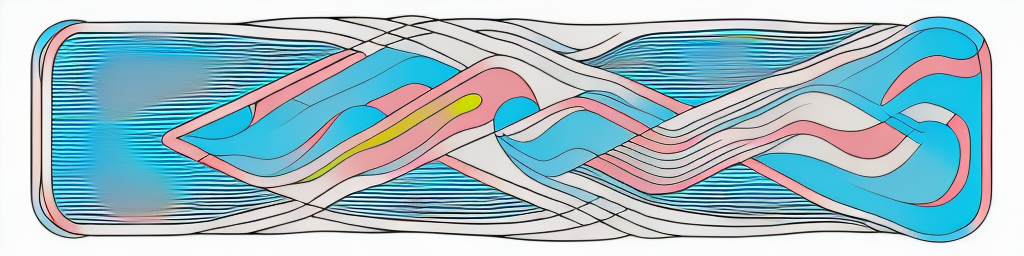
Advancing Heat Exchanger Performance through CFD Analysis
Engineers Pursue Improved Heat Exchanger Performance with CFD
Heat exchangers are an essential component in many industries, including chemical processing, power generation, and HVAC systems. They are responsible for transferring heat from one fluid to another, allowing for efficient energy usage and preventing equipment from overheating. However, the performance of heat exchangers can be improved using computational fluid dynamics (CFD) technology. In this article, we will explore the benefits and limitations of using CFD in heat exchanger design and review some case studies of successful implementation.
Understanding Heat Exchangers and Their Importance
Heat exchangers come in different types and sizes, each designed for a specific application. Their primary functions include transferring heat from one fluid to another, reducing energy consumption, and optimizing mechanical performance. Some common types of heat exchangers include plate heat exchangers, shell and tube heat exchangers, and air-cooled heat exchangers.
Plate heat exchangers are composed of multiple thin plates stacked together, allowing for a large surface area for heat transfer. They are commonly used in HVAC systems to regulate air temperature and in power plants to improve energy efficiency. The thin plates also make them ideal for use in the food and beverage industry, as they can be easily cleaned and sterilized.
Shell and tube heat exchangers have tubes that carry one fluid, surrounded by a shell that carries another fluid through it. They are commonly used in chemical processing plants, as well as in heating and cooling systems for buildings. The design of shell and tube heat exchangers allows for high heat transfer rates, making them efficient for large-scale applications.
Air-cooled heat exchangers use air as the cooling medium, removing heat through a fan or natural convection. They are commonly used in the oil and gas industry, as well as in power plants and chemical processing plants. Air-cooled heat exchangers are ideal for use in remote locations where water is scarce or unavailable.
Applications of Heat Exchangers
Heat exchangers have a wide range of applications, from cooling engines in vehicles to processing chemicals in industrial plants. They are essential in HVAC systems to regulate air temperature and in power plants to improve energy efficiency. Additionally, they play a crucial role in the food and beverage industry, where they help pasteurize liquids and preserve food products for longer periods.
In the automotive industry, heat exchangers are used to cool the engine and prevent overheating. This helps improve the performance and longevity of the vehicle. In the chemical processing industry, heat exchangers are used to control the temperature of chemical reactions, ensuring that they occur at the desired rate and producing high-quality products. In the pharmaceutical industry, heat exchangers are used to sterilize liquids and prevent contamination.
Challenges in Heat Exchanger Design
Heat exchanger design poses some challenges, including achieving optimal heat transfer efficiency while minimizing pressure drop and overcoming the limitations of the available materials. Engineers must also consider the cost and availability of materials, as well as factors such as corrosion, fouling, and vibration.
Corrosion can occur when the heat exchanger is exposed to harsh chemicals or high temperatures. This can cause the materials to degrade over time, reducing the efficiency of the heat exchanger. Fouling can occur when deposits build up on the surface of the heat exchanger, reducing the heat transfer rate. Vibration can also be a problem, as it can cause the heat exchanger to fail prematurely.
To overcome these challenges, engineers must carefully consider the design and materials used in the heat exchanger. They must also consider the operating conditions and maintenance requirements, ensuring that the heat exchanger remains efficient and reliable over its lifetime.
Introduction to Computational Fluid Dynamics (CFD)
CFD is a technology that simulates fluid flow and heat transfer in engineering designs. It is widely used in engineering and design optimization to improve performance and reduce costs. CFD simulation allows engineers to visualize fluid behavior, optimize design, and identify potential problems before fabrication or installation.
Basics of CFD
CFD simulations use mathematical models to describe fluid behavior, creating a virtual environment that mimics real-world conditions. These models simulate fluid behavior by measuring temperature, pressure, velocity, and other parameters at different points within the system.
Advantages of Using CFD in Engineering
CFD offers several advantages over traditional engineering design methods. It allows for efficient optimization of designs, reducing manufacturing costs while increasing performance. Additionally, CFD simulations can predict the behavior of complex fluid systems that are difficult or impossible to replicate in a lab environment.
Limitations of CFD
While CFD is a powerful tool for engineering design, it has certain limitations. Simulations often require significant computational resources, and the accuracy of the model depends on the quality and quantity of input data. Additionally, some physical phenomena, such as turbulence or complex chemical reactions, may be difficult to simulate accurately.
CFD Applications in Heat Exchanger Design
The use of CFD software in heat exchanger design can lead to significant improvements in performance and efficiency. By simulating the flow of fluid through heat exchangers, engineers can predict the effects of different designs and optimize them for maximum performance.
Optimizing Heat Transfer Efficiency
CFD simulations allow engineers to optimize heat transfer efficiency by modeling the flow of fluids through heat exchangers. By adjusting the design of the heat exchanger, the simulation can be used to find the optimal configuration for maximum heat transfer efficiency.
Reducing Pressure Drop and Energy Consumption
CFD simulations can also be used to reduce pressure drop and energy consumption. By optimizing heat exchanger design, engineers can minimize the pressure drop experienced by fluids as they pass through the system, reducing the energy required to operate the heat exchanger.
Enhancing Thermal Performance
CFD can also be used to enhance the thermal performance of heat exchangers. By simulating fluid behavior and optimizing the design, engineers can achieve more even distribution of heat across the exchanger, reducing the risk of hot or cold spots and increasing overall efficiency.
Case Studies: Successful CFD Implementation in Heat Exchanger Performance Improvement
Two successful case studies illustrate the benefits of using CFD to improve heat exchanger performance.
Plate Heat Exchangers
A company that manufactured plate heat exchangers wanted to improve the performance and reduce the size of its products. By using CFD software to simulate fluid flow and heat transfer, engineers were able to optimize the design of the heat exchangers, resulting in a 20% increase in efficiency and a 30% reduction in size.
Shell and Tube Heat Exchangers
An engineering consultancy was asked to optimize the performance of a shell and tube heat exchanger in a process plant. By analyzing flow patterns with CFD, the consultancy was able to identify a design flaw that was reducing the efficiency of the heat exchanger. By modifying the design, the consultancy was able to increase efficiency by 25% and reduce energy consumption by 20%.
Conclusion
CFD is a powerful technology that can significantly improve the performance and efficiency of heat exchangers. It enables engineers to create virtual models of fluid flow and heat transfer, facilitating the optimization of design parameters and identifying potential issues before they occur. By simulating fluid behavior, engineers can minimize the pressure drop, reduce energy consumption, and enhance the thermal performance of heat exchangers, resulting in significant cost savings and performance improvements.