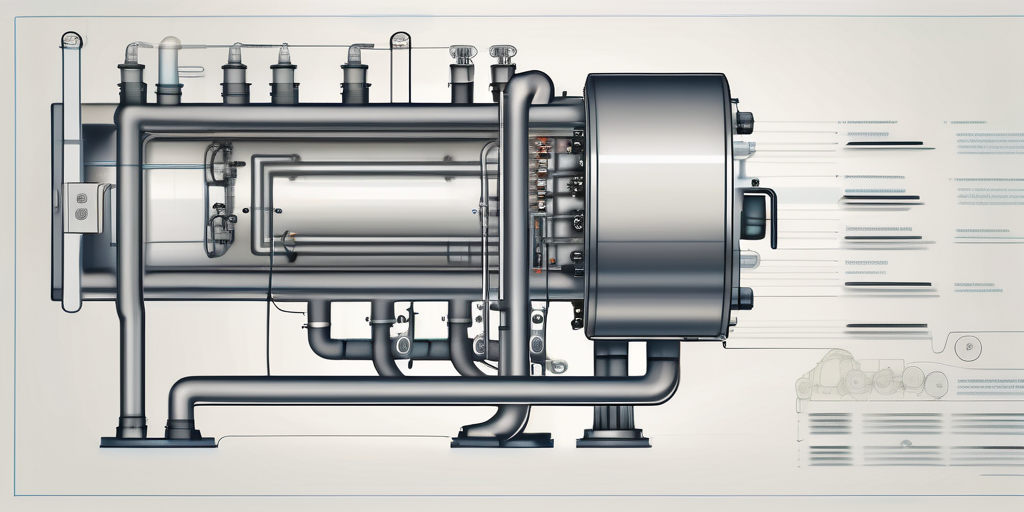
How Can CFD be Used in Steam Boiler Design?
CFD for Boilers
Computational Fluid Dynamics (CFD) is a powerful tool used in the design and optimization of boilers. By simulating the fluid flow, heat transfer, and combustion processes inside the boiler, CFD analysis can provide valuable insights into the behavior of boilers under various operating conditions. In this article, we will explore the use of CFD in understanding the thermal stresses experienced by steam tubes in boilers and the challenges associated with incorporating combustion, conjugate heat transfer, and multiphase fluid dynamics in the simulations. Finally, we will discuss the importance of optimizing boiler designs to minimize thermal stress.## CFD for Boilers
Boilers are integral devices used in numerous industrial processes, ranging from power generation to chemical production. They are responsible for converting water into steam, which can then be used for heating or as a source of energy. The efficient operation of boilers is crucial for the overall performance and reliability of these processes.
CFD simulations offer a comprehensive understanding of the fluid flow inside boilers, enabling engineers to optimize their designs. By modeling the complex interaction between the combustion gases, water, and heat transfer surfaces, CFD can accurately predict the boiler's performance and identify potential areas for improvement.
One of the key aspects of CFD for boilers is the accurate representation of the combustion process. Combustion is a complex chemical reaction involving the rapid oxidation of fuel in the presence of oxygen. CFD simulations can accurately capture the combustion process by solving the governing equations for mass, momentum, energy, and species transport. This allows engineers to analyze the distribution of temperature, species concentration, and heat release rate inside the boiler.
Another important factor in boiler performance is the heat transfer between the combustion gases and the water. CFD simulations can accurately model the convective heat transfer by solving the Navier-Stokes equations for fluid flow and the energy equation for heat transfer. This enables engineers to analyze the temperature distribution and heat transfer rates inside the boiler, helping them optimize the design of heat transfer surfaces such as tubes and fins.
CFD simulations also play a crucial role in understanding the fluid flow patterns inside the boiler. By solving the Navier-Stokes equations, engineers can analyze the velocity distribution, pressure drop, and turbulence characteristics of the flow. This information is vital for optimizing the design of flow passages, ensuring uniform flow distribution, and minimizing pressure losses.
Furthermore, CFD simulations can provide insights into the formation and behavior of pollutants such as nitrogen oxides (NOx) and carbon monoxide (CO) inside the boiler. By modeling the chemical reactions and transport processes, engineers can analyze the concentration distribution of pollutants and evaluate the effectiveness of emission control measures.
In addition to optimizing the design and performance of boilers, CFD simulations can also be used for troubleshooting and diagnosing operational issues. By comparing the simulation results with experimental data, engineers can identify the root causes of problems such as poor combustion, uneven heat distribution, or excessive pressure drop. This allows for targeted modifications and improvements to be made, leading to more efficient and reliable boiler operation.
Steam Tube Thermal Stress
The steam tubes in boilers are subjected to extreme temperatures, pressures, and temperature gradients. These conditions can induce thermal stresses, which over time, can lead to tube failures. Understanding and mitigating these thermal stresses is of utmost importance to ensure the reliable and safe operation of boilers.
CFD simulations play a crucial role in analyzing the thermal stresses experienced by steam tubes. By modeling the fluid flow, heat transfer, and temperature distribution inside the tubes, engineers can accurately quantify the magnitude and distribution of the thermal stresses. This information can then be used to optimize the tube geometry, material selection, and operational parameters to minimize the risk of failures.
Moreover, CFD simulations allow engineers to explore various design modifications, such as the inclusion of baffles or turbulence promoters, to enhance heat transfer and reduce thermal stress. By evaluating different design alternatives virtually, time and cost-intensive experimental prototypes can be minimized, resulting in more efficient and reliable boiler systems.
One particular challenge in steam tube thermal stress analysis is the presence of temperature gradients along the length of the tubes. These gradients can result in non-uniform thermal expansion, leading to additional stresses. To accurately capture these effects, engineers employ advanced numerical techniques, such as finite element analysis, to discretize the tubes into smaller elements and solve the governing equations for each element. This approach allows for a detailed understanding of the thermal stress distribution, enabling engineers to identify potential failure locations and take appropriate preventive measures.
Another important consideration in steam tube thermal stress analysis is the choice of materials. Different materials have varying coefficients of thermal expansion, which directly influence the magnitude of thermal stresses. Engineers must carefully select materials with suitable properties to ensure that the tubes can withstand the thermal loads without experiencing excessive stress. Additionally, the mechanical properties of the materials, such as yield strength and creep resistance, must also be taken into account to ensure long-term reliability.
In addition to CFD simulations and material selection, engineers also employ non-destructive testing techniques to assess the integrity of steam tubes. These techniques, such as ultrasonic testing and radiographic inspection, allow engineers to detect any defects or damage that may compromise the structural integrity of the tubes. By regularly monitoring the condition of the tubes, maintenance and repair activities can be planned in a proactive manner, minimizing the risk of unexpected failures.
Furthermore, advancements in sensor technology have enabled real-time monitoring of steam tube conditions during operation. By installing temperature and strain sensors along the length of the tubes, engineers can continuously monitor the thermal stresses and detect any abnormal behavior. This real-time data can be used to optimize operational parameters, such as steam flow rate and temperature, to minimize thermal stresses and prolong the service life of the tubes.
In conclusion, the analysis and mitigation of thermal stresses in steam tubes are crucial for the reliable and safe operation of boilers. Through the use of CFD simulations, advanced numerical techniques, appropriate material selection, non-destructive testing, and real-time monitoring, engineers can ensure that steam tubes are designed and operated within safe limits, minimizing the risk of failures and maximizing the efficiency and reliability of boiler systems.
Combustion + Conjugate Heat Transfer + Multiphase Fluid Dynamics = A Tough Challenge
Boiler simulations become particularly challenging when combustion, conjugate heat transfer, and multiphase fluid dynamics must be considered simultaneously. Combustion involves the complex chemical reactions between fuel and oxidizer, releasing heat that drives the steam production. Properly modeling this process in a CFD simulation requires accounting for combustion kinetics, species transport, and radiation effects.
In addition to combustion, the boiler's heat transfer mechanism is also crucial. The conjugate heat transfer occurring between the solid boiler components and the fluid flow should be accurately captured. This includes accounting for convective heat transfer, conductive heat transfer within the solid components, and radiative heat transfer between the surfaces.
Furthermore, many boiler systems involve multiphase fluid dynamics, where a mixture of gas and liquid flows through the system. Modeling and simulating the behavior of such flows require capturing the complex interfacial phenomena, such as phase change, droplet evaporation, and bubble formation.
Undoubtedly, incorporating combustion, conjugate heat transfer, and multiphase fluid dynamics in a single CFD simulation poses significant challenges. However, overcoming these challenges is crucial for accurately predicting the boiler's performance and ensuring its safe and efficient operation.
Optimizing for Minimizing Thermal Stress
To minimize the thermal stresses experienced by steam tubes, optimization techniques based on CFD simulations can be employed. By analyzing the results obtained from the simulations, engineers can identify potential design modifications or operational adjustments that can reduce the thermal stress levels.
For instance, adjusting the flow rates, tube geometries, or material properties can significantly impact the thermal stress distribution. By carefully analyzing the CFD results, engineers can identify the optimal combination of these parameters to minimize thermal stress while maintaining high performance.
Moreover, CFD simulations can also provide insights into the impact of transient operating conditions, such as startups or load changes, on the thermal stress levels. By considering these factors during the design phase, engineers can ensure that the boiler is robust enough to withstand the thermal stresses that may occur during its lifetime.
In conclusion, CFD analysis plays a pivotal role in understanding and optimizing the design of boilers. By simulating the complex fluid flow, heat transfer, and combustion processes, engineers can gain valuable insights into the thermal stresses experienced by steam tubes and identify areas for improvement. Overcoming the challenges associated with incorporating combustion, conjugate heat transfer, and multiphase fluid dynamics further enhances the accuracy and reliability of CFD simulations. By optimizing boiler designs to minimize thermal stress, engineers can ensure the safe and efficient operation of boilers in various industrial applications.