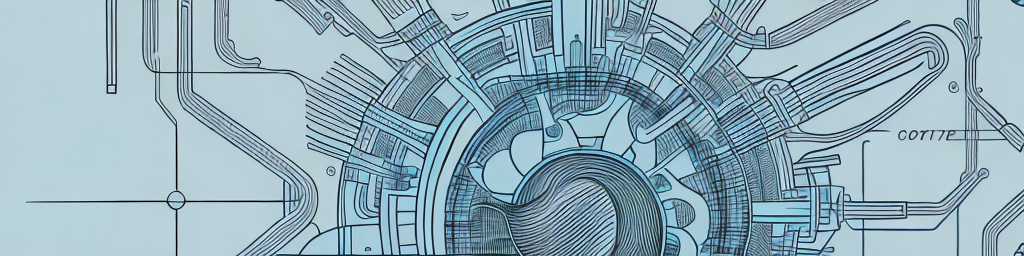
Boosting Horsepower: Engine Design Leveraging CFD
Engine Optimization
For car enthusiasts, increasing horsepower is a never-ending pursuit. Achieving maximum power output is a delicate balance between engine design, aerodynamics, and fuel efficiency. One of the most powerful tools available to engineers to optimize engine performance is Computational Fluid Dynamics, widely known as CFD. In this article, we will explore the basics of CFD in engine design and how CFD simulation techniques can be leveraged to improve horsepower and efficiency.
Understanding the Basics of CFD in Engine Design
What is Computational Fluid Dynamics (CFD)?
Computational Fluid Dynamics (CFD) is a computer-based simulation technique used to predict how fluids interact with objects. In the context of engine design, CFD can simulate the flow of air and fuel through the intake, combustion, and exhaust systems. By simulating these complex fluid dynamics, engineers can optimize the design of each component to achieve maximum power output and efficiency.
CFD has become an essential tool in engine design, allowing engineers to test and refine their designs without the need for expensive physical prototypes. With CFD, engineers can quickly evaluate the performance of multiple design options, making it possible to develop highly efficient and powerful engines in a fraction of the time it would take using traditional design methods.
The Role of CFD in Engine Performance Optimization
The primary role of CFD in engine design is to optimize the airflow through the engine to achieve maximum power output while minimizing energy losses due to friction and turbulence. By simulating the flow of air and fuel through the engine, engineers can identify areas of high pressure and turbulence that can reduce engine efficiency and performance.
CFD can also simulate the combustion process, providing insight into the best fuel injection and ignition timing strategies for improved engine performance and efficiency. By optimizing the combustion process, engineers can improve fuel efficiency, reduce emissions, and increase power output.
Another important role of CFD in engine design is to optimize the cooling system. High-performance engines generate a lot of heat, and effective cooling is essential to prevent overheating and engine damage. With CFD, engineers can simulate the flow of coolant through the engine and identify areas of high temperature that require additional cooling.
In summary, CFD is a powerful tool for engine design that allows engineers to optimize the airflow, combustion, and cooling systems of an engine for maximum power output and efficiency. By using CFD, engineers can develop highly efficient and powerful engines in less time and at a lower cost than traditional design methods.
Key Components of Engine Design for Increased Horsepower
When it comes to engine design, there are several key components that can be optimized to increase horsepower. In this article, we will explore four of these components in more detail.
Intake Manifold Design
The intake manifold is responsible for delivering air to the engine. Optimizing the shape and size of the intake manifold can significantly improve power output by ensuring a smooth, uninterrupted flow of air to the combustion chamber. There are several factors that can impact the design of the intake manifold, including the size of the engine, the intended use of the vehicle, and the desired power output.
One important consideration when designing an intake manifold is the length of the runners. Longer runners can help to increase low-end torque, while shorter runners are better suited for high-RPM power. Additionally, the shape of the intake manifold can impact the velocity and direction of the air entering the combustion chamber. By carefully designing the shape of the manifold, engineers can ensure that the air is delivered to the combustion chamber in the most efficient way possible.
Exhaust System Optimization
The exhaust system plays a critical role in removing burnt fuel and gases from the engine. A well-designed exhaust system minimizes backpressure and increases the flow of exhaust gases. This allows the engine to breathe more efficiently, which can increase horsepower and efficiency.
There are several factors that can impact the design of the exhaust system, including the size of the engine, the intended use of the vehicle, and the desired power output. One important consideration when designing an exhaust system is the diameter of the exhaust tubing. A larger diameter can help to reduce backpressure and increase flow, but may also reduce low-end torque. Similarly, the design of the muffler can impact the performance of the exhaust system, with straight-through designs typically offering the best flow and performance.
Cylinder Head and Combustion Chamber Improvements
The cylinder head and combustion chamber are at the heart of the engine. By improving the shape of the combustion chamber and valve timing, engineers can optimize the combustion process for maximum power output and efficiency. There are several factors that can impact the design of the cylinder head and combustion chamber, including the size of the engine, the intended use of the vehicle, and the desired power output.
One important consideration when designing the cylinder head is the shape of the combustion chamber. By carefully designing the shape of the combustion chamber, engineers can ensure that the fuel and air mixture is properly mixed and ignited for maximum power output. Additionally, the valve timing can impact the performance of the engine, with more aggressive camshafts typically offering increased power at high RPMs.
Turbocharging and Supercharging
Turbocharging and supercharging are two methods of forced induction that increase the power output of an engine by compressing the air before it enters the combustion chamber. CFD simulations can help engineers optimize the design of the turbocharger or supercharger to achieve maximum power output with minimal energy losses.
One important consideration when designing a turbocharger or supercharger system is the size of the unit. A larger unit can provide increased boost pressure, but may also increase lag time and reduce low-end torque. Additionally, the intercooler can impact the performance of the system, with larger intercoolers typically offering better cooling and increased power output.
By optimizing these key components of engine design, engineers can increase the power output and efficiency of an engine, providing drivers with a more exhilarating and enjoyable driving experience.
CFD Simulation Techniques for Engine Design
Mesh Generation and Quality
CFD simulations rely on a computational mesh to divide the fluid domain into discrete cells. The quality of the mesh can significantly impact the accuracy of the simulation. Engineers must carefully design the mesh to ensure it accurately represents the fluid domain while minimizing computation time.
Boundary Conditions and Solver Settings
Boundary conditions and solver settings are critical components that impact the accuracy and runtime of CFD simulations. Engineers must carefully select appropriate boundary conditions for each component of the engine and adjust solver settings to achieve accurate results efficiently.
Post-processing and Data Analysis
Once the CFD simulation is complete, engineers must analyze the data to inform design decisions. The simulations can provide insight into the airflow through different components of the engine, velocity profiles, and turbulence levels. Engineers can use this data to inform optimization strategies and identify potential improvements.
Real-World Applications of CFD in Engine Design
Case Study: Formula 1 Engine Development
Formula 1 engines operate at the peak of performance, achieving up to 14,000 RPM and producing over 1,000 horsepower. CFD simulations are a critical tool for optimizing engine design in this environment. By simulating the flow of air through the engine and minimizing energy losses, engineers can improve acceleration, speed, and handling.
Case Study: High-Performance Motorcycle Engines
Motorcycle engines are subject to strict weight and size limitations. This makes optimizing the engine design an even greater challenge. However, CFD simulations have proven to be an effective tool for addressing these limitations, allowing engineers to optimize components such as the intake manifold, exhaust system, and combustion chamber for maximum power output and efficiency.
Case Study: Improving Efficiency in Commercial Vehicle Engines
Improving fuel efficiency is a significant challenge for commercial vehicle manufacturers. By leveraging CFD simulations, engineers can optimize the design of the engine to minimize energy losses due to friction and turbulence. This can significantly improve fuel efficiency and reduce operating costs for fleet operators.
Conclusion
In conclusion, CFD simulations are a powerful tool for optimizing engine design for maximum power output and efficiency. By leveraging CFD simulations, engineers can design and optimize key components such as the intake manifold and combustion chamber, as well as improve fuel injection and ignition timing strategies. With the ability to simulate real-world conditions with precision, CFD simulations have revolutionized the engine design process, allowing for unprecedented performance gains and fuel efficiency improvements.