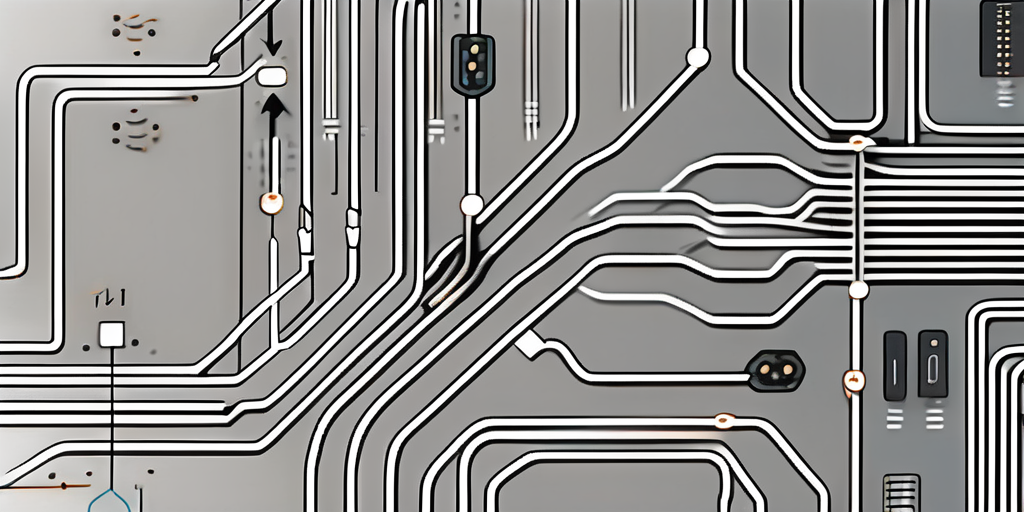
Verifying Printed Circuit Board (PCB) Thermal Performance with CFD
CFD for Printed Circuit Boards
Computational Fluid Dynamics (CFD) plays a crucial role in the design and analysis of printed circuit boards (PCBs), enabling engineers to optimize thermal management and airflow within these electronic systems. Understanding the basics of CFD and its significance in the electronics industry is essential for harnessing its potential in PCB design.## Understanding the Basics of CFD
Computational Fluid Dynamics, commonly known as CFD, is a computational analysis method used to simulate and analyze fluid flow, heat transfer, and other related phenomena. It employs mathematical models and numerical algorithms to solve complex equations, providing insights into fluid behavior and its impact on surrounding surfaces.
CFD has revolutionized the field of fluid dynamics by enabling engineers and scientists to study and predict fluid flow behavior in a wide range of applications. From designing efficient aircraft wings to optimizing the cooling of electronic devices, CFD has become an indispensable tool in various industries.
What is Computational Fluid Dynamics?
Computational Fluid Dynamics involves dividing a domain into a grid or mesh, discretizing the governing equations, and solving them iteratively. These equations describe the conservation of mass, momentum, and energy, allowing CFD to calculate fluid flow patterns, pressure distributions, and temperature distributions within a given system.
The process of CFD begins with defining the geometry of the system under study. This could be a simple object or a complex assembly of components. The geometry is then divided into small elements, forming a mesh. Each element represents a small portion of the system and is assigned properties such as velocity, pressure, and temperature.
Once the mesh is created, the governing equations, such as the Navier-Stokes equations, are discretized using numerical methods. These equations describe the fundamental principles of fluid flow and heat transfer and are solved iteratively to obtain a numerical solution.
CFD simulations require powerful computers and specialized software to perform the complex calculations involved. The accuracy of the results depends on the quality of the mesh, the chosen numerical methods, and the assumptions made in the mathematical models.
Importance of CFD in Electronics
In the realm of electronics, CFD plays a critical role in addressing the challenges associated with thermal management and airflow optimization. Electronics components generate heat during their operation, and effective thermal management is essential to ensure reliability and prevent premature failure.
By using CFD, engineers can analyze the heat dissipation capabilities of electronic devices and optimize their designs to enhance cooling efficiency. CFD simulations can predict temperature distributions, identify hotspots, and evaluate the effectiveness of different cooling strategies such as heat sinks, fans, and liquid cooling systems.
Furthermore, CFD can also be used to study the airflow patterns around electronic components and optimize the design of ventilation systems. By analyzing the flow of air, engineers can identify areas of low airflow and make design modifications to improve cooling performance.
Overall, CFD has become an invaluable tool in the electronics industry, enabling engineers to design more efficient and reliable electronic devices. By simulating and analyzing fluid flow and heat transfer, CFD helps optimize thermal management and airflow, ensuring the longevity and performance of electronic systems.
The Role of CFD in PCB Design
With the increasing power density and miniaturization of electronic components, optimizing heat dissipation and airflow within PCBs has become a key requirement. CFD offers unique insights into these aspects, enabling engineers to design cooling solutions that improve performance and reliability.
Heat Transfer and Thermal Management
Heat transfer is a dominant factor in PCB design, as excessive temperatures can degrade the performance and lifespan of electronic components. CFD allows engineers to analyze heat flow paths, locate hotspots, and evaluate the effectiveness of heat sinks, thermal vias, and other cooling strategies.
For example, CFD simulations can provide detailed information on the temperature distribution across the PCB, highlighting areas that may require additional cooling measures. By visualizing the heat flow paths, engineers can identify potential bottlenecks and optimize the placement of heat-generating components to ensure efficient heat dissipation.
Furthermore, CFD can help engineers evaluate the effectiveness of different cooling strategies. By simulating the performance of heat sinks, thermal vias, and other cooling mechanisms, engineers can make informed decisions on the most suitable solutions for their specific PCB design. This not only improves the thermal management of the PCB but also enhances the overall reliability and longevity of the electronic components.
Airflow Optimization in PCBs
In addition to managing heat, optimizing airflow within PCBs is crucial for dissipating heat effectively. CFD simulations can analyze the distribution of airflow, identify areas of low flow or recirculation, and help engineers improve the positioning of components and create efficient cooling channels.
By simulating the airflow patterns within the PCB, engineers can identify areas where the airflow is restricted or insufficient. This information can be used to redesign the PCB layout, adjust the positioning of components, or introduce additional cooling features to enhance airflow. CFD can also help engineers evaluate the impact of different fan configurations, duct designs, and vent placements on the overall airflow efficiency.
Moreover, CFD simulations can provide insights into the impact of external factors on the airflow within the PCB. By considering the influence of factors such as enclosure design, ambient temperature, and air inlet/outlet locations, engineers can optimize the overall cooling performance of the PCB.
In summary, CFD plays a crucial role in PCB design by enabling engineers to optimize heat dissipation and airflow. By analyzing heat transfer and thermal management, as well as airflow optimization, CFD simulations provide valuable insights that help improve the performance, reliability, and longevity of electronic components.
CFD Analysis Process for PCBs
The CFD analysis process for PCBs consists of several stages, including pre-processing, solving, and post-processing. Each step plays a vital role in ensuring accurate and reliable simulations.
Pre-processing in CFD Analysis
Pre-processing involves setting up the geometry of the PCB, defining boundary conditions, and meshing the domain. Accurate representation of the PCB geometry is crucial for obtaining realistic results. The mesh quality and resolution can significantly impact the accuracy and time required for the simulation.
Solving and Post-processing in CFD Analysis
The solving phase involves numerically solving the governing equations using appropriate numerical methods. Once the simulation is complete, post-processing techniques are employed to analyze and visualize the results, enabling engineers to gain insights into flow patterns, temperature distributions, and areas of concern.
Challenges in Implementing CFD for PCBs
Implementing CFD in PCB design is not without its challenges. Understanding and addressing these challenges is crucial for accurate and reliable simulations.
Complexity of Electronic Components
Electronic components, such as integrated circuits and power modules, possess intricate features and thermal characteristics that can influence the accuracy of CFD simulations. Modeling these components accurately requires detailed thermal and fluid behavior information.
Limitations of CFD Simulations
While CFD simulations offer valuable insights, they also have limitations. These include assumptions made during modeling, simplifications in boundary conditions, and uncertainties in material properties. Engineers must be aware of these limitations and consider them while interpreting results.
Future Trends in CFD for PCBs
The field of CFD for PCB design continues to evolve, with advancements in software and the integration of AI and machine learning techniques.
Advancements in CFD Software
CFD software providers are continuously improving their solutions, making them more user-friendly and capable of handling complex geometries and physics. These advancements empower engineers to simulate and optimize PCB designs with higher accuracy and efficiency.
Impact of AI and Machine Learning on CFD Analysis
AI and machine learning techniques are increasingly being integrated into CFD analysis. These technologies can help automate parameter selection, optimize designs, and enhance simulation capabilities by learning from past simulations. The integration of AI and CFD holds the potential to revolutionize PCB design processes.
In conclusion, CFD plays a critical role in the design and analysis of printed circuit boards. By understanding the basics of CFD, acknowledging its importance in the electronics industry, and leveraging its capabilities in PCB design, engineers can optimize thermal management, airflow, and overall performance. While challenges exist, ongoing advancements in CFD software and the integration of AI and machine learning offer promising avenues for future development.