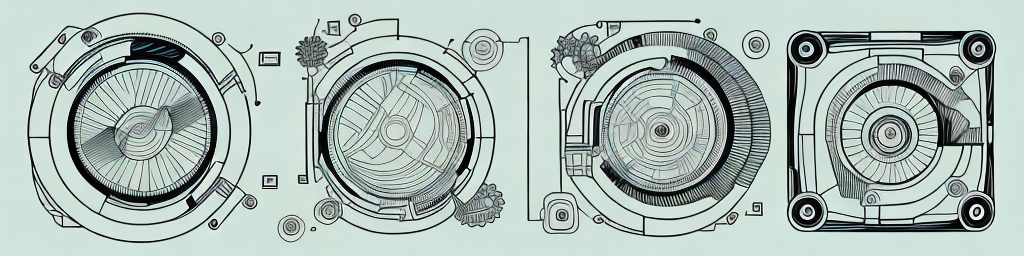
Elevating Fan Efficiency with CFD Models
Design Exploration within CFD Software will Deliver Higher Efficiency Industrial and Consumer Fans
Recent developments in computational fluid dynamics (CFD) software have made it possible for engineers to design fans that embody higher efficiency, improved performance, and longer service life. CFD simulates the fluid dynamics of air flowing through fans and enables the identification of areas for improvement in a fan's design.
Understanding the Importance of Fan Efficiency
Fan efficiency is an important consideration for many industries, including HVAC, aerospace, automotive, and consumer products. Fans are an essential component of many systems, and their energy efficiency can have a significant impact on the overall performance and cost of these systems. By designing fans that offer improved energy efficiency to reduce costs and environmental impact, engineers can deliver benefits to manufacturers, end-users, and society as a whole.
When it comes to fan efficiency, there are several factors to consider. These include the design of the fan blades, the motor's efficiency, and the system's overall airflow. By optimizing these factors, engineers can create fans that are more energy-efficient and cost-effective.
Energy Consumption and Cost Savings
One of the most significant benefits of improving fan efficiency is the potential for energy savings and cost reductions. By utilizing computational fluid dynamics (CFD) software, engineers can optimize fan design, which leads to increased energy efficiency, reduced costs, and lower energy consumption. CFD software simulates the airflow of fans, enabling engineers to study the fluid dynamics of air transport and identify areas for energy savings.
Improved fan efficiency can result in significant cost savings over the lifetime of a system. For example, a more energy-efficient fan can reduce electricity consumption, resulting in lower utility bills. Additionally, improved fan efficiency can reduce the wear and tear on other components of a system, leading to lower maintenance costs and longer service life.
Environmental Impact
In addition to cost savings, improving fan efficiency can also have a positive impact on the environment. CFD software can help minimize the environmental impact of fans by reducing energy consumption and waste, as well as minimizing carbon emissions by designing more efficient fans. By doing so, engineers can play an essential role in mitigating climate change.
Reducing energy consumption and waste can also help conserve natural resources, such as coal and natural gas, which are often used to generate electricity. By designing more energy-efficient fans, engineers can help reduce the demand for these resources, which can help preserve them for future generations.
Improved Performance and Longevity
Another benefit of improving fan efficiency is the potential for improved performance and longevity. By utilizing CFD software, engineers can identify areas for improvement in fans' design, leading to better performance and longer service life. Combining CFD simulations with material selection and engineering considerations can produce fans with improved performance and longevity.
Improved fan performance can lead to better airflow, which can result in better system performance overall. Additionally, longer service life can reduce the need for frequent replacements, resulting in lower costs and less waste.
Overall, improving fan efficiency can have significant benefits for manufacturers, end-users, and society as a whole. By reducing energy consumption, cost, and environmental impact, engineers can create fans that are more sustainable and cost-effective. Additionally, improved fan performance and longevity can result in better system performance and lower maintenance costs. As such, fan efficiency should be a key consideration for anyone involved in the design, manufacture, or use of fans in any industry.The Role of CFD Software in Fan Design
CFD software plays a critical role in helping engineers design fans that are more efficient, effective, and economical. When designing fans, engineers begin with a simulation of the airflow, which drives the optimization process.
Designing a fan is a complex process that requires careful consideration of multiple factors. Engineers must take into account the fan's intended use, the environment it will be operating in, and the materials it will be made of, among other things. CFD software helps simplify this process by providing engineers with a detailed simulation of the airflow, allowing them to make informed decisions about the design of the fan.
Simulating Fluid Dynamics
CFD software simulates fluid dynamics, reproducing the fan's performance characteristics, including airflow rate, pressure, and noise level. The simulation data enables engineers to validate their designs, understand the airflow behavior, and iterate on the design to improve it further.
Through the use of CFD software, engineers can visualize the airflow patterns within the fan, allowing them to identify areas of high turbulence or low pressure. This information is crucial in optimizing the design of the fan, as it enables engineers to make informed decisions about the placement and shape of the fan blades.
Analyzing Performance Metrics
The CFD simulation provides engineers with data to evaluate fan performance metrics like pressure, flow rate, and turbulence. By analyzing these performance metrics, they can determine the design elements that contribute to specific airflow characteristics and adjust the design accordingly.
For example, if the CFD simulation shows that the fan is producing excessive noise, engineers can adjust the shape of the fan blades or the angle of attack to reduce turbulence and noise. By making these small adjustments, engineers can significantly improve the performance of the fan, making it more efficient and effective.
Identifying Areas for Improvement
CFD software helps engineers identify areas for improvement in the fan design by providing crucial insights into the fan's performance. For example, it can show areas of excessive flow or turbulence, enabling engineers to optimize the fan design for maximum efficiency and effectiveness.
By using CFD software, engineers can also test the fan's performance under different operating conditions, such as changes in temperature or humidity. This information is essential in ensuring that the fan will perform as intended in real-world applications.
In conclusion, CFD software plays a critical role in the design of fans, enabling engineers to create more efficient, effective, and economical products. By simulating fluid dynamics, analyzing performance metrics, and identifying areas for improvement, engineers can optimize the design of the fan, ensuring that it will perform as intended in real-world applications.
Key Factors in Design Exploration for Higher Efficiency Fans
Designing higher efficiency fans requires practical insights into the design process. Here are some of the key factors that engineers need to consider when exploring designs for higher efficiency fans.
Blade Geometry and Aerodynamics
The shape and geometry of the fan blades play a vital role in determining the airflow rate and pressure produced by a fan. By optimizing blade designs, engineers can improve the fan's efficiency and reduce energy consumption.
One important factor in blade geometry is the angle of attack. The angle of attack is the angle between the blade and the oncoming air. By adjusting the angle of attack, engineers can improve the efficiency of the fan. Another important factor is the blade pitch. Blade pitch is the angle between the blade and the plane of rotation. By adjusting the blade pitch, engineers can optimize the fan's performance for a specific application.
Aerodynamics is also a critical consideration in fan design. By utilizing computational fluid dynamics (CFD) simulations, engineers can optimize the shape of the fan blades for maximum airflow and pressure. CFD simulations also allow engineers to evaluate the impact of different design parameters on fan performance, such as blade thickness, blade count, and blade curvature.
Material Selection and Weight Reduction
The materials used to construct the fan blades can also impact the fan's efficiency, longevity, and effectiveness. By choosing lightweight materials to reduce weight and, consequently, the load on the fan motor, engineers can improve the fan's performance and extend its lifespan.
One common material used in fan blade construction is aluminum. Aluminum is lightweight and has good thermal conductivity, making it an excellent choice for fan blades. However, other materials, such as carbon fiber and titanium, can offer even better performance in terms of weight reduction and strength.
Weight reduction is not the only consideration in material selection. The material's thermal properties, such as thermal conductivity and heat capacity, can also impact the fan's performance. By selecting materials with high thermal conductivity, engineers can improve the fan's heat dissipation capabilities, leading to better performance and longer lifespan.
Noise Reduction and Vibration Control
Fan noise and vibration can be significant issues in some applications. By utilizing CFD simulations, engineers can optimize blade geometry for reduced noise and vibration, leading to a more pleasant experience for the end-user.
One common method for reducing fan noise is to use a blade design with a low tip speed ratio. The tip speed ratio is the ratio of the blade tip speed to the free stream velocity. By reducing the tip speed ratio, engineers can reduce the noise generated by the fan.
Vibration control is also an important consideration in fan design. Excessive vibration can lead to premature failure of the fan and can cause noise and discomfort for the end-user. By optimizing blade geometry and material selection, engineers can reduce vibration and improve the fan's reliability.
In conclusion, designing higher efficiency fans requires careful consideration of a range of factors, including blade geometry and aerodynamics, material selection and weight reduction, and noise reduction and vibration control. By optimizing these factors, engineers can improve the fan's efficiency, reliability, and overall performance.
Case Studies: Successful Implementation of CFD Software in Fan Design
Here are some examples of how CFD software has been successfully utilized in industrial and consumer fan design.
Industrial Fan Efficiency Improvements
A manufacturer of large industrial fans used CFD software to optimize blade geometry and improve fan efficiency, leading to significant energy savings and reduced noise levels.
By using CFD simulations, the manufacturer was able to analyze the airflow patterns and identify areas of high turbulence and pressure drop. With this information, they were able to modify the blade geometry to reduce turbulence and minimize pressure drop, resulting in improved fan efficiency. The simulations also helped in identifying the optimal number of blades and blade angles, leading to further improvements in fan performance.
The energy savings achieved through these improvements were substantial, resulting in reduced operating costs for the manufacturer. Additionally, the reduced noise levels improved the working environment for employees.
Consumer Fan Innovations
An electronics company used CFD simulations to optimize blade design for a high-performance consumer fan. The resulting product was quieter and emitted less heat, leading to a more positive user experience.
Through the use of CFD software, the company was able to analyze the airflow patterns and identify areas of high turbulence and noise. Based on this information, they were able to modify the blade design to reduce turbulence and minimize noise levels. The simulations also helped in identifying the optimal blade speed and shape, leading to a more efficient and effective fan.
The resulting product was not only quieter and emitted less heat, but also had a longer lifespan due to the reduced wear and tear on the fan components. This led to increased customer satisfaction and loyalty.
Overcoming Design Challenges
An aerospace manufacturer used CFD software to overcome design challenges in designing an aircraft engine fan. The simulations provided insights into the airflow and enabled the optimization of blade geometry, material selection, and weight distribution, leading to improved engine efficiency and reduced fuel consumption.
The CFD simulations allowed the manufacturer to analyze the complex airflow patterns in the engine and identify areas of high turbulence and pressure drop. With this information, they were able to modify the blade geometry, select the optimal materials, and distribute the weight in the most efficient manner, resulting in improved engine efficiency and reduced fuel consumption.
The insights gained through the use of CFD software also allowed the manufacturer to identify potential design flaws before the fan was manufactured, saving time and resources. The resulting engine was more reliable and had a longer lifespan, leading to reduced maintenance costs for the airline.
In conclusion, the use of CFD software in fan design has led to significant improvements in efficiency, performance, and user experience. By analyzing complex airflow patterns and identifying areas of improvement, manufacturers have been able to optimize blade geometry, select optimal materials, and distribute weight in the most efficient manner. The resulting products have led to reduced operating costs, increased customer satisfaction, and improved reliability.
Conclusion
CFD software has revolutionized the process of designing higher efficiency fans. Through simulations, engineers can optimize the blade design, material selection, and performance characteristics of fans, leading to significant energy savings, reduced costs, and improved environmental impact. Implementing CFD simulations in fan design means achieving better outcomes and making significant strides towards sustainability and environmental responsibility.