead to increased production, reduced costs, and improved product consistency and quality.
The Future of Mixing Tanks and CFD
The future of mixing tanks and CFD is an exciting one, with the potential for even more advanced technologies and innovations. Mixing tanks are used in a variety of industries, including chemical, pharmaceutical, and food and beverage, to mix substances and create products. Computational Fluid Dynamics (CFD) is a powerful tool that can be used to simulate and optimize mixing processes in these tanks.
Emerging Technologies and Innovations
New technologies and innovations, such as AI and machine learning, are being integrated into mixing tank design, offering the potential for even more precise and efficient mixing processes. AI algorithms can be used to analyze and optimize mixing parameters, such as impeller speed and tank geometry, to improve mixing efficiency and reduce energy consumption. Machine learning can be used to predict the behavior of different substances in the tank, allowing for more accurate and efficient mixing.
In addition to AI and machine learning, other emerging technologies are being used in mixing tank design. For example, 3D printing can be used to create custom impellers and other components, allowing for more precise and efficient mixing. Sensors and monitoring systems can be used to provide real-time feedback on mixing performance, allowing for adjustments to be made on the fly.
Challenges and Opportunities
As the demand for more efficient and effective mixing processes continues to grow, challenges and opportunities lie ahead. One challenge is the need to balance efficiency with product quality. In some cases, faster mixing can lead to lower product quality, so engineers must find the right balance between speed and quality.
Another challenge is the need to optimize mixing processes for different substances. Different substances have different properties, such as viscosity and density, which can affect mixing performance. Engineers must design mixing tanks that can handle a wide range of substances and optimize mixing processes for each one.
Despite these challenges, there are many opportunities for innovation in mixing tank design. By embracing new technologies and innovative approaches, engineers can continue to optimize mixing tank design and revolutionize the way we mix substances in the future. The potential benefits of more efficient and effective mixing processes are significant, including lower energy consumption, reduced waste, and improved product quality.